Titel: | Ueber die chemische Verarbeitung von Metallen. |
Fundstelle: | Band 244, Jahrgang 1882, S. 210 |
Download: | XML |
Ueber die chemische Verarbeitung von
Metallen.
Mit Abbildungen auf Tafel 17.
Ueber die chemische Verarbeitung von Metallen.
Bei dem in Fig. 16 bis
19 Taf. 17 dargestellten Ofen mit Erdölheizung
für Goldarbeiter von R. Schade in
Sorau (* D. R. P. Kl. 40 Nr. 16 325
vom 17. Mai 1881) trägt der Dreifuſs a den
Schmelzraum u, welcher unten und nach auſsen einen
breiten Rand, innen zwei ringartige Ansätze hat, von denen der unterste t weit nach innen vorspringt und dazu dient, an dieser
Stelle die Luftzufuhr zu vermindern, wie auch die Flamme zu concentriren, während
der obere, kleinere als Stütze für den Tiegelträger l
bestimmt ist. In der Mitte des letzteren steht der Tiegel g, umgeben von dem Reflectorring k.
Unmittelbar über dem Schmelzraum u befindet sich der
Emaillirraum y (Fig. 18);
derselbe hat einen vorspringenden, viereckigen, schrägen Ansatz mit beweglicher
Klappe und rundem Glimmerfenster o zum Beobachten. Der
Emaillirraum enthält einen mehr als halbkreisförmigen Ring r, um die Hitzeausstrahlung nach der Auſsenwand zu mildern, mit zwei
einander gegenüber stehenden gezahnten Ansätzen r1, sowie einen die Kreislinie des Ringes ergänzenden
Vorsetzer p. Die gezahnten Ansätze nehmen den
dachartigen Reflector s auf, welcher die empor
schieſsenden Flammen gegen das Innere des Tiegels zurückwerfen soll. Der mittels c verstellbare Dochtbehälter e hat am oberen äuſseren Rande einen breiten vorspringenden Ring, um eine
wagrechte Luftströmung zur Flamme zu veranlassen. In dem mit nach innen
vorspringenden Ring versehenen Dochtbehälter ruht auf drei Ansätzen der mit
Auflagerand versehene Tiegel f, welcher das bei
etwaiger Undichtheit des Schmelztiegels herab fallende Edelmetall auffängt. Der
Deckel x dient zum Auslöschen der Flamme, während die
Bodenplatte bei d mit einem Kreis von Oeffnungen
versehen ist.
Die Emaillireinrichtung (Fig. 19
Taf. 17) besteht aus einer mit Hinterwand versehenen Röhre m aus reinem Nickelblech o. dgl., deren offenes Ende in die runde Oeffnung
des halbkreisförmigen Einsatzes n eingeführt wird. Die
Scheidewand b dient dazu, die zu emaillirenden
Gegenstände aufzunehmen, wie auch gleichzeitig die zu heftige Unterhitze zu mildern.
Der oberhalb der Röhre befindliche Reflector s1 bezweckt, die Oberhitze zu vermehren, so daſs
durch Platte und Reflector im Emaillirrohr ein gleichmäſsiger Hitzegrad
entsteht.
G. A.
Dick in London (D. R. P. Kl. 40 Nr. 17161 vom 8. Juni 1881) empfiehlt Metalllegirungen, welche auſser Eisen nicht mehr als 12
bis 15 Proc. Zinn und Kupfer, 10 Proc. Blei und 2 Proc. Phosphor enthalten. Zur
Erzielung einer besonders dichten Legirung fügt man noch etwas Silicium hinzu. Als
Lagermetall soll eine Legirung dienen aus 80 Th.
Eisen, welches 0,4 Silicium, 0,2 Kohlenstoff und 0,3 Phosphor enthält, 8 Th. Kupfer,
8 Th. Zinn und 4 Th. Blei, oder es werden 16 Th. Eisenschwamm mit 1,5 Th. Kupfer und
2,5 Th. 5 Proc. Phosphor enthaltendes Zinn zusammengeschmolzen.
