Titel: | Ueber Neuerungen im Hüttenwesen. |
Fundstelle: | Band 245, Jahrgang 1882, S. 333 |
Download: | XML |
Ueber Neuerungen im Hüttenwesen.
Mit Abbildungen auf Tafel 24.
(Fortsetzung des Berichtes S. 218 Bd.
244.)
Ueber Neuerungen im Hüttenwesen.
Der Fortschauflungsofen für Bleigeschicke von M. Derer zeichnet sich dadurch aus, daſs der den
Feuerraum A (Fig. 1 und
2 Taf. 24) und den 3m,5 langen, an der
Feuerbrücke 2m breiten Schmelzraum C enthaltende Theil des Ofens schmäler, aber länger
genommen ist als bei den bisher üblichen Fortschauflungsöfen und daſs das Gewölbe
doppelt geneigt ist, um hierdurch eine bessere Ausnutzung der Wärme zu erzielen. Der
Raum gegen die Fuchsbrücke B zu ist etwas verjüngt, um
die erzeugte Wärme zusammenzuhalten und den Schmelzraum in allen seinen Theilen
gleichmäſsig zu erhitzen. Der 0m,6 breite und 2m lange Feuerrost ist mit Ober- und Unterwind
versehen. Die heiſsen Gase gelangen aus dem Schmelzraume C in den 17m langen und 3m breiten Röstraum E.
Da aber diese Gase nur noch wenig freien Sauerstoff enthalten, welcher zur
oxydirenden Röstung nicht genügen würde, so wird durch das Gewölbe gleichmäſsig
vertheilt atmosphärische Luft mittels eines Gebläses zugeführt, welche in Kanälen
der Feuer- und Fuchsbrücke B und D vorgewärmt ist. Das Gasgemisch entweicht schlieſslich
durch den Fachskanal F zum Schornstein. (Oesterreichische Zeitschrift für Berg- und Hüttenwesen,
1881 S. 670.)
Vorrichtung zur Flugstaubablagerung der Gesellschaft des Emser Blei- und Silberwerkes in Ems.
Nach Versuchen von M. Freudenberg ist der Absatz von
Flugstaub abhängig von der Temperatur der Gase und der Gröſse der Wandflächen. Dem
entsprechend nimmt die Ablagerung in den oberen Kammerabtheilungen rascher ab als in
den unteren. Der Gehalt des Flugstaubes an Silber, Zink und Antimon ist am gröſsten
in der Nähe des Ofens und nimmt mit der Länge der Kanäle ab. Entnommene Proben
enthielten 60,5 bis 67 Proc. Blei, 3,2 bis 4,2 Proc. Zink, 0,003 Proc. Silber, 14,1
bis 14,8 Proc. Schwefelsäure, 5,4 bis 6,2 Proc. Schwefel, 1 bis 2,1 Proc. Eisenoxyd
und Thonerde, 5,8 bis 8 Proc. Kohle, 0,3 bis 0,4 Proc. Antimon, 0,16 bis 0,24 Proc.
Arsen und 0,6 bis 1,2 Proc. Kalk.
Es hat sich ferner gezeigt, daſs die in den Rauchkanälen als Flugstaub sich
ablagernden Metallmengen in gleichem Verhältniſs stehen zur Quadratfläche der
Kanalwandungen, daſs also in demselben Verhältniſs, in welchem die inneren Flächen
der Rauchkanäle zunehmen, auch eine Zunahme der als Flugstaub sich ablagernden
Metallmengen stattfindet. Am einfachsten und billigsten werden die inneren
Rauchkanal- bezieh. Rauchkammerflächen durch möglichst dünne Platten, Gewebe oder
Geflechte vergröſsert, welche, ohne daſs sie den Kanalquerschnitt wesentlich
verkleinern, parallel der Zugrichtung im Inneren der Kanäle bezieh. Kammern
angebracht werden. Dies geschieht nach dem Patente der genannten Gesellschaft (*D.
R. P. Kl. 40 Nr. 17513 vom 26. August 1881) durch Aufhängen dünner Eisenbleche, auch alter Trommel-
und Setzsiebe B (Fig. 3 und
4 Taf. 24) an Haken D. Zur Sicherung des
bereits abgelagerten Flugstaubes gegen weiteres Fortreiſsen durch den Zug sind in
Entfernungen von 3 zu 3m 0m,6 hohe Quermauern C
angebracht.
