Titel: | Blechrollmaschine für conische (Galloway-) Siederohre; von A. H. C. Bachmann. |
Autor: | A. H. C. Bachmann |
Fundstelle: | Band 237, Jahrgang 1880, S. 184 |
Download: | XML |
Blechrollmaschine für conische (Galloway-)
Siederohre; von A. H. C.
Bachmann.
Mit Abbildungen auf Tafel 16.
Bachmann's Rollmaschine für conische Röhren.
Die Anwendung der conischen Siederohre findet, nachdem die Zweckmäſsigkeit und
Nützlichkeit derselben erkannt worden ist, immer mehr statt. Dieselben finden nicht
allein Verwendung bei den Cornwall-Kesseln, wo die Feuerrohre durch die Anbringung
von Galloway-Röhren versteift werden, sondern es sind auch, nachdem die conischen
Rohre entstanden, besondere Kesselsysteme erdacht worden, bei welchen solche
Siederohre einen Haupttheil dieser Constructionen bilden.
Für Cornwall-Dampfkessel bilden diese Rohre nicht nur die beste
Verankerung der Feuerrohre gegen das Zusammendrücken derselben, sondern erfüllen
auch gleich den Zweck eines starken Wasserumlaufes von dem Unterkesselwasser nach
dem Oberkesselwasser. Dieser Umlauf ist von groſser Wichtigkeit zur Erzielung
schneller Dampfbildung und gleichmäſsiger Erhitzung des Kesselwassers. Die im
Cornwall-Kessel unterhalb der Feuerrohre befindliche Wassermenge wird durch die
Rohrverbindungen schneller erwärmt und in Dampf verwandelt, als dies ohne
Galloway-Rohre der Fall ist. Verfasser hat vielseitig Beobachtungen angestellt und
gefunden, daſs nach einer 3 bis 4stündigen Heizung des Cornwall-Kessels ohne
Galloway-Rohre das unter den Feuerrohren im Kessel befindliche Wasser noch lange
nicht den Siedepunkt erreicht hatte, als bereits das Oberkesselwasser Dampf von 4at lieferte. Diese Erscheinung ist auch leicht
erklärlich. Die im Unterkessel unter den Feuerrohren befindliche Wassermasse ist
eine sehr bedeutende. Die Feuerrohre sind nach dieser Seite hin mit Flugasche
bedeckt, welche bekanntlich die im Feuerrohre vorhandene Wärme nicht übertragen
kann, bezieh. solchen Vorgang nicht zuläſst, oder diesen höchstens nach mehreren
Stunden mangelhaft bewirkt. Die Oberflächen der Feuerrohre geben aber die Wärme an
das Oberwasser schnell ab und verwandeln dasselbe in Dampf. Hierbei findet ein
starker Wasserumlauf oberhalb der Feuerrohre statt, die sich aber nicht bis nach den
bedeutend tiefer liegenden Wassertheilen des Unterkessels erstrecken kann. Dazu
kommt noch, daſs bei den meisten Dampfkesselanlagen der Fehler begangen wird, daſs
das Speisewasser in den unteren Theil des Kessels, also des kalten Wasserraumes,
eingeführt wird, anstatt daſs man dasselbe oberhalb der Feuerrohre durch ein langes,
siebartiges, parallel mit der Kessellängsachse eingebrachtes Speiserohr
einführt.
Diesem Uebelstände wird aber durch Anbringung vieler
Galloway-Röhren in den Feuerungsrohren abgeholfen. Die Wärme wird durch diese Röhren
sehr schnell dem Wasser zugeführt und das specifisch leichter gewordene Wasser der
Röhren fängt an aufzusteigen. Hierdurch muſs die Nachströmung kälteren Wassers vom
Unterkessel erfolgen, und es wird so ein Umlauf gebildet, welcher im Stande ist, das
Unterwasser mit dem Oberwasser des Kessels in rascher Folge zu einer gleichmaſsigen
Erwärmung zu bringen.