W. Koppel in Manchester (Englisches Patent Nr. 280 vom
22. Januar 1881) will zur Herstellung von Lagermetall
10 Th. Eisen mit 10 Th. Kupfer und 18 bis 20 Th. Zink zusammenschmelzen.
Um Eisen zu galvanisiren, wird
dasselbe nach J. Elmore in
London (D. R. P. Kl. 48 Nr. 17406 vom
11. October 1881) mit verdünnter Säure gereinigt, gespült, in eine
Zinksalzlösung gebracht und mittels einer dynamo-elektrischen Maschine Zink auf dem
Eisen galvanisch niedergeschlagen. Um der Zinkoberfläche Metallglanz zu verleihen, führt man
den galvanisirten Gegenstand rasch über ein Feuer hinweg oder bringt ihn in eine
Kammer, deren Temperatur eben hinreicht, das Zink zu schmelzen.
Um Metallgewebe galvanisch mit Nickel,
Kupfer oder Silber zu überziehen, wird es nach J. Lang in
Schlettstadt, Elsaſs (* D. R. P. Kl.
48 Nr. 15768 vom 17. Mai 1881) zu einem endlosen Bande zusammengenäht und
dieses Band durch zwei Walzen straff ausgespannt, welche mit einer die Elektricität
nicht leitenden Masse überzogen sind. Die Lagerung der Walzen in dem sie tragenden
Rahmen ist ebenfalls isolirt, wie auch dieser gegen die eine Elektrode, welche aus
einer parallel zum ausgespannten Metalltuch befestigten Platte besteht. Als zweite
Elektrode dient eine die ganze Gewebebreite berührende Metallwalze, welche sich beim
Drehen der beiden Spannwalzen in dem Rahmen mit bewegt. Durch Niederlassen des
Rahmens senkt man nun sowohl das Metallgewebe, als auch Walzen und Elektrode in eine
elektrolytische Flüssigkeit und läſst die Walzen langsam drehen. Der elektrische
Strom wirkt nun auf die Flüssigkeit so lange ein, bis die Vernickelung des
Metallgewebes erfolgt ist. Man unterbricht dann den Strom, hebt den Rahmen hoch und
entfernt das Gewebe.
Die bereits mehrfach (1865 177 40.
1866 179 372) erwähnte Verkupferung von Eisen und Stahl mit alkalisch-organischen Kupferlösungen
nach F. Weil wird nach dessen neueren Mittheilungen
(Comptes rendus, 1881 Bd. 93 S. 1018 und 1072) in
der Weise ausgeführt, daſs man die Eisengegenstände in die Kupferlösung eintaucht
und mit Zinkdraht verbindet, oder daſs man mit Natronlauge gefüllte Thonzellen in
die Lösung hängt und die zu verkupfernden Gegenstände mit einer in die Natronlauge
eintauchenden Zinkplatte durch einen Kupferdraht verbindet. Ist die Natronlauge mit
Zinkoxyd gesättigt, so scheidet man dieses mit Schwefelnatrium aus, um die
regenerirte Natronlauge aufs Neue verwenden zu können. Der Kupfergehalt der Lösung
wird mittels Zinnchlorür titrirt (vgl. 1870 198 413).
Mignon und Rouart (Comptes rendus, 1882 Bd. 94 S. 63) heben hervor, daſs
entgegen den Angaben Weil's in Val d'Osne eine saure
Lösung einer organischsauren Kupferalkaliverbindung zum Verkupfern verwendet
werde.
