Titel: | Ueber Neuerungen im Eisenhüttenwesen. |
Fundstelle: | Band 255, Jahrgang 1885, S. 29 |
Download: | XML |
Ueber Neuerungen im Eisenhüttenwesen.
(Patentklasse 18. Fortsetzung des Berichtes Bd.
253 S. 117.)
Mit Abbildungen auf Tafel
3.
Ueber Neuerungen im Eisenhüttenwesen.
Zur Verbindung des direkten Verfahrens zur Herstellung
schmiedbaren Eisens mit dem Herdprocesse hat Wilson, wie W. P. Ward im American Institute of Mining Engineers in der
Februarversammlung 1884 zu Cincinnati mittheilte, folgende dem Scientific American Supplement, 1884 S. 7043
veröffentlichte Ofeneinrichtung in Anwendung gebracht.
Ueber dem Fuchse eines zweiherdigen Puddelofens A (Fig. 1 und 2 Taf. 3)
erhebt sich, getragen von 4 Säulen, ein schmiedeiserner Cylinder N, in welchem ein mittlerer Hauptgasabzugskanal B, 8 derartige Nebenkanäle E und zwischen je zwei der letzteren je ein (also im Ganzen 8) Retorten
C in feuerfestem Mauerwerke ausgeführt sind. Ueber
diesen Retorten ist auf dem Cylinder ein ringförmiger Begichtungstrichter D angeordnet, durch welchen dieselben mit pulverisirtem
Erze gemischt mit 20 Proc. Holzkohle oder Kokes beschickt werden. In dem
Hauptgaskanale B sind oben Verbindungskanäle mit den
Seitenkanälen C angebracht und münden letztere am Boden
des Cylinders N in einen ringförmigen Sammelkanal F, welcher zu den Dampfkesseln oder anderen
Hüttenapparaten führt. In den schräg ansteigenden Böden der Retorten münden
guſseiserne Rohre P, welche mittels Schieber die
Einführung des reducirten Erzes in den Vorherd des Puddelofens gestatten.
Beim Betriebe des Ofens werden die Retorten, welche so viel Erz fassen, daſs der
Puddelofen 24 Stunden in Betrieb bleiben kann, mit Erz und Kohle gefüllt und der
Puddelofen angefeuert. Die Verbrennungsproducte des letzteren streichen dann durch
den Hauptkanal B hinauf, die Nebenkanäle E hinab und gelangen durch den ringförmigen Kanal F zu den Dampfkesseln. Auf diesem Wege umspülen diese
Gase die Retorten auf 3 Seiten und bewirken im Vereine mit der Kohle eine Reduction
des Erzes. Dieses wird dann in den Vorherd hinabgelassen und unter der Schlacke des vorigen
Einsatzes vollständig reducirt. Sodann wird es in den der Feuerbrücke zunächst
liegenden Herd gebracht und hier zu Luppen verarbeitet. Da der Fassungsraum der
Retorten und der der beiden Herde in Einklang stehen., so ist ein ununterbrochener
Betrieb des Ofens möglich.
O. Thiéblemont in Liverdun (* D. R. P. Nr. 28223 vom 18.
November 1883) wendet als Reductions- und
Kohlungsmittel keinen festen Kohlenstoff, sondern Wasserstoff und Kohlenwasserstoff bei mehr oder minder hoher Temperatur
an. Der zur Ausführung des an sich bekannten Verfahrens dienende Apparat umfaſst
einen Röstofen zur Verdampfung des im Erze enthaltenen Wassers und zur
Verflüchtigung schädlicher Beimengungen, ferner einen Reductionsofen, einen
Schweifsofen zur Vereinigung des Metallschwammes und einen Schmelzofen zur Gewinnung
eines mehr oder minder Kohlenstoff haltigen Eisens. Fig. 3 und 4 Taf. 3 zeigen den
Apparat, welcher nach der etwas unklar gehaltenen Patentschrift folgende Einrichtung
hat: Ist in den beiden Röstöfen a das Erz, welches in
möglichst gleich groſsen Stücken eingebracht werden muſs, genügend vorbereitet, so
wird es von den Bühnen k aus mittels Stangen durch die
Schürlöcher l in den Reductionsofen b geschoben. Hier wird durch das glühende Erz in den
Regeneratorkammern g hoch erhitztes Gas geleitet und
dasselbe dadurch reducirt. Nachdem es sich hierauf in dem Schachte d genügend abgekühlt hat, gelangt es durch die
Oeffnungen o in den Flammofen n (Fig.
