Titel: | Ueber einige Kesselexplosionen. |
Autor: | Whg. |
Fundstelle: | Band 242, Jahrgang 1881, S. 243 |
Download: | XML |
Ueber einige Kesselexplosionen.
Mit Abbildungen auf Tafel 19.
Ueber einige amerikanische Kesselexplosionen.
Dem Scientific American sind die folgenden Angaben über
einige Explosionen von Dampfkesseln entnommen, welche in diesem Jahre in Amerika
stattgefunden haben.
Am 1. Juni 1881 in der Mittagsstunde explodirte in der Färberei von Gafney und Comp. in Kensington, Philadelphia, ein
einfacher Cylinderkessel, wobei 3 Personen getödtet und 8 verwundet wurden (vgl. a. a. O., 1881 Bd. 45 S.
20). Der Kessel hatte 0m,9 Durchmesser, war 9m lang und an beiden Enden mit ebenen guſseisernen Böden von 48mm Dicke versehen. Die Böden waren mit einer nach
innen gerichteten Flansche von 41mm Dicke an den Kessel genietet. In der Mitte des
einen Bodens war ein Mannloch von 394mm Breite und
324mm Höhe ausgespart, dessen Rand nur innen
durch eine schmale Arbeitsleiste verstärkt war. Diese Verstärkung war aber durch
Fortnahme der harten Kruste beim Hobeln jedenfalls reichlich aufgehoben. Der
Mannlochdeckel selbst war nicht bearbeitet, so daſs
schon durch das Aufschrauben desselben erhebliche Spannungen im Kesselboden
entstehen konnten. Rechnet man noch hinzu, daſs auch vom Gieſsen her, besonders am
Rande, Spannungen in dem Eisen vorhanden sein konnten, so liegt es auf der Hand,
daſs ein solcher Kesselboden selbst von dem ausgezeichnetsten Material nicht sehr
widerstandsfähig sein konnte, wie es auch durch die erwähnte Explosion erwiesen
wurde. Und doch sollen derartige Kessel mit gegossenen Stirnplatten in den
Vereinigten Staaten von Nordamerika auſserordentlich verbreitet sein. Der explodirte
Kessel war noch neu, erst im März aufgestellt und nebst zwei ganz gleichen Kesseln,
die schon seit 2 Jahren im Betrieb waren, mit Wasserdruck auf 6at,48 geprüft. Die zulässige Betriebsspannung
betrug 4at,42. Die beiden Sicherheitsventile des
Kessels hatten je 5cm Durchmesser und es scheint,
daſs dieselben nicht genügten, bei geringem Dampf verbrauch ein Steigen der Spannung
über die zulässige Grenze zu verhindern. Eine solche Steigerung der Spannung wird
wenigstens als die Ursache jener Explosion angesehen, da man sämmtliche
Absperrventile in den verschiedenen Zweigen der von dem Kessel ausgehenden
Dampfleitung nach der Explosion geschlossen fand. Die vordere mit dem Mannloch
versehene Stirnplatte barst durch zwei diagonale Risse in vier Theile (vgl. Fig.
7 Taf. 19), welche dann durch einen ringsum laufenden Sprung von der
Flansche abgetrennt wurden. Diese Theile und der Kessel selbst wurden nach
entgegengesetzten Richtungen weit fortgeschleudert und richteten arge Zerstörungen
an. Die hintere Stirnplatte wie auch der Mantel am hinteren Ende wurden,
wahrscheinlich beim Sturz des Kessels, eingedrückt. Im Uebrigen blieb der Mantel
unversehrt.
Am rathsamsten dürfte es jedenfalls sein, guſseiserne Kesselböden überhaupt nicht zu
verwenden. Will man aber nicht davon abgehen, so sollte man wenigstens solche Formen
wählen, welche den Eigenschaften des Guſseisens entsprechen, d.h. welche eine
Inanspruchnahme des Materials auf Zug möglichst ausschlieſsen, oder doch auf das
geringste Maſs zurückführen und welche bewirken, daſs die Belastung durch den
Dampfdruck hauptsächlich nur Druckspannungen hervorruft. Dieser Bedingung scheint
z.B. die Form Fig. 8
ziemlich gut zu
entsprechen. Der Boden ist hier nach innen gewölbt, die Flansche nach auſsen
gerichtet und das Mannloch durch eine kräftige Rippe versteift.
