Titel: | Ueber Neuerungen in der Giesserei. |
Fundstelle: | Band 253, Jahrgang 1884, S. 363 |
Download: | XML |
Ueber Neuerungen in der Gieſserei.
Mit Abbildungen auf Tafel 26.
(Patentklasse 31. Fortsetzung des Berichtes Bd.
250 S. 149 u. Bd. 252 S. 454.)
Ueber Neuerungen in der Gieſserei.
Um die Leistungsfähigkeit einer Gieſserei zu erhöhen, schlägt Gust. Hertzog in Paris (* D. R. P. Nr. 26417 vom 21. Januar 1883) die in
Fig. 1 und 2 Taf. 26
skizzirte Anordnung des Gieſshauses vor. Auf einer
Langseite des Gieſshauses steht die Formmaschine B,
deren Preſskolben durch Wasserdruck bewegt wird. Ueber dem Preſskolben befinden sich
2 Schienengeleise A, A1, welche in einer gewissen Entfernung über einander an allen Wänden des
Gieſshauses entlang laufen und die zur Beförderung der Ober- und Unterkasten
bestimmten Wagen S tragen. Unter den Geleisen A, A1 liegt auf der
gegenüber liegenden Langseite des Gieſshauses ein Geleise H, auf welchem die Formkasten auf einander gestellt und vollgegossen
werden. Die Schienengeleise A, A1 haben eine so groſse Spurweite, daſs die Formkasten durch sie
hindurch auf im Geleise H stehende Wagen gesenkt werden
können. Ueber dem Geleise H ist ein Laufkrahn F angeordnet, welcher das Aufeinandersetzen der
Formkasten und das Herunterlassen derselben auf das Geleise H vermittelt. Unter letzterem liegt in der linken Ecke des Raumes der
Schacht G, welcher den in denselben gestürzten
gebrauchten Formsand aufnimmt. Von hier aus befördert die Schnecke G1 den Sand zur
Kollermühle K, in welcher derselbe gemahlen wird, um
dann von Neuem angefeuchtet und gesiebt in die Aufbewahrungskasten L gebracht zu werden. Letzteren gegenüber auf der
anderen Schmalseite des Gieſshauses liegt der Trockenofen E, durch welchen die Formkasten auf ihren Wagen einzeln hindurchgefahren
und 15 bis 20 Minuten lang einem erhitzten Luftstrome ausgesetzt werden.
Der Betrieb einer derartig eingerichteten Gieſserei ist folgender: Die Formkasten
werden auf den Geleisen A, A1 auf ihren Wagen in der Pfeilrichtung nach einander unter die
Presse B geführt, hier über der Modellplatte mit dem
Preſsrahmen versehen, mit Sand gefüllt, gepreſst, abgestrichen und dann in
fortlaufender Reihe in den Trockenofen E gefahren. Von
hier gelangen dieselben über das Geleise H, wo mittels
des Krahnens F der Oberkasten auf den Unterkasten
gesetzt und dann beide
mit einander verbunden auf Wagen, welche auf dem Geleise H stehen, gesetzt werden. Diese werden nun weiter gefahren zum Orte, wo
das Eingieſsen in die Formen erfolgt. Das Auseinandernehmen der Kasten findet über
dem Schachte G statt, so daſs der beim Herausnehmen der
Guſsstücke abfallende Sand sofort durch G zu der
Kollermühle K gelangt.
Die Wagen S, auf welchen die runden Formkasten ruhen,
bestehen aus je zwei mit losen Rädern versehenen Achsen, von denen die eine an zwei
festen Trägern befestigt ist, welche an den vorderen Enden unten eingekerbt sind, um
sich mit diesen Ausschnitten über die anderen Achsen zu legen. Die Formkasten,
welche in Fig. 2
punktirt in den Wagen S eingezeichnet sind, ruhen
mittels zweier Drehzapfen auf den Achsen und können nach Belieben um erstere gekippt
werden.
G. Hertzog hat auch eine Maschine zur Herstellung von Sandkernen (* D. R. P. Nr. 27396 vom
20. November 1883) angegeben, deren Einrichtung aus Fig. 3 und
4 Taf. 26 zu ersehen ist. Auf einem Gestelle A dreht sich um einen Zapfen C ein Tisch B, welcher an seinem Umfange in genau gleichen
Abständen vom Zapfen C die Formhülsen v zur Herstellung der Kerne trägt. Die Formhülsen, z.B.