5), in welchem es vollends zu Eisen umgewandelt wird. Zu dem Apparate
gehören 2 Generatoren. Von denselben erzeugt immer einer an Kohlenstoff reiche Gase
durch Entgasung der Kohle, der andere an Kohlenstoff
arme Gase durch Vergasung derselben und zwar wechseln
diese Generatoren ihre Rollen, wenn die beiden Vorgänge in denselben beendet sind;
d.h., ist die Entgasung in dem einen Ofen fertig, so beginnt in demselben die
Vergasung: inzwischen wird der andere Ofen neu beschickt und in diesem die Kohle
entgast. Beide Gasmengen werden dem Apparate in nicht näher angegebenen
Verhältnissen zugeführt.
Haben die in den Regeneratoren hoch erhitzten Gase den Reductionsschacht b durchzogen, so gelangen dieselben theils in die
Röstöfen, wo die Gase zum Rösten des Stückerzes dienen, theils durch Kanäle e in die andere Gruppe von Regeneratoren zu deren
Beheizung. Letztere werden zur Erhitzung der Gase benutzt, wenn die erste Gruppe
hinreichend abgekühlt ist. Zur Einführung der Gase in die Regeneratoren dienen die
Ventile h und i, zur
Abführung der Gase in die Oefen die Schieber m. Im
Anfange des Betriebes bleibt natürlich der im Abkühlungsraume d befindliche Erzposten unreducirt. Die Ueberführung
des Erzes aus den Röstöfen in den Reductionsofen und von diesem in den Flammofen
kann auch auf maschinellem Wege erfolgen. Der Erfinder schlägt z.B. für letztere
Ueberführung eine Presse vor, welche das aus dem Reductionsofen kommende schwammige Metall in
einer unter Druck stehenden Gasatmosphäre stetig verdichtet und dann dem Flammofen
zuführt. In letzterem befindet sich eine Silicatschlacke: zur Erhaltung der zur
Zusammenschweiſsung der Eisentheilchen nöthigen Temperatur wird durch die Oeffnungen
p dem Ofenherde Gas und Luft zugeführt. Zur
Erleichterung der Schweiſsung ist in dem Herde eine von oben in das Schlackenbad
herabhängende gekühlte Scheidewand r angeordnet, welche
das Bad in 2 Theile scheidet. Ueber dem linken Theile, welcher durch die Kanäle b mit dem Reductionsschachte d in Verbindung steht, wird ein reducirendes Gas eingeführt, um jede
Möglichkeit einer Oxydation des Metallschwammes beim Eintritte in den Herd zu
vermeiden. Von der linken Seite wird das Metall unter der Scheidewand r auf die rechte Seite gebracht, um hier seine
Schweiſsung zu beenden. Thiéblemont glaubt, in diesem
Ofen ganz reines flüssiges, von Kohlenstoff fast freies Eisen herstellen zu können.
Zur Umwandlung desselben in Stahl wird, nachdem man die Schlacken entfernt hat,
Roheisen mit dem nöthigen Kohlenstoffgehalte zugesetzt.
Auch Will. Arthur in Cowes, Insel Wight, England (D. R.