Um beim Verzinken von Draht eine
reine Oberfläche des letzteren, ohne Erhöhungen und Zinktropfen zu erhalten, führen
Witte und Kämpfer in Osnabrück (* D. R. P. Kl. 7 Nr. 17165 vom 8. Juni 1881) die Drähte
direct aus dem Zinkbad durch Oeffnungen, welche durch die über einander greifenden
Zinken zweier Kämme gebildet werden. Diese Oeffnungen müssen den Draht genau um
schlieſsen; jedoch besorgen nicht diese das Abstreifen des dem Draht noch
anhaftenden Zinkes,
sondern ein sich vor den Oeffnungen gleich nach Beginn des Betriebes bildendes
Röhrchen aus festem Zink. Um die Bildung eines solchen zu befördern, muſs die
Entfernung der Kämme von der Oberfläche des Zinkbades an der Stelle, wo der Draht
aus demselben austritt, sowie die Geschwindigkeit des Drahtes eine durch Erfahrung
festzustellende sein, da sonst das den Draht umhüllende Zink fest geworden ist, ehe
es die Kämme erreicht, oder das noch flüssige Zink erst hinter den Kämmen hart wird;
in beiden Fällen kann natürlich von einer Röhrenbildung nicht die Rede sein.
Der untere Kamm steht fest, während der obere gegen jenen nach oben drehbar ist. Es
ist diese Anordnung nothwendig, um leicht neue Drahte einlegen und
Verbindungsstellen der Drähte durchführen zu können.
Das Verfahren scheint praktisch zu sein, da die Durchgangsöffnung für den Draht,
vorausgesetzt, daſs eine Röhrenbildung wirklich stattfindet, durch immer neu
zugeführtes und sofort erkaltendes Zink immer gleich bleibt. Jedenfalls verspricht
es mehr, wie das Bedecken des Zinkbades mit festgeklopftem Sand, welch letzterer das
überflüssige Zink zurückhalten soll. Denn hierbei werden die Durchgangsöffnungen
durch die Erzitterungen des Drahtes fortwährend erweitert und können nur durch
erneutes Andrücken des Sandes wieder geschlossen werden.
Joh.
Schreiber in Düsseldorf (* D. R. P. Kl. 7 Nr. 16445 vom 23. April 1881) ordnet beim
Verzinnen von Blechen 5 Kessel A bis E (Fig. 21
Taf. 17) an; davon sind die letzten 4 geheizt, dagegen ist A durch einen Luftkanal gekühlt. Der Kessel B
enthält das unreinste Zinn, welches behufs Vermeidung der Oxydation von einer etwa
9cm hohen Palmölschicht bedeckt ist. Da der
Schmelzpunkt dieses Zinnes ein relativ hoher ist und in Folge dessen das Palmöl zu
heiſs werden würde, so muſs letzteres von Zeit zu Zeit abgekühlt werden, was durch
Ausschöpfen in den Kessel A geschieht. Der Kessel C enthält reineres, D das
reinste Zinn; in beiden wird die Oberfläche des Metalles, von einer nur 2cm hohen Fettschicht bedeckt. In dem in A befindlichen Palmöl werden die Bleche liegend
vorgewärmt und sodann in senkrechter Stellung in die Zinnbäder B, C und D untergetaucht.
Bevor die Bleche nach D kommen, wird das überflüssige
Zinn mittels eines Wergwisches entfernt. Hierauf führt man die Bleche behufs
Glättung der Oberfläche durch die in entgegengesetzten Richtungen rotirenden beiden
linken Walzen in den Kessel E, welcher bis zur
Walzenmitte mit Palmöl von der ungefähren Temperatur des schmelzenden Zinnes gefüllt
ist, damit die Bleche nicht erkalten. Unterhalb der Walzen werden die Bleche von
einem Korb k aufgenommen, welcher durch den aus einem
Stück bestehenden Hebel ht und die Lenkstangen r, beim Zurückdrücken des Hebels h nach links, die Bleche den beiden rechts liegenden,
entgegengesetzt rotirenden Walzen W wieder zuführt, so
daſs die Bleche oberhalb der Walzen geglättet austreten. Die Walzen sind aus
polirtem Stahl und behufs schnellerer Erwärmung beim Beginne des Betriebes hohl.