Griffith empfiehlt in der Berg-
und Hüttenmännischen Zeitung, 1882 S. 122 den in Fig. 5 und
6 Taf. 24 dargestellten Rauchcondensator A,
auf dessen Wasserfläche der durch Rohr e angesaugte
Hüttenrauch u. dgl. mittels Gebläse d durch Rohr c getrieben wird. Die Dämpfe treffen hier mit durch
Schnecke g zerstäubtem Wasser zusammen, steigen durch
die beiden von den Brausen f mit Wasser benetzten
Siebböden a und b auf und
entweichen schlieſslich durch Rohr h.
Die Kupferraffinerie in den Vereinigten Staaten
bespricht eingehend T. Egleston im Engineering and Mining Journal, 1882 Bd. 33 S. 167, 183
und 209. Es wird hierzu fast nur das gediegene Kupfer vom Obernsee verwendet,
welches jetzt in den 3 Werken zu Hancock, Detroit und Pittsburg so verarbeitet wird,
daſs im Flammofen reines Kupfer und reiche Schlacke erhalten werden. Zu Detroit und
Hancock werden dann die Raffinirschlacken und Krätzen im Schachtofen auf
Schwarzkupfer und arme Schlacken verarbeitet.
Die am Obernsee und zu Detroit für je 10t Rohkupfer
verwendeten Oefen sind 4m,3 lang und werden mit
Unterwind betrieben, unter Verwendung langflammiger Kohlen aus Ohio. Der mit
Aschenfall b versehene Feuerraum F (Fig. 7 und
8 Taf. 24) wird durch die Thür m beschickt,
der mit Arbeitsöffnung l versehene Schmelzherd H durch die Thür k,
während groſse Stücke durch eine Oeffnung im Gewölbe eingeführt werden, deren
bewegliches Gewölbe q durch Kettenträger x gehoben wird. In dem die Feuerung umgebenden
Mauerwerk befinden sich Luftzuführungskanäle a, in der
Feuerbrücke c der mit Regulirschieber s versehene Luftkanal e.
Die Gase entweichen durch Fuchs o zu dem 18m hohen Schornstein S.
Der Pittsburger Ofen (Fig. 9 bis
11 Taf. 24) ist diesem sehr ähnlich für 5t Kupfer ist der Herd H 2m,1 breit und 3m,3 lang. Zur Herstellung der Herde setzt man auf das Fundament ein 0,4 bis
0m,8 hohes Gewölbe u, bringt darauf ein 16 bis 20cm dickes
Bett von reichen Schlacken und Waschabgängen, darüber den eigentlichen Herd n aus Sand und Bruchkupfer. Man feuert zu diesem Zweck
20 Stunden lang, bringt dann auf den bloſsen Herd eine 0,6 bis 0m,9 hohe Schicht von scharfen gewaschenen
Fluſssand, erhitzt, gibt ihm mit einem Bleche die richtige Gestalt, klopft mit einem
Schlegel fest, schlieſst die Thüren, erhitzt den Herd 12 Stunden lang zur Weiſsglut,
bis der Sand zusammengesintert ist, läſst den Ofen 2 Stunden lang abkühlen und
bringt etwa 500k Bruchkupfer hinein. Hat sich das
geschmolzene Kupfer mit dem Sand gemischt, so kühlt man den Ofen ab, schöpft das
nicht in den Herd eingedrungene Kupfer möglichst aus und wiederholt das Verfahren 2
bis 3mal, bis das Bett
0,3 bis 0m,5 dick ist. Der alte Herd eines
Pittsburger Ofens enthielt:
Kupfer
31,76
Eisenoxyd
3,71
Manganoxyd
Spur
Blei
0,16
Kalk
1,05
Magnesia
0,12
Thonerde
3,83
Kieselsäure
58,91.
Die Pittsburger Oefen halten etwa 6 Monate.
Bei der Verarbeitung des Rohkupfers vertheilt man zunächst das feinkörnige Metall auf
dem Herde und bringt dann durch die Oeffnung des Gewölbes die dicken Stücke,
„Massen“ genannt, darauf. Am Obernsee besteht eine Beschickung aus
Rohkupfer, 25 bis 30 Proc. Kupfer enthaltenen Schlacken und Kalkstein. Eine solche
Beschickung enthält 8 bis 9l Erz mit 80 bis 85
Proc. Kupfer. Eine derartige in Pittsburg verwendete Schlacke ergab bei der
mechanischen Analyse 8,2 Proc. metallisches Kupfer und 91,8 Proc. Abgesiebtes;
letzteres bestand aus:
Eisenoxydul
7,71
Kupfer
18,78
Sauerstoff an Kupfer gebunden
4,74
Zinkoxyd
0,26
Nickeloxyd
0,34
Manganoxyd
0,07
Thonerde
13,48
Kalk
10,25
Magnesia
2,10
Kieselsäure
41,07
–––––
98,80.