P. Nr. 28220 vom 9. Oktober 1883) schlägt gasförmiges
Brennmaterial zur Reduction und Kohlung des
Erzes vor. Hiernach werden die Erze in natürlichem Zustande oder, im Falle dieselben
stark verunreinigt sind, geröstet in Muffeln gebracht und hierin bis zur
Kirschrothglühhitze erhitzt. Sodann wird in bemessenen Mengen unter Druck
Wasserstoff oder Wasserstoff und Kohlenoxyd, oder Wasserstoff, Stickstoff und
Kohlenoxyd in die Muffeln eingeführt, so daſs das Erz allen Sauerstoff an den
Wasserstoff abgeben kann und auch die Verunreinigungen (wie Schwefel, Phosphor und
Silicium) in flüchtige Verbindungen übergeführt werden. Nach beendeter Reduction
wird die Wasserstoffzuführung abgestellt und werden bestimmte Mengen von gasförmigen
Kohlenwasserstoffen behufs Kohlung des Eisenschwammes in die Retorten geleitet. Zu
diesem Zwecke sind die Muffeln mit Zuleitungs- und Ableitungsröhren versehen. Als
Verdünnungsmittel für die Kohlenwasserstoffe wendet man weniger carburirten
getrockneten Wasserdampf als Wasserstoff, Kohlenoxyd und Stickstoff an: letzterer
besonders soll eine Kohlenstoffaufnahme des Eisenschwammes aus den
Kohlenwasserstoffen befördern. Der Eisenschwamm wird in einer Stickstoff-Atmosphäre
erkalten gelassen, oder in einen offenen Herd gebracht.
Gewöhnlich werden die Regenerativ-Winderhitzungsapparate
möglichst breit angeordnet, um groſse Berührungsflächen zwischen Gebläsewind und
Mauerwerk zu erhalten. Nach dem Engineering and Mining
Journal, 1884 Bd. 37 S. 459 zieht Weimer in
Lebanon, Penn., die Apparate mehr in die Länge, so daſs die einzelnen Kammern über einander zu stehen kommen. Abgesehen davon, daſs
hierdurch Raumersparniſs erzielt wird, ist bei derartigen Apparaten eine
Bewegungsumkehr des Windes nicht nothwendig. Die allgemeine Einrichtung unterscheidet sich
hiernach nur unwesentlich von der bekannten. Das Füllmauerwerk wird aus nur 2
Steinmodellen aufgebaut und trägt sich dabei das Mauerwerk selbst, so daſs für die 3
Füllungen keine besonderen Tragebögen nöthig sind. Wie aus Fig. 9 Taf. 8 zu entnehmen
ist, wird das Gas der untersten Kammer durch das Rohr a
zugeführt. In dem Verbrennungsraume b mischt es sich
mit ⅓ der zu seiner vollkommenen Verbrennung nöthigen kalten Luftmenge und
durchziehen dann die Verbrennungsgase mit den noch unverbrannten Gasen die unterste
Kammer. In dem Räume c tritt das zweite Drittel der
Verbrennungsluft, durch den Kanal d vorgewärmt, mit den
Gasen zusammen. Das Gemisch steigt dann weiter bis zur Kammer e, mischt sich mit dem letzten Drittel der vorgewärmten
Verbrennungsluft, streicht durch das oberste Füllmauerwerk und verläſst dann den
Apparat durch die Esse. Hat derselbe die nöthige Hitze, so werden die Gaszuleitungen
und Ablässe geschlossen und der Gebläsewind durch das Rohr f in den oberen Theil des Apparates eingeführt, um denselben der Länge
nach zu durchziehen und durch das Rohr g zu entweichen.
An dem Apparate sind die bekannten Reinigungsöffnungen angeordnet.
Um das Regenerativ-Winderhitzungs-Prinzip auch bei kleineren Oefen, z.B. Puddelöfen, anwenden zu können,
bringt J. T. King in Liverpool (Englisches Patent, 1883
Nr. 4779) drehbare Regenerativ-Kammern in Vorschlag,
welche, wie in Fig.
10 Taf. 3 angedeutet ist, zu zwei oder mehr Kammern in einer auf Rollen
ruhenden cylindrischen Trommel angeordnet und mit Füllmauerwerk ausgesetzt sind. Die
Stellung der einzelnen Kammern hinter dem Ofen ist nun eine solche, daſs immer eine
Kammer hinter dem Fuchse steht, also die Verbrennungsgase durch sich hindurch gehen
läſst, während sich die andere Kammer vor dem Luftzuführkanale befindet. Ist die
eine Kammer heiſs genug und die andere entsprechend abgekühlt, so dreht man den
Cylinder um, so daſs die kalte Kammer hinter den Fuchs, die heiſse vor den Luftkanal
zu stehen kommt. Die heiſse Luft führt zu Oeffnungen in der Feuerbrücke oder unter
den Rost.