26 Stück, haben verschiedene Durchmesser, welche den in der Gieſserei am meisten
gebrauchten Kernen entsprechen. An ihren oberen Enden tragen die Hülsen eine Platte
b2, welche an einer
Stelle eine mit Rand versehene Erweiterung zur Aufnahme des Sandes besitzt. Auf der
Platte b2 steht ein
Kasten b1, welcher über
das obere Ende der Hülsen gesetzt wird, um den Stampfsand aufzunehmen. Genau unter
dem die Mittellinien der Hülsen durchschneidenden Kreise befindet sich eine
Schraubenspindel K, welche mittels der Schraubenmutter
E gehoben und gesenkt werden kann, indem letztere
mittels der Kegelgetriebe J1 bezieh. J2
von der Handkurbel P aus gedreht wird; letztere kann
man behufs langsamerer Drehung der Mutter E auch auf
das Vorgelege O stecken. Um die Handhabung der Kurbel
P zu erleichtern, kann sich das Lager W, in welchem die Kurbelwelle P1 liegt, um die Zwischenwelle J drehen, so daſs der Arbeiter der Welle P1 jede Neigung zur
Wagerechten geben kann. Auf der Schraubenspindel K ist
eine Stange L befestigt, auf welche oben ein der
lichten Weite der betreffenden Hülse entsprechender Kolben M gesteckt wird.
Die Handhabung der Maschine ist hiernach leicht verständlich: Die Formhülse v, welche dem zu formenden Kern entspricht, wird über
den Kolben M gedreht und dann die Scheibe B mittels des Vorsteckers N auf A befestigt. Sodann hebt man M durch Drehen von P so
hoch in die betreffende Hülse hinein, als es der Länge des zu formenden Kernes
entspricht und stampft die Hülse voll Sand. Hierauf wird die Kurbel P so lange gedreht, bis der Kolben M den Kern ganz aus der Hülse herausgeschoben hat und
dieser weggenommen werden kann.
Die Formhülsen können auch für die Herstellung abgesetzter Kerne eingerichtet werden.
Um Luftkanäle in die Kerne zu stoſsen, verlängert man den Zapfen C nach oben und befestigt an diese Verlängerung einen
Hebel, welcher eine in Führungen gleitende Nadel trägt. Behufs schnellerer Auf- und
Abbewegung der Spindel L kann an diese direkt eine
Zahnstange mit Trieb- und Handrad angebracht werden. Diesbezügliche Abänderungen
sind in der Patentschrift vorgeführt.
Zur Herstellung von Röhrenformen, deren Mäntel aus
verschiedenen auf einander gestellten Sandcylindern bestehen, benutzt Jos. Kudlicz in Sedlec, Böhmen (* D. R. P. Nr. 26772
vom 17. Juni 1883, vgl. 1881 242 * 405) eine Maschine,
welche, wie Fig. 7 Taf.
26 zeigt, im Wesentlichen aus dem cylindrischen Kasten M und dem mittels eines Zahnstangengetriebes in lothrechter Richtung
verschiebbarem Kerne K von einer dem äuſseren
Durchmesser des zu gieſsenden Rohres gleichen Stärke besteht. Um nun ein leichtes
Herausnehmen der gestampften Mäntel aus dem Formkasten M zu ermöglichen, legt man auf dem Boden desselben um den Kern K herum den Ring R (Fig.
8 und 9 Taf. 26).
Derselbe besitzt an seinem Umfange verschiedene Aussparungen o, um mit den Händen unter den leicht abnehmbaren Ring r fassen zu können, und an seinem inneren Umfange
bewegliche Knaggen t, welche durch Federn radial
einwärts geschoben werden. Diese Knaggen werden bei hochstehendem Kerne K von letzterem in den Ring R zurückgedrängt. In dieser Lage findet das Vollstampfen der Form statt.
Ist letzteres vollendet, so senkt man den Kern K, bis
die Knaggen t über seine obere Endfläche aus dem Ringe
R heraus treten. Nun hebt man den Kern K wieder, wodurch der Sandmantel, auf dem Ringe R bezieh. r stehend, bis
über den Formkasten gehoben wird und nun mittels des Ringes r bequem erfaſst und ohne Beschädigung zum Trockenraume gebracht werden
kann. Aehnliche Einrichtungen sind zur Herstellung der Muffenenden, der Eingüsse
u.s.w. getroffen.
Im Génie civil, 1883/4 Bd. 4 S. 141 wird eine von Fr. Sagnes construirte Formmaschine besprochen, welche
sich (in der Gieſserei von Bergès in Paris) bei Herstellung kleinerer Guſsgegenstände aus Bronze, z.B.
Schiffsbeschlagnägel, Nieten, Geschoſszünder, Quetschkugeln für die
Pulverfabrikation u. dgl. schon bewährt haben soll. Um Schiffsnägel herzustellen,
erhält die Maschine die in Fig. 6 Taf.