Zum Einfetten von Metallblechen, welche
durch Eintauchen in ein Metallbad mit einem Metallüberzuge versehen werden
sollen, werden die Bleche nach R. J. Hutchings in
Swansea (* D. R. P. Kl. 7 Nr. 15270
vom 30. März 1881), statt sie vor dem Verzinnen oder Verzinken in ein
Talgbad zu tauchen, durch zwei Walzen hindurch gelassen, welche sich unmittelbar
über dem das Metallbad enthaltenden Behälter befinden und deren poröse Oberfläche
mit Fett getränkt ist. Zu diesem Zweck sind die Walzen B (Fig. 20
Taf. 17) hohl und werden durch das seitliche Rohr e mit
Oel oder geschmolzenem Talg versorgt. Die Mantelwand ist mit Oeffnungen a versehen, durch welche das Fett in die Filzschicht
D gelangt.
Patina. Wie aus den Verhandlungen des Vereines zur Beförderung des Gewerbfleiſses (Sitzungsberichte, 1882 S. 4 und 48) hervorgeht, ist die
Patina-Commission zu dem Resultat gekommen, daſs Bronzen von verschiedenster
Zusammensetzung eine schöne, grüne Patina annehmen können. Die Patinabildung wird
gefördert durch häufiges Abwaschen der Bronzen und Abreiben derselben mit Oel. (Vgl.
Brühl 1882 243 251.)
Elster empfiehlt zur künstlichen Patinirung das
weinsaure Kali-Kupferoxyd-Ammoniak. Kupferzinnlegirungen geben eine weit bessere
Oberfläche als Kupferzink; doch wird mit der Zeit aus jeder Kupferzinnlegirung
Kupfer ausgeschieden, welches als grünes Oxyd herunterläuft. Um eine gute Patina zu
erhalten, soll man statt der jetzt gegebräuchlichen Kupferzink- wieder
Kupferzinnbronze anwenden, welche sich allerdings schwieriger bearbeiten läſst als
erstere, auſserdem aber die im Freien stehenden Denkmäler jährlich in der heiſsesten
Jahreszeit mit der erwähnten Kupferlösung behandeln. Die schlecht erhaltenen
Pferdebändiger auf der Berliner Schloſsterrasse enthalten 18 Proc. Zink und 2 Proc.
Zinn. Daſs die ebenso zusammengesetzte Bronze des Dianabrunnens in München eine
bessere Oberfläche zeigt, ist lediglich dem Kalk haltigen Wasser zu verdanken. Die
schönen griechischen Bronzen zeigen bis 13 Proc. Zinn. Besonders empfehlenswerth
erscheint die Kupferaluminiumbronze, aus welcher z.B. die Widmungstafel am
Stein-Denkmal gegossen ist.