Der geschlossene Ofen wird allmählich in Hitze gebracht, bis alles in Fluſs gekommen
ist, da bei rascher Temperatursteigerung die obere Schicht schmilzt und die untere
bedeckt, so daſs diese dann nur bei einem gröſseren Aufwand an Brennstoffen in Fluſs
kommt. Die beim Einschmelzen gebildete, meist 5 bis 14 Proc. Kupfer enthaltene
Schlacke wird 4 bis 6 mal ausgezogen und im Flamm- oder Schachtofen weiter
entkupfert. Fünf Schlackenproben aus Pittsburg hatten folgende Zusammensetzung:
I
II
III
IV
V
Metallisches Kupfer
3,40
0
3,37
0,51
0
Abgesiebtes
96,60
100,00
96,63
99,49
100,00
––––––––––––––––––––––––––––––––––––
100,00
100,00
100,00
100,00
100,00
––––––––––––––––––––––––––––––––––––
Das Abgesiebte:
Eisenoxydul
12,46
11,43
12,01
12,02
10,53
Kupfer
4,82
4,93
5,05
5,80
5,44
Sauerstoff im Kupfer
1,22
1,24
1,28
1,46
1,37
Zinkoxyd
0,37
0,56
1,52
0,75
0,43
Nickel
0,06
–
0,47
0,18
0,08
Manganoxyd
0,05
0,04
0,15
0,13
0,12
Thonerde
15,71
14,52
15,21
14,48
15,36
Kalk
14,34
14,75
14,79
15,25
11,81
Magnesia
4,07
3,99
4,11
3,90
2,57
Kieselsäure
45,32
46,94
45,81
44,66
49,83
––––––––––––––––––––––––––––––––––––
100,42
98,40
100,40
98,23
97,54.
Das Kupfer enthält jetzt etwa 0,72 Proc. Sauerstoff. Nun wird
unter Luftzutritt durch Gewölbe, Aschenfall und Feuerbrücke (vgl. Fig. 7) und
unter Umrühren das Kupfer weiter erhitzt (Verblasen), die entstehenden 12 bis 40
Proc. Kupfer enthaltenden Schlacken von Zeit zu Zeit abgezogen, um sie nebst den
Raffinirschlacken zur nächsten Beschickung zu geben, bis das Kupfer übergar ist,
d.h. etwa 1 Proc. Sauerstoff enthält. Nun wird durch Entfernung des Sauerstoffes
mittels Polen raffinirt, indem man die Oberfläche des Metalles völlig von Schlacke
reinigt, mit Kluftholz und Holzkohle bedeckt und den Polstab einsenkt. Alle 10 bis
15 Minuten werden Proben genommen, bis sich keine schwarzen Flecken mehr auf der
Bruchfläche zeigen, diese vielmehr sehnig und seidenglänzend ist. So oft Probe
genommen wird, nimmt man den Polstab heraus, entfernt die etwa entstandene Schlacke
und setzt wieder Kohle zu. Einige Werke setzen während des Raffinirens 0,05 bis 0,07
Proc. Blei hinzu, namentlich wenn das Kupfer zu Blech verarbeitet werden soll, und
wird dann der Polstab eingesetzt, sobald das auf dem Kupfer vertheilte Blei
geschmolzen ist. Bei einem Versuche betrug der Sauerstoffgehalt des Bades:
Vor Zusatz des Bleies
0,53
bis
0,55 Proc.