26 ersichtliche Einrichtung. Die Formplatte P, auf
welcher die Modelle der Nagelköpfe angebracht sind, ruht auf dem Gestelle O. Unter derselben liegt die mittels des Hebels L, des Triebes E und der
Zahnstange M lothrecht verstellbare Stange T, welche an ihrem oberen Ende den Tisch P1 trägt. Auf letzterem
sind die nach oben gerichteten Modelle für die Schäfte der Nägel befestigt, so daſs
dieselben durch Oeffnungen der Nagelkopfmodelle hindurch über die Platte P hervortreten können. In dieser Lage wird auf die
Platte P ein Formkasten mit Preſsrahmen gesetzt und
werden dann beide mit
Sand gefüllt. Der Preſskopf B wird behufs möglichster
Beschleunigung der Preſsarbeit durch ein Kurbelgetriebe (ähnlich wie bei
Stoſsmaschinen) bewegt. Die auf der Kurbelscheibe H
befestigte Pleuelstange b greift direkt an die in
Führungen gleitende Stange C des Preſskopfes B an. Die Bewegung der Kurbelscheibe H erfolgt mittels der Riemenscheibe F mit Schwungrad V und der
Zahnräder J, K. Das Schwungrad kann mittels der
Kuppelung D und der Hebel L1 und D1 vom Preſstische aus leicht mit der Welle A1 gekuppelt werden.
Das Sperrrad R mit Sperrklinke R1 verhindert einen Rückgang der
Kurbelscheibe H und damit die unbeabsichtigte Senkung
des Preſskopfes B.
Ein ähnliches Verfahren zum Formen von Guſsnägeln, bei welchem eine getrennte
Abformung der Köpfe und eine darauf folgende Herstellung der Nagelschäfte mittels
Durchstecken eines besonderen Modellstiftes durch die den Nagelköpfen entsprechenden
Modelle stattfindet, wurde von O. H. Stamm in Cassel (*
D. R. P. Nr. 24440 vom 14. Januar 1883 und Zusatz * Nr. 26431 vom 11. August 1883)
vorgeschlagen.
Gallas und Aufderheide in Kaiserslautern wurde zu ihrem
Patente * Nr. 19572 (vgl. 1883 250 * 8) ein Zusatzpatent
* Nr. 23343 vom 9. August 1881 ertheilt, welches Einrichtungen zur leichteren Handhabung der Formmaschine betrifft. Eine
derselben strebt die Fortlassung des das Gewicht des Preſstisches theilweise
ausgleichenden Gegengewichtes an. Es soll dies durch Anordnung eines
Differentialkettenzuges bewirkt werden. Auf den Wellen a (Fig. 5 Taf.
26) der in die Zahnstangen des Preſstisches eingreifenden Triebe D sind je zwei Kettenrollen, eine von kleinem, die
andere von doppelt so groſsem Radius aufgekeilt. Auf diesen Rollen sind nun Ketten
befestigt, welche in ihrer unteren Schleife Tragerollen K aufnehmen, deren Wellen mit dem Preſstische fest verbunden sind. Beim
Drehen der Wellen a wickeln sich also gröſsere
Kettenlängen ab, als sich aufwickeln oder umgekehrt und findet hierdurch die Hebung
und Senkung des Preſstisches statt. Nebenbei stehen aber die Triebe mit den
Zahnstangen noch in Eingriff. Ein besonderer Zweck dieser umständlicheren Anordnung
ist durchaus nicht einzusehen. Allerdings wird in der Patentschrift die ganz
unverständliche Behauptung aufgestellt, daſs durch diese Anordnung (der 4
Kettenzüge) der Preſstisch mit beliebiger Belastung annähernd durch die halbe Kraft
gehoben werden könne, als wenn die Kettenzüge nicht vorhanden wären. Dies ist aber
offenbar falsch; denn der auf die Windekurbel auszuübende Druck hängt
ausschlieſslich ab von dem Verhältnisse des Hebelarmes derselben zum Radius des
Triebes und die 4 Kettenzüge bringen im besten Falle nur passive
Bewegungshindernisse hervor. – Auſserdem ist noch eine zweite Ausführung angegeben,
nach welcher Preſstisch und Maschinengestell nur durch einen Differentialflaschenzug
mit einander verbunden sind und beide durch Handhabung des letzteren einander
genähert oder von einander entfernt werden können. Die zweite Neuerung betrifft eine
unwesentliche Abänderung
des Kastenrichtapparates, behufs Einstellung von Kasten
verschiedener Höhe, und eine Einrichtung der Formplatten, um Unter- und Oberkasten neben einander zugleich auf einer Formplatte formen zu können, indem bei ungleich
hohen Kasten die eine Hälfte der Formplatte so viel erhöht wird, daſs die Oberkanten
beider Kasten in gleicher Höhe liegen.