Als Futter für Bessemerbirnen schlägt H. D. Pochin in Barnes (Englisches Patent, 1883 Nr.
5568) Chromerz vor. Dasselbe soll entweder in Stückform
mit einem Bindemittel von Steinkohlentheer, vermischt mit Dolomit, aufgemauert oder
eine steife Mischung dieser Bestandtheile in gepulvertem Zustande in die Birne
eingestampft werden. Das Chromerz, hauptsächlich aus Eisenoxyd und Chromoxyd
bestehend, soll als basisches Futter dienen.
Zur möglichst vollständigen Gewinnung des Phosphors aus
Phosphor haltigen Erzen benutzt C. Stöckmann
in Ruhrort (* D. R. P. Nr. 27105 vom 14. Juli 1883) ein Verfahren, welches sich an
das Patent Nr. 13660 des Hörder Hüttenvereins anlehnt,
indem das aus den Eren gewonnene, an Silicium arme Roheisen mit 1 bis 3 Proc. Mangan in einer
mit Kalk und Magnesia ausgefütterten Birne bis zum Verschwinden des Kohlenstoffes
verblasen wird. Der hierzu nöthige Wind ist jedoch nicht kalt, sondern so heiſs wie
möglich, um trotz des Fehlens des Siliciums heiſse Posten zu erhalten. Da wenig oder
gar kein Silicium im Eisen vorhanden ist, so bedarf man auch keines Kalkes zur
Bindung desselben. Die Phosphorsäure geht deshalb – und dies ist der eigentliche
Zweck des Verfahrens – mit dem gebildeten Manganoxyde eine Verbindung ein, aus
welcher sich die Phosphorsäure für Zwecke der Landwirtschaft besser ausscheiden
läſst als aus den phosphorsauren Kalk haltenden Schlacken. Ist beim Blasen aller
Phosphor oxydirt, was am Verschwinden der Kohlenstofflinien zu erkennen ist, so
zieht man die Schlacke ab und setzt dem Eisenbade in bekannter Weise Spiegeleisen
oder Ferromangan zu. Ist die Schlacke zu steif, so läſst sich dieselbe durch Zusatz
einiger Quarzstücke flüssiger machen.
Bei der Lagerung der Walzenzapfen für Triowalzwerke
besteht eine Schwierigkeit darin, die Zapfen der Mittelwalze so anzubringen, daſs:
1) der Deckel A (Fig. 11 und 12 Taf. 3) in
lothrechter Richtung leicht verstellbar ist, um den erforderlichen Schluſs des
Lagers stets zu erzielen; 2) der beim Walzen zwischen den Walzen b und c entstehende
Verticaldruck auf die Druckschraube S übertragen wird,
ohne daſs ein bremsender Druck auf den Zapfen a
hervorgebracht wird; 3) bei dem Niederschrauben der Druckschraube S nur die äuſseren Theile der Lagerung auf einander
gepreſst werden, ohne daſs dadurch ein bremsender Druck auf einen der Zapfen erzeugt
werden kann: endlich 4) bei der erforderlichen inneren Weite der geschlossenen
Ständer und der dadurch bei den bisherigen Constructionen entstehenden groſsen
Entfernung der Stützpunkte des Deckels A dessen
Querschnitt in der Mitte genügend stark bleibt, um dem Walzendrucke zu widerstehen,
während andererseits zwischen A und dem Deckel B des Lagers der Oberwalze genügender Spielraum bleibt,
um auch Walzen einlegen zu können, deren Durchmesser bis zu 20 Proc. kleiner sind
als urspünglich.