Nach „ „ „
0,55
Nach
10
Minuten
langem
Polen
0,56
„
15
„
„
„
0,44
bis
0,46
„
18
„
„
„
0,29
Beim Raffiniren ohne Blei:
I
II
III
IV
V
VI
Nach
30
Min.
langem
Polen
0,19
0,25
0,55
0,37
0,44
0,19
„
45
„
„
„
0,14
–
0,56
0,25
0,48
0,12
„
60
„
„
„
0,12
–
0,44
–
0,48
–
Das Polen geschieht bei möglichst hoher Temperatur und möglichst vollständigem
Luftabschluſs. Durch zu langes Polen wird das Kupfer brüchig, hellgelb, stark
glänzend und völlig spiegelnd. Ueberpoltes, anscheinend Kohlenstoff enthaltendes
Kupfer enthält aber immer noch etwas Sauerstoff. Bei Gegenwart von viel Kohlenstoff
und Sauerstoff bildet sich Kohlensäure, welche das Kupfer porös macht.
Das Ausschöpfen des mit Kohle bedeckt zu haltenden Kupfers geschieht unter
wiederholter Probenahme und bei möglichst neutraler Flamme, während auch wohl
Kluftholz auf der Oberfläche des Kupfers verbrannt wird. Der Sauerstoffgehalt des
Kupfers während des Ausschöpfens betrug:
I
II
III
IV
V
Bei Anfang
des
Ausschöpfens
0,10
0,24
0,60
0,22
0,11
Proc.
In der Mitte
„
„
0,12
–
0,19
0,41
0,10
Am Ende
„
„
0,10
0,30
–
0,43
0,12
Die Beschickung des Ofens und das Schmelzen nehmen etwa 12 Stunden in Anspruch, die
Entfernung der Schlacke 4 bis 5, das Verblasen 1,5 bis 2, das Raffiniren und das
Auskellen je 2 Stunden, das ganze Verfahren somit 22 Stunden, so daſs zur
Ausbesserung des Herdes etwa 2 Stunden übrig bleiben. Gefeuert wird jede Stunde
einmal.
Die reichen Schlacken werden am Obernsee in einem Schachtofen auf Schwarzkupfer und
absetzbare Schlacken verschmolzen, in Pittsburg erst im Flammofen und die dabei
erhaltenen reichen Schlacken im Schachtofen. In Hancock und Detroit werden die 5 bis
12 Proc. Kupfer enthaltenden Schlacken dem Schachtofen übergeben, der Kratz vom
Polen geht zum Raffinirofen, und zwar beträgt die im Schachtofen verschmolzene
Schlackenmenge etwa 35 Procent vom Gesammtgewicht der Beschickung des Raffinirofens.
Als Schachtofen wird namentlich ein entsprechend abgeänderter, 3m hoher Cupolofen von Mackenzie verwendet, mit elliptischem Querschnitt, dessen Mauerwerk mit
einem Eisenmantel versehen ist. Er hat in der Formgegend Wasserkühlung und zur
Windzuführung einen ringförmigen Schlitz. Die Beschickung besteht aus 7l Kohle, 20l
Schlacke und 8 bis 9l Kalk; dann setzt man etwa
0l,5 Kupferabfälle hinzu und bläst mit einer
45cm Wassersäule entsprechenden Windpressung.
In 10 Stunden schmilzt jeder Ofen 18 bis 20l
Schlacken durch, wobei die Schlacken abwechselnd durch 2 Augen in Behälter an der
einen Seite ausflieſsen, während das Kupfer an der entgegengesetzten Seite
abgestochen wird. Enthalten die Schlacken mehr als 0,75 Proc. Kupfer, so werden sie
nochmals verschmolzen. Jede Schmelzung gibt 29 bis 30l Schlacke und werden in 10 Stunden etwa 1000k Schwarzkupfer erhalten, welche mit dem Rohkupfer in den Raffinirofen
gehen. In Pittsburg werden die reichen Schlacken, welche vor dem völligen
Flüssigwerden des Kupfers entstehen, im Cupolofen verschmolzen.
Die besten Sorten Obernsee-Kupfer hatten z.B. folgende Zusammensetzung:
Kupfer
99,92
99,900
99,890
99,870
99,830
99,82
99,810
99,80
Eisen
–
–
0,005
–
–
–
0,008
–
Nickel
–
0,002
0,003
0,003
0,030
–
–
0,02
Kobalt
–
–
–
–
Spur
0,09
Spur
–
Blei
–
–
–
–
–
–
–
–
Silber
0,03
0,030
0,030
0,020
0,030
0,06
0,030
0,04
Sauerstoff
0,28
0,280
0,190
0,270
0,220
0,28
0,300
0,28
––––––––––––––––––––––––––––––––––––––––––––––––––––––––––––––––––––––––
100,23
100,212
100,118
100,163
100,083
100,25
100,148
100,14
Andere Proben enthielten 99,53 bis 99,78 Proc. Kupfer,
0,005 bis 0,044 Proc. Blei, 0,02 bis 0,12 Proc. Silber, 0,01 bis 0,04 Proc. Eisen,
0,002 bis 0,08 Proc. Kobalt und Nickel, 0,002 bis 0,07 Proc. Zink.