Um nun einen mächtigen Wasserumlauf zu erreichen, ist wohl zu
beachten, daſs die Röhren in den Feuerrohren versetzt eingebracht werden. Hierbei
werden die Röhren
von der Flamme besser umspült, als wenn sie in verticaler Stellung hinter einander
angebracht sind.
Da es noch viele Dampfkesselbesitzer und junge Techniker gibt, die
mit der Nützlichkeit und Wichtigkeit der Verwendung der Galloway-Rohre nicht
vertraut sind, so wurde das bis jetzt Gesagte der eigentlichen Beschreibung der
Rollmaschine für solche Rohre und deren Fabrikation vorangeschickt. Es dürfte
hierdurch eine Hinweisung gegeben sein, wie man einen dauerhaften und sicheren
Dampfkessel mit ökonomischer Einrichtung hinsichtlich des Verbrauches von
Brennmaterialien erhalten kann.
Die vom Verfasser construirte und ausgeführte Maschine (Fig. 1 bis
8 Taf. 16) besteht aus einer Grundplatte A,
welche auf ihrer Oberfläche sehr sauber abgedreht sein muſs; dieselbe hat unterhalb
6 Rippen als Versteifung und in der Mitte eine Nabe zur Aufnahme der conisch
abgedrehten Stahlwelle B, welche conisch eingepaſst,
mit dem Keile P befestigt ist und einen aufgesetzten
Guſsmantel C (Hohlkegel) trägt. Das Aufsetzen des
Hohlkegels C hat den Zweck, auch auſsergewöhnliche
Gröſsen von conischen Rohren anfertigen zu können. Hierbei wird es alsdann
erforderlich, die Stahlachse E mit kleineren
Kegelscheiben zu besetzen. Die Normalgröſse der conischen Rohre (Siederohre) ist 750
bis 800mm Länge, 200mm lichte Weite oben und 100mm
unten.
Um den Kegel B dreht sich die Rollkurbel D mittels der Rollen O und
des Hebels N. In der Rollkurbel befindet sich die
Stahlwelle E die durch den Keil p befestigt ist. Der Scheibenkegel F sitzt
drehbar auf der Welle E. Die Scheiben haben einen
Zwischenraum von 3mm, damit die Reibung der ganzen
Scheibenfläche vermieden wird. Wird der Kegel F aus
einem Stücke hergestellt, so nimmt derselbe, wenn die Rollkurbel, auf welche er
befestigt ist, um die Achse B gedreht wird, eine
rollend schleifende Bewegung an, welche mehr Kraft erfordert. Da nun an den
berührenden Kegelflächen von C und F bei gleicher Geschwindigkeit der Umdrehung der
Rollkurbel D verschiedene Geschwindigkeiten eintreten,
so wird die Drehung eine leichtere, wenn der Kegel F
aus vielen Scheiben besteht, die unabhängig von einander sich auf der Achse E drehen können.
Die beiden Stahlachsen B und E haben am oberen Ende eine cylindrische Verlängerung, über welche Zapfen
ein Kuppeleisen G gelegt wird, um etwaiges
Auseinanderfedern zu verhindern. Dasselbe muſs sehr leicht aufgepaſst werden, damit
das Stück mit der Hand schnell auf- und abgelegt werden kann, wenn das gerollte Rohr
abgenommen werden soll.
Der Support H ist in Fig. 1 in
der Grundansicht, in Fig. 2 im
Durchschnitte und in Fig. 3 in
der Vorderansicht dargestellt. Die Supportplatte J ist
in Fig. 4 besonders angegeben. Der Support H
ist auf der Platte J befestigt, welche sich unter der
Rollkurbel D befindet und um die Kegelachse B drehen läſst, mithin auch der Support H. An der Schraube K
befindet sich der Schlüssel L und das Klemmeisen M, welches nach der Kegelfläche C ausgearbeitet und derselben angepaſst ist. N ist ein von beiden Seiten des Supportes angebrachtes starkes
Führungsstück, welches das Klemmeisen M genau in der
Verticalachse des Kegels erhält, sowie auch eine Drehung desselben beim Walzen der
Bleche verhindert. Die Löcher Q in der Grundplatte A (Fig. 1)
dienen dazu, ein Drehen bezieh. Mitnehmen des Supportes H beim Walzen zu verhindern. In die Löcher Q
wird ein Kopfbolzen R gesteckt, wogegen der Support H mit der Platte J
ruht.