J. Allen Parks in New-York (* D. R. P. Nr. 25236 vom 29.
Mai 1883) wendet zur Herstellung von Eisenbahn-Scheibenrädern mit Hartguſskranz für letzteren eiserne
Hohlformen an, durch welche während des Gusses ein Strom kalten Wassers getrieben
wird. Zu diesem Zwecke besitzen die Formen in dem ringförmigen Hohlräume eine
Scheidewand, um Zufluſs und Abfluſs des Wassers von einander zu trennen. Bei sehr
groſsen Rädern können in dem Hohlräume auch mehrere Unterabtheilungen mit
entsprechenden Einlauf- und Auslaufstutzen behufs gleichmäſsigerer Abkühlung
angeordnet werden. (Vgl. Turk 1875 217 154. 218 * 491.)
Einen eigentümlichen Weichglüh- oder Temperofen
verwendet Georg Fischer in Hainfeld, Oesterreich (* D.
R. P. Nr. 27 099 vom 8. Juli 1883). Der in Fig. 10
Taf. 26 ersichtliche Ofen besteht aus drei schrägen über einander angeordneten
Ofenschächten A, A1, A2, von denen die beiden unteren mit
Feuerungen B bezieh. l
versehen sind. Die Decken der Schächte werden von feuerfesten Röhren b gebildet. Auf den Sohlen liegen Schienen a, auf welchen die mit den zu glühenden Guſsstahlwaaren
gefüllten cylindrischen Gefäſse E bezieh. geeignet
construirte Wagen nach unten zu den Entleerungsöffnungen p und h rollen.
Die Guſsstücke werden durch die mittels des Schiebers f
zu schlieſsende Oeffnung e im Kanäle C und den Schacht D in die
Schächte A, A1, A2 gebracht. In C ist zu diesem Zwecke eine Windevorrichtung d angeordnet. Während die Beschickung durch die Oeffnung e erfolgt, gelangen die Verbrennungsgase aus A direkt nach c, anstatt
wie sonst von e nach g.
Die Feuergase der kleinen Feuerung l treten durch die
Oeffnungen m in der Decke von A1 nach A2 und gelangen von hier zur Esse n. In A ist bei i eine Vorrichtung angebracht, um immer eines der
Gefäſse E herausnehmen zu können, während das
nächstfolgende festgehalten wird. Die Gefäſse E sind
entweder Hohlcylinder, in welche die zu glühenden Stücke gesteckt und die von
Deckeln geschlossen werden, deren Ränder die Schienen a
umschlieſsen, oder es werden dazu feuerfeste Wagen benutzt, welche 2 Achsen mit je 2
Rädern und Verschluſsdeckel besitzen. Der Schacht A
soll zur eigentlichen Temperung der Guſsstahlwaaren dienen, die Schächte A1 und A2 dagegen nur zur
Vorwärmung derselben. Weiteres über diesen eigenthümlichen Ofen läſst sich aus der
Patentschrift nicht entnehmen.
Tafeln
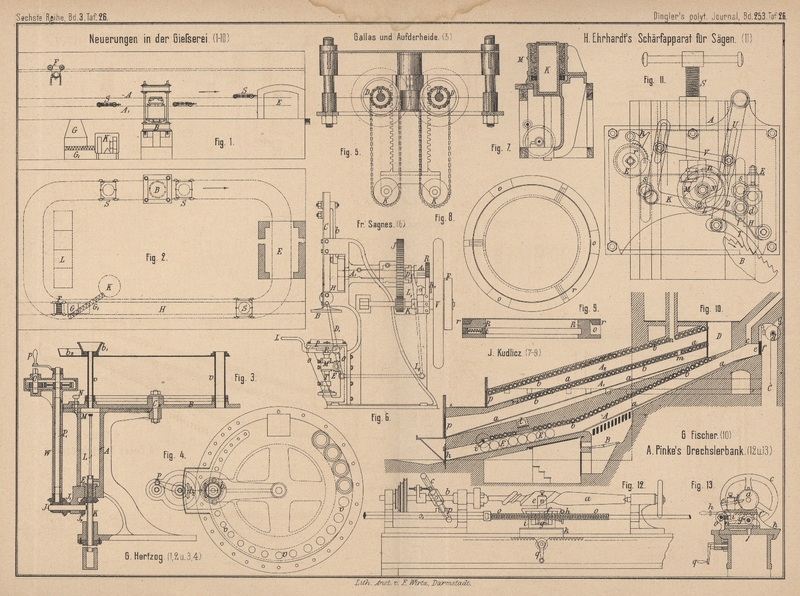