Gut raffinirtes Kupfer aus Arizona ist ebenso rein als das vom Obernsee, wie folgende
Annalysen zeigen:
Kupfer
99,990
99,990
Eisen
0,021
0,014
Zink
Spur
Spur
Silber
0,008
0,008
–––––––––––––––––
100,019
100,012.
Weniger gut ist das aus Colorado Erzen erhaltene Kupfer, welches Tellur enthält und
nur zur Herstellung von Messing tauglich erscheint. Bemerkenswert]! ist, daſs fast
alles amerikanische Kupfer, sowohl das vom Obernsee, wie auch das aus Schwefelerzen
des Ostens dargestellte, kein Arsen, Antimon und Wismuth enthält. Das Kupfer aus den
unreinen Schwefelerzen des Westens (I) und das aus den Ore-Knob-Erzen (II) hat
folgende Zusammensetzung:
I
II
Kupfer
99,650
99,80
Sauerstoff
0
0,39
Kohlenstoff
0
0
Schwefel
0
0
Arsen
0,088
0
Antimon
0,035
0
Blei
0,044
0,01
Silber
0,066
0,05
–––––––––––––––
99,883
100,25.
F. Gutzkow's Verfahren der
Goldscheidung in Californien bespricht T.
Egleston.1)
Danach werden in der Münze von St. Francisco verarbeitet: Goldbarren aus
Californien, welche man so stellt, daſs sie 2 Th. Gold auf 3 Th. Silber enthalten,
und dann granulirt, ferner Silber in Ziegelform von Comstock mit 2 bis 10 Proc.
Gold, welches ohne Granulirung direkt aufgelöst wird, und schlieſslich Silber in
Ziegelform mit beträchtlichem Kupfergehalt von der Amalgamation der Abgänge und aus
Gruben Nevadas, welches mit so viel Feinsilber zusammengeschmolzen wird, daſs der
Kupfergehalt auf 12 bis 8 Proc. herabgeht.
Zur Auflösung der Legirungen dienen 66cm weite und
45cm tiefe Kessel R (Fig. 12 und
13 Taf. 24) aus Guſseisen, welches durch einen Gehalt von 2 bis 4 Proc.
Phosphor gegen Säure widerstandsfähiger wird. Sie fassen 100 bis 150k Beschickung, welche durch eine mit Deckel
verschlieſsbare Oeffnung e des Hutes P eingetragen wird. Die beim Auflösen entwickelten Gase
und Dämpfe gelangen durch ein Bleirohr s in eine mit
Bleiplatten ausgekleidete Kammer N von 4m,6 Breite, 4m,6
Höhe und 11m,6 Länge, von hier durch einen Thurm
in einen hohen Schornstein. Die 66°-Schwefelsäure gelangt aus dem in dem mit Blei
ausgekleideten Behälter B umgestülpten Ballon A, dessen Mündung etwa 15cm tief in die Säure eintaucht, durch ein Bleirohr a in den Behälter K. Hier befindet sich ein
hölzerner, mit Blei überzogener Kolben J mit 3 bis 4cm Spielraum an jeder Seite, welcher durch
Gegengewicht I ausbalancirt ist und durch ein vom
Gerüst E getragenes Hebelwerk HG auf und nieder bewegt werden kann. Beim Niederdrücken des Kolbens wird
ein demselben gleiches Volumen Säure durch Rohr Q in
den Kessel R gedrückt, und zwar beim vollständigen
Eintauchen 10k. Beim Aufziehen des Kolbens füllt
sich der Behälter K wieder mit Säure. Nachdem die Säure
zum Sieden gebracht ist, entfernt man den Deckel P und
bringt 30 bis 40k Granalien oder eine etwas
reichere Beschickung von Silberziegeln in den Kessel, setzt den Deckel wieder auf,
gibt nach 11 bis 15
Minuten die weitere erforderliche Säure zu, so daſs sie 23 bis 25cm hoch im Kessel steht und heizt unter
zeitweiligem Umrühren 3 bis 4 Stunden lang.