Was nun die Anwendung dieser Maschine zur Herstellung conischer Siederohre betrifft,
so gibt hierüber das Folgende Aufschluſs. Die Platten (aus Low-Moor-Bisenblech)
erhalten die Form Fig. 5. An
den Längskanten werden die Platten mit einem Kehlhammer einmal an der linken und
einmal an der rechten Seite abgeschärft, wobei zu beobachten ist, daſs die
Abschärfungen bei der Walzung der Bleche richtig auf einander fassen (vgl. Fig.
8). Nachdem sämmtliche Bleche für die Schweiſsung abgeschärft worden sind,
werden die Bleche in einem Glühofen hellroth erwärmt. Jede zu walzende bezieh. zu
rollende Platte wird an der Seite mit äuſserer Abschärfung über den Kegel Fig.
7 etwas gekrümmt, um solche anliegend am Kegel C zwischen beide Walzen zu schieben, wie die punktirten Linien in Fig.
1 angeben. Durch Andrehen des Schlüssels L
drückt die Schraube K das Klemmeisen M gegen die Platte und den Kegel und wird so
festgehalten. Die Maschine, welche vorher in die Stellung der punktirten Linie y gebracht wurde, wird nunmehr in der Richtung des
Pfeiles gedreht, wobei die Walze F die Platte um den
Kegel C wickelt. Wenn die Walze F bis zur anderen Seite des Supportes H
gelangt ist, wird das Klemmeisen gelöst, der Bolzen R
(Fig. 1) aus der Platte A gehoben und in der
Richtung des Pfeiles um ein Loch weiter gestellt, der Support vorgeschoben und das
Klemmeisen M wieder festgestellt. Durch diese
Umstellung des Supportes, welche nur die Arbeit eines Augenblickes ist, hat man Raum
gewonnen, die abgeschärften Nähte fest auf einander zu walzen.
Nachdem nun das Rohr gewalzt ist, erfolgt die Abnahme desselben vom Kegel C. Hierzu wird das Kuppeleisen G abgehoben. Oberhalb des Kegels C in
entsprechender Höhe ist eine Kette mit Rolle angebracht, an welcher ersteren eine
Zange zum Abheben des Rohres angebracht ist. Damit nun das Rohr am oberen Ende
gefaſst werden kann, wird dasselbe mit einem kleinen scharfen Hebeisen (Brechstange)
von der Rollkurbel aus in die Höhe gehoben, die Zange aufgesetzt und mit Rolle und
Kette in die Höhe gezogen, was mit der gröſsten Leichtigkeit ausgeführt wird. Das
Gewicht der Normalrohre beträgt 30k. Die Rohre
sind beim Abheben noch so warm, daſs einzelne Stellen der Naht mit dem Hammer über
den Kegel Fig. 7
angetrieben werden können, was um so mehr erforderlich ist, als die innere Naht
allenthalben dicht und fest auf der Gegenwand des Rohres liegen muſs.