Daſs auch Schmiedeisen unter ähnlichen Umständen nicht widerstandsfähig genug ist,
zeigt eine andere Explosion, welche am 15. Januar 1881 in dem Lagerhaus von Creery und Comp. in New-York stattfand (vgl. Scientific American, 1881 Bd. 44 S. 98). Der Dampf
wurde hier zur Heizung und zum Betrieb der Elevatoren benutzt. Der Kessel war 10
Jahre alt und im August 1880 mit Wasserdruck auf 7at,4 geprüft. Die zulässige Spannung betrug 5at, die gewöhnliche Betriebsspannung durchschnittlich 3at,5. Bei der Explosion wurde der Deckel des
Dornes, welcher, wie die besprochene Kesselstirnwand, in der Mitte mit einem
Mannloch versehen war, durch einen diametralen Riſs in zwei Hälften getheilt und am
Rande rings herum abgerissen. Auſserdem zeigten die beiden Theile noch mehrere
radiale Risse. Diese Zerstörung – bei welcher glücklicherweise Niemand beschädigt
wurde – fand also in ganz ähnlicher Weise wie bei der guſseisernen Stirnplatte
statt, obgleich hier auſser einem das Mannloch einfassenden Ring noch sechs schräge
Anker angeordnet waren (vgl. Fig. 9 Taf.
19), welche den Deckel mit dem Mantel des Dornes verbanden. Bei der Explosion rissen
die Ankernieten am Deckel ab. Die Ursache des Unfalles scheint nicht aufgefunden zu
sein; jedenfalls genügt die im Scientific American
gegebene Erklärung, daſs nämlich die Anker bei steigender Temperatur wegen ihrer
gröſseren Erwärmung sich immer mehr als der Dommantel ausgedehnt und so ein
fortwährendes Aus- und Einbiegen des Deckels bewirkt haben, nicht, da die Differenz
in den Dehnungen zu gering ist. Das Blech war an den Bruchflächen durchaus gesund
und abgetrennte Versuchsstreifen erwiesen sich zäh und fest. Eine relative
Verschwächung des Bleches am Rande ist nicht auffällig, da dasselbe beim Umbördeln
hier stark zu leiden hat. Auch eine steilere Anordnung der Anker (vgl. Fig.
9 bei A), wie sie vorgeschlagen ist, wird
kaum die Construction fester machen. Der Kessel hatte mit gedämpftem Feuer und
geschlossenem Rauchschieber in der Nacht von Sonnabend auf Sonntag still gelegen. Am
Sonntag Mittag um 12 Uhr 30 Min. will der Kesselwärter nur 0at,2 Ueberdruck am Manometer gefunden haben. Um 4
Uhr 30 Min. Nachmittags fand der Wächter so starken Kohlendunst vor, daſs er die
Fenster öffnete, und gleich darauf fand die Explosion statt. Nach diesen Angaben
dürfte wohl auf einen eingetretenen Siedeverzug zu
schlieſsen sein; wenigstens wird damit die Explosion am einfachsten erklärt.
Jedenfalls hat dieselbe gezeigt, daſs der ausgeschnittene Domdeckel die schwächste
Stelle des Kessels war.
Ein dem zuerst beschriebenen gleicher, nur etwas kleinerer Kessel explodirte, jedoch
in anderer Weise, am 10. Juni 1881 in dem Walzwerke von C. M. Atkins nahe bei Pottsville, Pennsylvanien, wobei ebenfalls drei
Personen ums Leben kamen (vgl. Scientific American,
1881 Bd. 45 S. 34). Die Länge des Kessels betrug 7m,9, sein Durchmesser 0m,76. Er war i.
J. 1870 hergestellt, aus 11 Schüssen zusammengesetzt, in Längs- und Quernähten
einfach genietet. Im April 1873 wurde er in Betrieb genommen und war seitdem mit
Unterbrechungen, im Ganzen 76 Monate (die einzelnen Monate und Tage
zusammengezählt), in Benutzung gewesen. Er war im Verein mit einem zweiten gleichen
Kessel über einem Puddelofen aufgestellt (vgl. Fig. 10
Taf. 19). Die Dampfspannung hatte zwischen 4 und 4at,7 geschwankt; bei der letzteren Spannung hatte das Sicherheitsventil
abgeblasen. Die Enden der Kessel waren mittels angenieteter Oesen aufgehängt und
auch durch Mauerwerk unterstützt. Auſserdem scheint auf der ganzen Länge eine
weitere Unterstützung nicht vorhanden gewesen zu sein, so daſs die Kessel einer
dauernden Inanspruchnahme auf Biegung ausgesetzt waren. Die guſseisernen Böden waren
in diesem Falle nicht Schuld an dem Unglück; es riſs vielmehr der Mantel in dem
Querschnitt bei a (rechts in Fig. 10)
geradezu ab, und zwar im vollen Blech, nicht in einer Nietnaht. An dieser Stelle
wurde einige Minuten vor der Explosion ein Leck an der Unterseite des Kessels
bemerkt, worauf man Befehl gab, sofort das Feuer zu entfernen. Dies war jedoch nicht
mehr möglich, da mächtige Dampfwolken, aus dem in den Puddelofen niederrinnenden
Wasser entstanden, aus dem Feuerraum hervordrangen. Gleich darauf riſs der Kessel
vollständig aus einander, das kürzere Ende wurde weit fortgeschleudert, während der
übrige Theil, nach der entgegengesetzten Seite ausweichend, den Schornstein C umwarf, bei a
niederstürzte und dann liegen blieb. Die Blechstärke betrug an der Bruchstelle 5mm,3.