Um diese Bedingungen zu erfüllen, erhöht R. M. Daelen in
Düsseldorf (* D. R. P. Nr. 28592 vom 4. März 1884) das Unterlager C der Mittelwalze an beiden Seiten und versieht es mit
Vorsprüngen, so daſs der Deckel A umfaſst und mittels
der Doppelkeile D gegen letztere abgestützt wird. Der
untere Keil liegt fest, der obere wird durch eine in dem Vorsprunge des Unterlagers
C befestigte Hakenschraube eingestellt, so daſs
hierdurch der Schluſs des Lagers für den Zapfen b genau
eingestellt werden kann.
Das Unterlager C ruht bei E
auf dem Ständer, wo entweder durch Beilagen von Flacheisen oder durch Keile (wie D) die Höhenlage der Walze richtig eingestellt
wird.
In gleicher Weise wird das Oberlager F auf dem
Unterlager C abgestützt und eingestellt. An dieser
Stelle werden indessen die Beilagstücke oder Doppelkeile durch Schrauben G, welche mit ihren Muttern in dem Oberlager F eingelassen sind und bei J Gegenmuttern tragen, ersetzt.
Die Lagerkörper werden in der Richtung der Achsen der Walzen durch Schrauben
befestigt, welche bis jetzt zu beiden Seiten in die Ständer eingelassen werden, so
daſs deren Querschnitt an den Stellen der Durchbohrungen geschwächt wird. Eine
Verbesserung besteht darin, diese Schrauben in den Lagerkörpern anzubringen und mit
hakenförmigen Köpfen zu versehen, die in Nuthen liegen, welche die ganze Länge der
Ständerseiten einnehmen, so daſs keine schädliche Schwächung erfolgt, wie bei K dargestellt ist. Der Angriff der Schrauben erfolgt
dann in jeder Höhenstellung der Lagerkörper in richtiger Weise.
Da aber auch eine Schwächung der Querschnitte der Lagerkörper nicht immer günstig
ist, sind anstatt der Hakenschrauben K Bügel L von Flacheisen angewendet, durch deren Oeffnung Hebel
M gesteckt werden; letztere werden durch die
Kopfschrauben N eingestellt, deren Gewinde in den
Hebeln M eingeschnitten ist und welche mit Gegenmuttern
versehen sind. Hierdurch wird der fernere Vortheil erzielt, daſs die Gewinde nur
halb so stark beansprucht werden als bei den oben angeführten Einrichtungen und daſs
die Schrauben für die Bedienung leichter zugänglich sind, weil dieselben weiter nach
auſsen liegen.
R. Meffert in Schneidhausen bei Düren (* D. R. P. Nr.
28593 vom 7. März 1884) hat die in Fig. 8 Taf. 3 skizzirte
Lagerung für die Mittelwalze eines Triowalzwerkes
angegeben: Das Lager besteht aus den demselben als Stützpunkt dienenden
Gegengewichtsstangen a, zwischen deren Gegenmuttern b sich die mit den Ansätzen c versehenen Lagerdeckel d und d1 befinden; zwischen
diesen sind die Führungsstücke e und e1 angebracht und an
letztere legen sich die vier Lagerstücke f an, so daſs
sich zwischen diesen die Mittelwalze drehen kann. Die Führungsstücke e und e1 sind so zwischen den Deckeln d und d1 befestigt, daſs sie zwischen den Führungsbahnen
des Ständers k auf- und niedergehen können. Das
Festerstellen der Lager wird durch die Gegenmuttern b
bewerkstelligt; es müssen jedoch in diesem Falle die Unterlegescheiben g entfernt und durch entsprechend dünnere ersetzt
werden. Der obere Lagerdeckel d ist nach einer Seite
hin verlängert und mit einem Einschnitte versehen, damit die Stange i, auf welcher der Tisch ruht, mit der Mittelwalze auf-
und niedergehen kann.