Nachdem sämmtliche Rohre in der beschriebenen Weise vorbereitet sind, kann mit dem
Schweiſsen der Nähte begonnen werden. Zu diesem Zwecke bedient man sich eines
freistehenden Rundschmiedefeuers mit länglicher Düsenöffnung (Feuerarm), aus besten
feuerfesten Steinen hergestellt. Die Oeffnung oder der Feuerraum hat eine Länge von
450mm bei 120mm Breite; dieser Raum wird mit Kokes ausgefüllt und mit feinen, nassen
Schmiedekohlen die vorgenannte Oeffnung um 300mm
Höhe erhöht und eingebaut. Auf diesem so hergerichteten Feuer geschieht die
Nahtschweiſsung in 10 Absätzen von der Mitte des Rohres ausgehend. Im Innern des
Rohres werden gebrannte Thonstücke auf die zu schweiſsende Nahtstelle gelegt, um
während der Bildung der Schweiſshitze die Luft abzuhalten, indem nur von der
äuſseren Seite des Rohres die Schweiſsung erfolgen kann. Ist die Schweifshitze
eingetreten, so erfolgt die Aushämmerung auf den maſsiven Halbkegel Figur 6. Der
Halbkegel bietet nach unten Raum für die Schmiedezange und ist zu diesem Zwecke auf
ein schweres Guſsstück mit dem dickeren Theile so festgeschraubt, daſs der dünnere
Theil in horizontaler Lage genügend lang hervortritt, um das zu schweiſsende Rohr in
ganzer Länge aufschieben zu können.
Nachdem nun sämmtliche Rohre geschweiſst sind, werden sie gerichtet, indem bei der
Schweiſsung eine etwas flache und geworfene Fläche entstanden ist. Die Rohre werden
im Glühofen erwärmt und auf den Kegel Fig. 7,
welcher in horizontale Lage gebracht worden ist und auch gedreht werden muſs,
aufgetrieben und mit Holzhämmern gerundet, bis sie allenthalben anliegen. Der Kegel
zum Runden der Rohre ist abgedreht und hat eine saubere, glatte Fläche, wodurch die
Rohre auch eine saubere und genaue Form erhalten müssen. Hierauf beginnt die
Börtelung der Rohre, welche in einer Holzkohlenfeuerung, welche weniger zundert,
ausgeführt wird. Das Austreiben der Flanschen wird mit Holzhämmern vorgenommen und
die Stellung der Flanschen durch eine Lehre erlangt.
Zur Anfertigung der Galloway-Rohre gehören 3 Personen, ein Schmied und zwei Gehilfen.
Die Leute müssen gewandt und flink sein, da Blechschweiſsungen mit der ersten Hitze
stets gelingen müssen. Eine Schweifsnaht darf bei sauber gerundeten Rohren weder
innen noch auſsen sichtbar sein. (Nach dem Praktischen
Maschinenconstructeur, 1879 S. 296.)
Tafeln
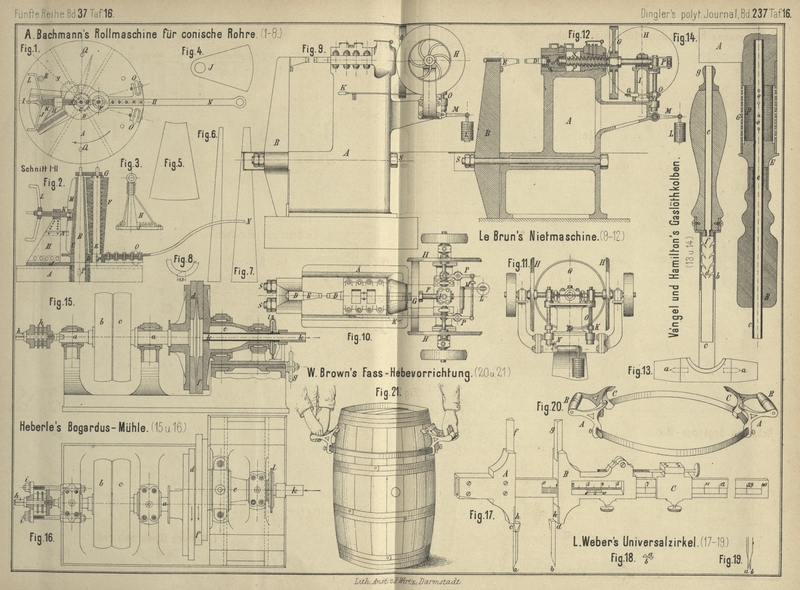