R. Weber fand in der schwarzen Kruste, durch welche in
den letzten Jahrzehnten die Patina der Bronze des Groſsen Kurfürsten sehr gelitten
hat, 5,7 Proc. Schwefel, so daſs hier die sonst so schöne Patina durch den
Schwefelwasserstoffgehalt der Luft verdorben ist. Die schwarze Kruste des
Friedrich-Denkmales enthielt dagegen nur 0,76 Proc. Schwefel, so daſs hier die
Schwärzung offenbar andere Ursache hat. Weber tauchte
nun in Wasser, welches kohlensaures Kupfer suspendirt enthielt, Kupferzinn- und
Kupferzinkplatten und leitete hin und wieder Kohlensäure in die Flüssigkeit. Nach
einigen Monaten war die Kupferzinnbronze durch das von der Kohlensäure gelöste und
auf ihr niedergeschlagene Kupfer geröthet und grüne Massen hatten sich an dem in die
Luft ragenden Plattentheil gebildet. Die Kupferzinkplatte dagegen war dunkel
gefärbt, fast schwarz und hatte ganz die Färbung des Metalles des Standbildes des
Groſsen Friedrich, dessen Bronze 10 Proc. Zink und nur 1 Proc. Zinn enthält. Auf
Kupferzinklegirungen entsteht demnach durch Kupferlösungen eine schwärzende Schicht
(vgl. Braconnot 1834 53
133). Die stark Zink haltigen Legirungen, wie das Metall des Friedrich-Standbildes,
oxydiren an der Luft, unter Abgabe namhafter Mengen von Metall, so daſs die
Oberflächen rauh werden und die feinen Umrisse ihre Zartheit verlieren. Dabei findet
denn in den bei weitem meisten Fällen eine Schwärzung der Oberfläche auch ohne
Mitwirkung von Schwefel statt. Die Zinnbronze dagegen, so am Groſsen Kurfürst, an
dem Geschützmetall der Kanone vor dem Zeughaus, verhält sich den Atmosphärilien
gegenüber entschieden widerstandsfähiger; die feinen Conturen bleiben selbst während
langer Zeiträume erhalten. Auch der Bildung grüner Patina ist die Kupferzinnlegirung
entschieden günstiger; doch kann sich unter günstigen Umständen auch die schwarze
Schicht auf den Kupferzinkbronzen durch Oxydation grün färben, z.B. bei lang
dauernder Benetzung.
Das bekannte Standbild in Düsseldorf, dessen Bronze 24 Proc. Zink, 2 Proc. Zinn und 1
Proc. Blei enthält, ist auf der oberen Rückenfläche mit einer schönen grünen Patina
überkleidet, sowie auch auf der Brustseite des Reiters; der Pferdebauch dagegen ist
an vielen Stellen dunkel, ferner auch der Rücken des Reiters. An den Stellen, wo der
Regen herabrieselt und sich hält, ist der grüne Ueberzug entstanden, die
abgewendeten Theile dagegen sind dunkel. Hier mögen auf die Oxydation jener
schwarzen Schicht die Rheinnebel günstig eingewirkt haben. Unter solchen der
Aufstellung des Friedrich-Denkmals gegenüber besonderen Umständen mögen dann auch
auf an Zink reichen Legirungen Patinen entstehen können, welche Oxydationsproducte
der Oberflächenschichten des schwarzen Körpers auf solchen Standbildern sein
dürften. Die Feinheit der Conturen ist indessen entschieden weniger gut erhalten als
bei Zinnbronzen. Besonders stark sind zur Schwärzung die Arsen haltigen Bronzen
geneigt; Kupferplatten mit nur 0,13 bis 0,25 Proc. Arsen färben sich an der Luft
schwarz.
Entgegen der Angabe von Gladenbeck, daſs das Zink ein
für den Gieſser nothwendiger Zusatz sei, bemerkt Weber,
daſs das Blei, welches als Bindemittel vielfach angewendet wird, weniger bedenklich
sein dürfte als Zink. Daſs man auch Bronzen ohne erheblichen Zinkzusatz gieſsen kann, beweisen die
Analysen der Mehrzahl der Bronzen, welche der Verein hat untersuchen lassen. So
enthielten die Bronzen in Potsdam (Schäfer am Teich, Bachus, Germanicus) neben 9,14
Proc. Zinn 1,28 Zink, neben 7,50 Zinn 1,64 Zink und neben 6,16 Zinn 2,35 Zink, die
bayerischen Bronzen zu Augsburg 1,24 Zinn, 0,50 Zink; 8,17 Zinn und 0,0 Zink. Zwei
Figuren in München 4,18 Zinn und 0,44 Zink:, 4,77 Zinn und 0,28 Zink. Die Bronze in
den Sklaven des Groſsen Kurfürsten zeigte 7,5 Zinn und 0,48 Zink, während die
Hauptfigur neben 7,5 Proc. Zinn 1,38 Proc. Zink enthält. Es ist richtig, daſs ein
Zinkgehalt den Bronzeguſs erleichtert; allein man kann ihn, wie jene Beispiele
zeigen, sehr abmindern und es kommt doch in solchen Fällen mehr darauf an, ein gutes
Gebilde zu erzielen, als die Arbeit des Gieſsers zu erleichtern.