Zum Heben des Walzenlisches bringt Meffert (* D. R. P. Nr. 28225 vom 31. Januar 1884)
folgende Einrichtung in Vorschlag: In dem Lagerstuhle a
(Fig. 6
und 7 Taf. 3)
ruht die dreifach gekröpfte Welle b mit daran
befestigtem Kuppelmuffe b1 und Sperrscheibe b2. Die mit den Kurbelhälsen c bis c2 versehene Welle b steht einerseits durch die Stangen d und d1 mit dem Walzentische t, andererseits durch die Stange e und den im
Lagerstuhle e1 sich
drehenden Hebel f mit dem Gewichte g in Verbindung. Die auf der Grundplatte h befestigte und mit der Nase i versehene Feder k legt sich mit letzterer
fest auf die Sperrscheibe b2, so daſs sie bei deren Umdrehung, sobald der Einschnitt l bei i angelangt ist, in
denselben eingreift. In dem Bocke m auf der Bühne p ist der Tritt s
angebracht, welcher im Bocke m seinen Drehpunkt hat,
bei i rechtwinklig ausläuft, hier unter die Feder k faſst und dieselbe auf und nieder bewegt.
Die Handhabung des Hebeapparates ist folgende: Sobald das Packet zwischen Unter- und
Mittelwalze hindurchgegangen und auf dem Walzentische t
angelangt ist, wird der Kuppelmuff n gegen den Muff b1 gerückt und dadurch
die Welle b in Bewegung gesetzt; durch die sich nach
oben drehenden Kurbeln c, c1 und die Stangen d, d1 wird der Walzentisch t, welcher seinen Drehpunkt bei o hat, in die
Stellung t1 gebracht;
andererseits bewegt sich die Kurbel c2 mit der Stange e und
dem Hebel f abwärts. Der Hebel f geht nun mit seinem entgegengesetzten zweitheilig und gabelförmig
auslaufenden Ende mit dem Gewichte g aufwärts, das
Gegengewicht r wird hierdurch erleichtert und die
Mittelwalze, welche durch die Stangen v und die Hebel
q mit dem Gegengewichte r in Verbindung steht, legt sich in Folge dieser Entlastung an die
Unterwalze.
Während dieser Zeit ist der Einschnitt l der
Sperrscheibe b2 bei i angelangt. Die Nase i
der Feder k greift nun in den Einschnitt l und bleibt so lange in dieser Stellung, bis das
Packet seinen Rückwärtsgang (zwischen Ober- und Mittelwalze hindurch) nahezu
vollendet hat. In diesem Augenblicke wird durch Niedertreten des Trittes s die Feder k aus dem
Einschnitte l entfernt, der Walzentisch geht in seine
vorige Stellung zurück, das Gewicht g legt sich auf das
Gegengewicht r, so daſs durch diese Mehrbelastung die
Mittelwalze gegen die Oberwalze gedrückt wird und derselbe Vorgang nun wieder von
Neuem beginnen kann.
Tafeln
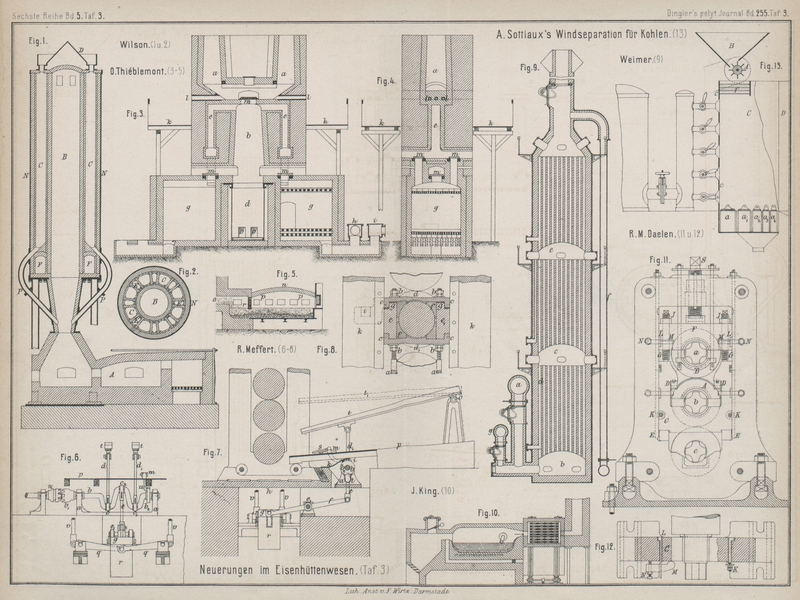