Wie dick das Blech ursprünglich war, ist nicht angegeben. Jedenfalls hatte die
Unterseite des Kessels bei a durch die aus dem
Puddelofen in einem senkrechten Kanal aufsteigenden Heizgase, welche hier fast
normal auf den Kessel stieſsen, sehr zu leiden. Wenn allerdings, wie im Scientific American angegeben ist, das Blech am ganzen
Umfange des Bruchquerschnittes gleiche Stärke hatte, so ist anzunehmen, daſs der
Kessel von vorn herein aus dünnem Blech hergestellt war. Ein Ausflicken oder eine
sonstige Ausbesserung des Kessels war nie nöthig gewesen. Der Kesselstein war erst
kurze Zeit vor der Explosion ausgekratzt. Irgend welche Fehler konnten am Kessel
nicht aufgefunden werden. Es muſs demnach als einzige Ursache der Explosion die
Einwirkung der Stichflamme angesehen werden. Durch dieselbe im Verein mit den
zeitweiligen Abkühlungen muſs die Beschaffenheit des Bleches wesentlich geändert
worden sein, indem es sich an der Bruchstelle krystallinisch und brüchig zeigte.
Auch die Jury war der Ansicht, daſs der Unfall durch die fortwährenden Dehnungen und
Zusammenziehungen
hervorgerufen sei. Der Berichterstatter des Scientific
American will bemerkt haben, daſs Explosionen, bei welchen der Kessel wie
hier in der Querrichtung reiſst, nur in Walzwerken vorkommen, wo die Kessel ähnlich
wie hier aufgestellt und groſsen und plötzlichen Temperaturänderungen ausgesetzt
sind. In einem geringen Grade mag auch die Beanspruchung auf Biegung mit zu dem
Bruche beigetragen haben.
Eine vierte Explosion, die am 12. Juni 1881 stattfand, betraf einen Schiffskessel von
der in Fig. 11
Taf. 19 skizzirten Anordnung (vgl. Scientific American,
1881 Bd. 45 S. 51). Derselbe gehörte dem Schraubendampfboot Baker an, welches als Schlepper und Lichterfahrzeug benutzt wurde und an
der Küste von Virginien vor Anker lag. Drei Neger fanden bei dem Unfall ihren Tod
und ein Neger und ein Weiſser wurden erheblich verbrannt. Der Kessel war i. J. 1877
theils aus Eisen, theils aus Stahl gebaut, 4m,88
lang und 2m,13 im Durchmesser. Er hatte zwei
Flammrohre von 686mm Durchmesser, deren jedes aus
drei Stahlplatten von etwa 6mm,5 Dicke hergestellt
war. Die Platten waren mit Flanschen zusammengenietet. Am hinteren Ende des
mittleren Rohrschusses war eine den Rost tragende Feuerbrücke eingebaut. Die
Flammrohre mündeten hinten in eine Rauchkammer, aus welcher die Heizgase durch 75
enge Rauchröhren nach vorn zurückkehrten, um hier durch den Schornstein zu
entweichen. Es wurde nun der hinter der Feuerbrücke liegende Schuſs des einen
Flammrohres zusammengeklappt, wobei das Blech dicht an der Flansche der hinteren
Rohrplatte auf mehr als der Hälfte des Umfanges aufriſs. Es zeigte sich, daſs das
Blech an dieser Stelle auſserordentlich dünn war, so daſs hierdurch die Explosion
erklärlich ist, auch wenn die Spannung nicht über die zulässige Grenze von 3at,4 gestiegen ist. (Das Urtheil der
Untersuchungscommission lautete, daſs die Explosion durch zu hohen Kesseldruck
herbeigeführt sei.) An der stärksten Stelle, nämlich in den höchsten Punkten des
Risses, betrug die Blechdicke noch 5mm,6. Von hier
an nahm sie aber nach unten hin stetig ab, so daſs die Bruchfläche im tiefsten
Punkte, einer schartigen Messerschneide ähnlich war. Die Ursache dieser
Verschwächung war eine auſserordentlich starke Corrosion auf der äuſseren (Wasser-)
Seite des Rohres. An einigen Stellen war das Blech vollständig durchgefressen. Auch
die untere Fläche des anderen Flammrohres zeigte schon breite Gruben von
unregelmäſsiger Form, die sich über eine groſse Fläche ausbreiteten. Ein
aufgenieteter Flicken (vgl. Fig. 12)
zeigt, daſs an der geschwächten Stelle schon vor einiger Zeit ein Leck bemerkbar
gewesen sein muſs, und es war sicher geboten, schon damals das Blech an der
betreffenen Stelle genau zu untersuchen und zu messen.