Was die Oberflächenbeschaffenheit betrifft, so lehrt die Erfahrung, daſs poröse
Metallflächen sich rascher oxydiren; was aber rasch entsteht, verschwindet rasch,
die lockeren Oxydschichten haften nicht. Daraus erklärt sich die Ansicht der
Künstler, daſs die Bronze gehämmert werden muſs; das Hämmern verdichtet eben die
Oberfläche.
Ueber die Wolframbronzen macht J. Philipp (Berichte der
deutschen chemischen Gesellschaft, 1882 S. 499) weitere Mittheilungen (vgl.
1880 236 87). Zur Untersuchung derselben erhitzt man die
fein gepulverte Bronze mit einem groſsen Ueberschuſs von ammoniakalischer
Silberlösung in einer Porzellanschale zum Sieden. Das ausgeschiedene Silber wird
abfiltrirt und, um das Durchgehen desselben durch das Filter zu verhüten, mit etwas
Ammoniumnitrat und Ammoniak haltigem Wasser ausgewaschen. Das Filtrat wird, nachdem
der gröſste Theil des Ammoniaks durch Abdampfen verjagt ist, mit Salpetersäure
versetzt, zum Kochen erhitzt, worauf man nach 12stündigem Stehen die ausgeschiedene
Wolframsäure abfiltrirt und mit verdünnter Salpetersäure auswäscht. Aus dem Filtrat
fällt man das überschüssige Silber durch Salzsäure, trocknet die Lösung ein,
befeuchtet den Rückstand mit Ammoniak, verdunstet nochmals und erhitzt mit
Salzsäure, wodurch noch wenige Milligramm Wolframsäure erhalten werden. Im Rest wird
das Natron als Chlornatrium bestimmt.
Bei genügend Material empfiehlt es sich, die Bestimmung des Silbers einerseits, die
der Wolframsäure und des Natrons andererseits in gesonderten Mengen auszuführen; für
letzteren Zweck eignet sich vortrefflich das von Woehler angegebene Verfahren, nach welchem die Bronze mit Schwefel im
bedeckten Tiegel geschmolzen und die erhaltene grauschwarze Masse durch Erhitzen mit
Königswasser zersetzt wird. Die ausgeschiedene, schön gelbe, leicht zu filtrirende
und auszuwaschende Wolframsäure wurde, ohne die Flüssigkeit zur Trockniſs
abzudampfen, direct filtrirt und mit Salpetersäure ausgewaschen. Die blaue Bronze muſs mit
ammoniakalischer Silberlösung im zugeschmolzenen Rohr mehrere Stunden auf 120°
erhitzt werden; in offenen Gefäſsen ist die Zersetzung unvollständig. Für die
Bestimmung des Wolframs und Natriums in der blauen Bronze ist, entgegen der Angabe
von Scheibler, die Woehler'sche Methode gleichfalls
vortrefflich zu verwenden; nur ist es nöthig, das feine Pulver mit Schwefel 7 bis 8
mal im bedeckten Tiegel zu schmelzen und jedesmal den überschüssigen Schwefel durch
Erhitzen zu verjagen. Die entstandene Schwefelververbindung wird alsdann leicht und
in kurzer Zeit durch Königswasser oxydirt. Auch das von Scheibler angewendete Schmelzen mit Aetzbaryt gibt gute Resultate, ist
aber umständlicher und in Folge der Nothwendigkeit, gröſsere Mengen von Bariumsulfat
auszuwaschen, langwieriger.