Die heiſse Lösung wird dann in einen eisernen, 2m,75 langen, 1m,5 breiten und 0m,5 tiefen Behälter U
durch ein eisernes Rohr T in darin befindliche 110°
heiſse Schwefelsäure von 58° B. abgehebert, von welcher 1cbm für je 200k
behandelte Legirung erforderlich ist und welche als Mutterlauge von der
Krystallisation des Silbersulfates erhalten wird. Zum Zweck des Abheberns mittels
Vacuum ist das für eine Reihe von 5 Kesseln gemeinschaftliche Gefäſs U mit einem schweren Eisenhut V bedeckt, welcher mittels Flaschenzug gehoben werden kann und am Rande
durch ein breites Kautschukband abgedichtet ist. Die luftdicht eingelassene Röhre
W steht mit einem Dampfrohre X zur Erzeugung des Vacuums in Verbindung; der hierzu
verwendete Dampf gelangt durch Rohr Z in den Behälter
j mit Eisenvitriollösung, um diese vorzuwärmen. Vor
dem Abhebern der Flüssigkeit wird das Gold auf eine Seite des Kesselbodens geschoben
und das Heberrohr bis nahe auf diesen herabgesenkt. Die den Behälter U bis etwa 6cm unter
dem Rande füllende Flüssigkeit läſst man bei aufgesetztem Deckel sich klären.
Dieselbe enthält Sulfate von Silber, Eisen und Kupfer, Graphit und suspendirtes
Gold, welches sich nebst Bleisulfat absetzt.
Die geklärte Flüssigkeit wird in das eiserne Gefäſs D,
welches von einem bleiernen Mantel umgeben ist, übergehebert und durch in den
Mantelraum geleitetes Wasser auf 30 bis 40° abgekühlt, wobei Silbervitriol
auskrystallisirt, und die saure Mutterlauge, welche allen Kupfervitriol enthält,
durch ein Dampfvacuum in den Behälter U geschafft. Um
die Krystalle möglichst von Säure zu befreien und trocken zu machen, befindet sich
am Boden von D ein Gefäſs c, in das die Mutterlauge gelangt und welches gestattet, den Heber d am tiefsten Punkte anzubringen. Für die Reduction des
Silbersulfates ist es erwünscht, die Krystalle möglichst säurefrei zu machen. Die
Krystalle werden mit einer eisernen Schaufel aus D in
den mit Blei ausgekleideten, auf Rädern h beweglichen
Holzbehälter F geschafft, welcher für 5 Lösekessel
gemeinschaftlich ist. Zwischen Los- und Hauptboden f
befindet sich ein Halm. Auf die Krystalle wird eine heiſse gesättigte neutrale
Eisenvitriollösung aus j durch Rohr i geleitet, welche zuerst Kupfersulfat löst, dann das
Silbersulfat reducirt, die freie Säure aufnimmt und anfangs als blaue, dann als
braune Flüssigkeit durch das Hahnrohr g in einen
Behälter o von 5m,6
Länge, 2m,8 Breite und 0m,9 Tiefe abflieſst, bis eine grüne Farbe das Ende
der Reduction anzeigt, Die blaue Kupfer haltige Flüssigkeit wird von der braunen
getrennt aufgefangen; in letzterer befinden sich noch etwa 2,5 Proc. Silber gelöst.
Die Reduction ist in 3 bis 4 Stunden beendigt. Die Eisenoxydlösung wird durch
Behandeln mit Eisenabfällen im Behälter o in Oxydulsalz
verwandelt und die Flüssigkeit mittels Dampfpumpe p durch
die Röhren r und q in den
Kasten k geschafft, aus welchem sie durch l nach j abflieſst.
Der Plattner'sche Goldextractionsprozeſs ist in Nevada County, Californien, seit 11 Jahren
eingeführt und wird augenblicklich von 11 Hütten angewendet. Auf dem Idaho-Werke
flieſst das gepochte und angereicherte Erz mit möglichst wenig Wasser über in
Platten eingelassene, mit Quecksilber gefüllte Vertiefungen (riffles), gelangt dann in Kübel, in welchen sich amalgamirte gewellte
Kupferplatten bewegen, flieſst nun über lange amalgamirte Platten und mit Gummistoff
ausgekleidete Tröge, um schlieſslich noch in Pfannen amalgamirt zu werden, ehe es an
die Chlorationswerke abgegeben wird. Auf den Werken der Providence-Mine gehen die
gepochten Erze durch eine Mulde, deren Bodenplatte amalgamirt ist, dann durch
amalgamirte Tröge in Frue'sche Goldwäschen.