Wodurch solche Corrosionen, unter denen besonders Schiffskessel viel zu leiden haben,
hervorgerufen werden, ist, soviel bekannt, noch nicht vollständig aufgeklärt.
Gewöhnlich werden sie auf den Einfluſs der mit dem Speisewasser eingeführten Luft
bezieh. der in der Luft enthaltenen Kohlensäure zurückgeführt und verschiedene
Versuche scheinen dies zu bestätigen. So wurden z.B. von der britischen Admiralty-Boiler-Commission eine groſse Anzahl Eisen-
und Stahlplatten, 100mm lang und breit und 10mm dick, von verschiedenen Werken Englands
entnommen, den verschiedenartigsten Schiffen der britischen Kriegs- und
Handelsmarine gesendet. Die Platten waren blank, doch nicht polirt und wurden in die
Kessel eingelegt. Auf beigefügten Formularen waren von den betreffenden
Oberingenieuren die Gewichtsverluste der Platten regelmäſsig zu verzeichnen. Die
Kessel mit Oberflächencondensatoren wurden nach dem täglich zugeführten Speisewasser
in Gruppen getheilt und da zeigte es sich, daſs in den Kesseln, in welchen während
24 Stunden über 30cm Wasser gewechselt wurden, die
Platten in gleicher Zeit durchschnittlich reichlich 12 mal so viel an Gewicht
verloren als in den Kesseln, in welchen in 24 Stunden nur 7cm,5 Wasserhöhe abgeblasen wurde. Die Corrosion
der Platten war demnach um so gröſser, je mehr Wasser, also auch je mehr Luft und
Kohlensäure dem Kessel zugeführt wurde. Bei einem Vergleich der Stahlplatten mit den
Eisenplatten zeigten die Stahlplatten durchschnittlich einen gröſseren
Gewichtsverlust; doch war der Unterschied nicht bedeutend.
Die Reihenfolge der Eisen- und Stahlsorten war folgende: Staffordshire-Eisen wurde am
wenigsten angegriffen; dann folgte Lowmoor, darauf Tiegelstahl, dann Bessemer- und
endlich Siemens-Martin-Stahl, welcher am meisten corrodirte. Staffordshire-Eisen
verlor für 1qc Fläche in 10 Tagen durchschnittlich
86g und weicher Stahl 107g, wenn ein Oberflächencondensator angewendet
wurde. Bei Benutzung eines Einspritzcondensators war der Unterschied etwas gröſser;
die Verluste betrugen in diesem Falle 83g und
125g.
Hinsichtlich eines Vergleiches von Seewasser mit anderem Wasser lieſs sich
schlieſsen, daſs, wenn (bei Oberflächencondensation) kein Wasser abgeblasen wird,
Seewasser vorzuziehen ist, wenn aber täglich 7,5 bis 30cm Wasser abgeblasen werden, Süſswasser den Vorzug hat. In einem Vorwärmer
betrug der Verlust in 10 Tagen 65g, in dem
zugehörigen Kessel dagegen nur 11g,5, was dadurch
zu erklären ist, daſs die meiste Luft schon in dem Vorwärmer ausgeschieden
wurde.
Der Wasserwechsel in dem explodirten Kessel war nun sehr stark gewesen; es wurden in
24 Stunden 60cm Wasser abgeblasen. Hieraus würde
also nach Obigem eine starke Corrosion sich folgern lassen. Das Speisewasser wurde
allerdings zunächst in einen Vorwärmer geführt und trat, auf 27 bis 38° vorgewärmt,
aus diesem in den Kessel ein. Diese geringe Erwärmung genügte aber jedenfalls nicht,
um die Luft aus dem Wasser abzuscheiden.