Nach der von Wright angegebenen Methode wurden 4 Arten
von Wolframbronzen erhalten, welche sich durch goldgelbe, rothgelbe, purpurrothe und
blaue Farbe unterscheiden. Die ersten beiden krystallisiren stets in würfelähnlichen
Formen, die rothe Verbindung wurde theils in Würfeln, theils in formlosen Stücken,
die blaue endlich in Krystallen von prismatischer Form erhalten. Unter sonst
gleichen Bedingungen werden aus an Säure ärmeren Gemischen die ersteren Bronzen, aus
an Säure reicheren die letzteren erhalten. Die gelben Bronzen werden in schönen,
groſsen Krystallen erhalten, wenn man ein Gemisch von 2 Mol. normalen
Natriumwolframiates und 1 Mol. Wolframsäureanhydrid zum Schmelzen erhitzt,
allmählich 40 bis 50 Proc. Zinn hinzugefügt und das Ganze 1 bis 2 Stunden in ruhigem
Fluſs erhält. Unter noch nicht festgestellten Bedingungen bilden sich hierbei auch
rothgelbe Krystalle. Die Zusammensetzung der gelben Bronze entspricht der Formel
Na5W6O18, die der rothgelben Na4W5O15.
Eine Verbindung von der Zusammensetzung NaWO3
scheint nach neueren Versuchen nicht zu bestehen. Durch entsprechende Behandlung
eines Gemisches von 2 Mol. Na2O auf 5 bis 6 Mol.
WO3 wurde schön purpurroth gefärbte Bronze
erhalten; noch saurere Gemische geben blaue Krystalle. Alle diese Bronzen zeigen ein
Volumgewicht von 7,2 bis 7,3.
Fortgesetzte Versuche ergaben, daſs man durch Zersetzung von sauren
Natriumwolframiaten mit Zinn Wasserstoff oder durch den elektrischen Strom
Reductionsproducte erhält, welche je nach der Farbe eine verschiedenartige
Zusammensetzung zeigen. Von diesen sind dargestellt: eine rein goldgelbe (Na5W6O18), eine rothgelbe (Na4W5O15),
eine purpurrothe (Na2W3O9) und endlich eine blaue Verbindung
(Na2W5O15). Die Wolfram bronzen entstehen aus sauren
Natriumwolframiaten durch Verlust von Sauerstoff und zwar wird stets auf 2 Atome
Natrium 1 Atom Sauerstoff entzogen.
Tafeln
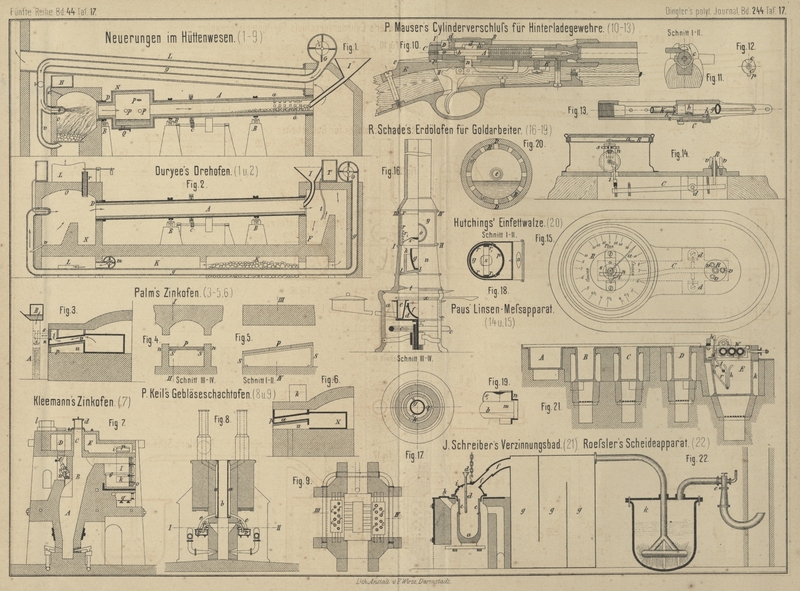