Das Rösten der Kiese geschieht in zweiherdigen, kreisrunden Oefen, deren oberer Herd
einen offenen Trockenboden bildet. Der Beschickung im unteren Ofen wird 3 Proc. Salz
zugesetzt. Das Erz aus den Goldwäschen mit 75 Proc. Kiesen und 25 Proc. Quarz eignet
sich gut für direktes Rösten; andere werden zunächst mit 15 bis 25 Proc. Sand
gemischt.
Zur Chloration werden etwa 2t,5 befeuchtetes Erz
0m,7 hoch auf die falschen Böden von 1m,8 hohen, mit Asphaltfirniſs ausgestrichenen
Kästen geschüttet, worauf man das in gewöhnlicher Weise erzeugte Chlorgas unter die
falschen Boden leitet. Hat das Chlor nach 5 bis 6 Stunden die Schicht durchdrungen,
so wird der Deckel mit Teig gedichtet und die Masse 2 Tage lang der Einwirkung des
Chlores überlassen. Das ausgelaugte Chlorgold wird in gewöhnlicher Weise mit
Eisenvitriol gefallt. Die Rückstände werden dann zur Gewinnung des Silbers in tiefer
stehenden Bottichen mit einer kalten Lösung von unterschwefligsaurem Calcium
ausgezogen; das gelöste Silber wird als Schwefelmetall gefällt, um die Lösung
abermals zu verwenden.
Nach W. U. Greene (Journal of
the Franklin Institute, 1882 Bd. 113 * S. 377) soll das aus Braunstein,
Chlornatrium und Schwefelsäure oder sogar aus Chlorkalk und Schwefelsäure
entwickelte Chlor in einem Gasometer aufgefangen, dann
mittels Druckpumpe durch Rohr a (Fig. 14
Taf. 24) in mit den gerösteten Erzen beschickte, 1m,07 weite und 1m,37 lange eiserne
Cylinder E eingepreſst werden, welcher langsam gedreht
wird. Das gelöste Chlorgold soll schlieſslich nach dem
Vorschlag von W. M. Davis mittels Kohle gefällt
werden.
Diese Wirkung von Holzkohle auf Goldchloridlösung ist
nach Versuchen von G. A. König (Daselbst S. 382)
vorwiegend den bekannten physikalischen Eigenschaften der Holzkohle zuzuschreiben;
daneben findet aber aucli eine Zersetzung nach folgender Gleichung statt: 4AuCl3 + 6H2O + 3C = 4Au
+ 12HCl + 3CO2.
Tafeln
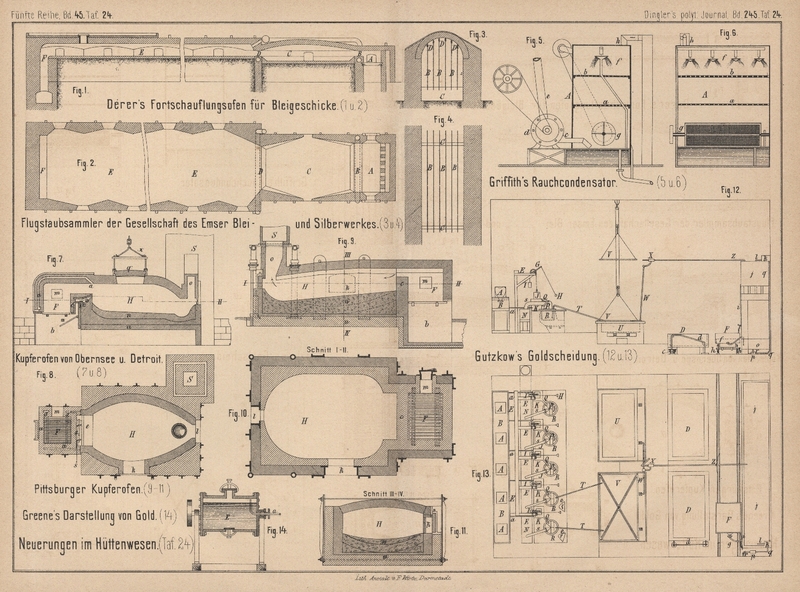