Ein lange Zeit auf See gewesener Schiffsingenieur veröffentlicht im Engineer, 1880 Bd. 50 S. 184 folgende Erfahrungen und
Rathschläge betreffs der Schiffskessel: Bei neuen Kesseln soll die erste Sorge sein,
eine dünne Schicht Kesselstein an den Wänden ansetzen zu lassen, was dadurch
erreicht werden kann, daſs man das Seewasser bis auf etwa seine doppelte Dichtigkeit
einkochen läſst. Wo sich eine solche schützende Schicht Kesselstein abgesetzt hat,
kann eine Corrosion nicht stattfinden, ebenso wie sich auch kein Kesselstein
festsetzen wird, wo sich Rost schon gebildet hat. Es ist vortheilhaft, abwechselnd
während einer Wache etwa 12mm Wasser (vom Boden)
abzublasen und während der folgenden ebenso viel abzuschäumen. Als ein wirksames
Schutzmittel gegen Corrosion kann Kalkwasser angesehen werden. In einen Eimer Wasser
wird etwa ¼ Eimer ungelöschten Kalk gethan und das Ganze gut umgerührt. Wenn sich
nach ein paar Stunden der Kalk niedergeschlagen hat, wird das klare Wasser
abgegossen und mit der Speisepumpe in den Kessel eingeführt. Nach Ansicht des
Verfassers soll die Corrosion hauptsächlich verursacht werden durch die galvanische
Wirkung zwischen den kupfernen Speise- oder Condensatorröhren und dem Eisen des
Kessels. Hierfür spricht zunächst, daſs man durch Verzinnung der Röhren sehr
günstige Resultate erzielt haben soll. Wie die Kupfertheilchen in den Kessel kommen,
ist allerdings noch nicht ganz klar gelegt; doch hat die Erklärung sehr viel für
sich, daſs das von der Maschine kommende Fett sich theilweise auf den Kupferröhren
festsetze, eine Oxydation des Kupfers hervorrufe und das Kupferoxyd dann von dem
Speisewasser mit in den Kessel gespült werde. Durch Anwendung von Glycerin als
Schmiermittel soll diese Wirkung verhütet werden.
Sehr empfohlen (u.a. auch von einer von der britischen Admiralität eingesetzten
Commission) werden Zinkeinlagen zur Verhütung der Corrossion der Kessel, jedoch muſs
bei denselben stets für eine vollkommen metallische Verbindung des Zinkes mit dem
Eisen gesorgt werden. Die Oxydation erstreckt sich dann hauptsächlich auf das im
Vergleich mit dem Eisen elektropositive Zink und das Eisen bleibt geschont. Die sich
allmählich auflösenden Zinkstücke müssen selbstverständlich zeitweilig ersetzt
werden. (Vgl. F. Fischer 1876 220 172 ff. Weindig 1876 222 92.)
Whg.
Tafeln
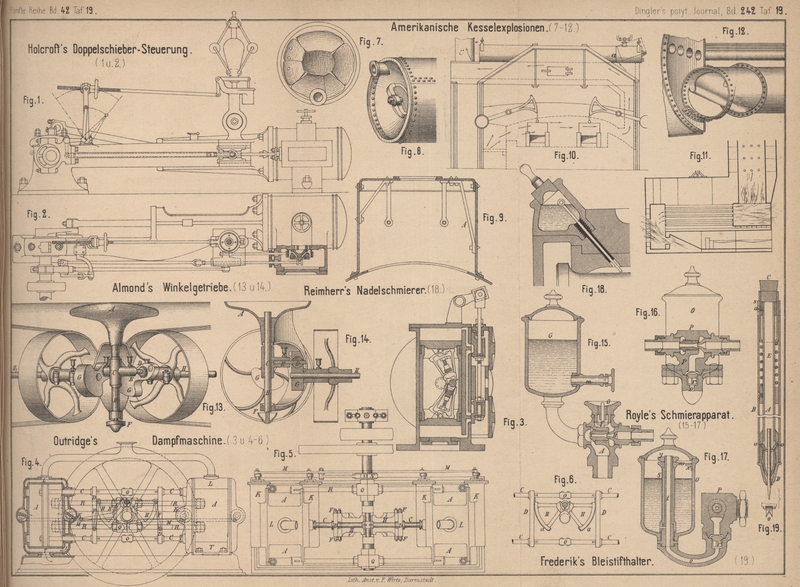