Titel: | Ueber die Fabrikation von Cementröhren am Salzberg Ischl; von Oberbergverwalter A. Aigner. |
Autor: | Aug. Aigner |
Fundstelle: | Band 220, Jahrgang 1876, Nr. , S. 506 |
Download: | XML |
Ueber die Fabrikation von
Cementröhren am Salzberg Ischl; von Oberbergverwalter A.
Aigner.
Mit Abbildungen auf Taf. IX [a.c/1].
Aigner, über die Fabrikation von Cementröhren
am Salzberg Ischl.
Die fabriksmäßige Erzeugung von Cementröhren unter Anwendung von
Wasserkraft am Salzberg bei Ischl wurde bereits in diesem
Journal, * 1875 215 423, mitgetheilt;
nachdem diese Fabrikation nunmehr im vollen Gange ist und seit
jenem Zeitpunkte einige wesentliche Verbesserungen darin
eingeleitet wurden, so dürfte deren Veröffentlichung als Folge
der damals angegebenen Motive ihre Berechtigung finden. Unter
Hinweisung auf die bereits gegebene Beschreibung der Sandwasch-
und Mörtelrührapparate soll mit Hilfe der Figuren
13 bis 30 (nach
dem Berg- und hüttenmännischen Jahrbuch, 1876 S. 1) die
gegenwärtige Einrichtung geschildert werden. Die
Zusammenstellung derselben zeigen Figur 16
im Grundriß, Figur 13
im Verticalschnitt nach I II, Figur 15 im Querschnitt III
IV von links und Figur 14
von rechts angesehen.
Es bedeuten darin A das Wasserrad,
n das Wasserfluder, w (Fig. 14
und 15) einen
Hebel zur Regulirung des Aufschlagwassers, D eine Trommel auf der Wasserradwelle,
b (Fig. 14)
die Riemenumsetzung und k, l die
conischen Getriebräder für den Mörtelrührapparat m; Z′
ist die Wasserzuleitung für die Sandwäsche s und den Rührapparat m, dessen Achse h in den fixen Halslagern i
läuft und sich mittels des Hebels 4 heben und senken läßt, so
daß durch die Hebung die Schaufeln des Rührapparates über den
Trog m hinausragen. Durch den Hebel
5 erfolgt die Auslösung des Rührapparates und zwar durch Hebung
der Zugstange d, wobei die Stange
b′, an welcher der Träger c des Rades k befestigt ist, dieses Kegelrad k senkt und außer Eingriff mit dem Triebrad l bringt. Oberhalb dem untern Lager i ist die Achse h mit einem Bund versehen, durch welchen deren genaue
Höhenstellung erzielt wird, da die Schaufeln des Rührapparates
sich knapp an dem mit Eisenblech beschlagenen Boden und den
Seitenwänden des Troges m bewegen.
Ueber dem Bund besitzt die Achse der Länge nach eine Nuth, so
daß sich das Zahnrad k, welches in
seiner Nabe mit einem Keil versehen ist, auf der Achse nicht
drehen läßt, jedoch nach oben und unten leicht verschiebbar ist.
Soll der gemischte Mörtel aus dem Rührapparat gezogen werden, so
wird das Kegelrad k ausgerückt und
hierauf die Achse h mittels des
Hebels 4 gehoben. Es kann nun das Waschen des Sandes in dem
Apparate s ohne Störung vor sich
gehen, da hierbei nur das Kegelrad l
leer läuft.
Ferner ist f (Fig. 16)
die Riemenscheibe für die Sandwäsche s und s′ (Fig.
14) der Hebel zur Hebung des Sandwaschkorbes; g (Fig. 16)
der Riemen für die Transmissionsachse a, um die Bewegung auf die Aufzugsmaschine das
Röhrenmodelles mittels der Riemenscheibe t zu übertragen.
Die Gußform e (Fig. 13
und 14) für
die Röhren besteht im Gegensatze zu der früher beschriebenen
hölzernen und horizontal liegenden Form aus starkem Eisenblech
und steht vertical. Es liegt hierin
eine wesentliche Verbesserung, nachdem die Holzmodelle durch
Anziehen von Feuchtigkeit sehr häufig eine Zerklüftung der
Röhren herbeiführten, welche sich immer nach ihrer Längsachse
zeigte. Durch die verticale Stellung des Modelles wird überdies
das gegossene Material compacter.
Die Aufzugsmaschine dient zum Einlassen des Röhrenmodelles unter
die Schnauze des Rührapparates in den Schacht S und zur Hebung desselben. Ihre
Construction ist aus Figur 13,
14 und in vergrößerter Ansicht aus Figur 26
zu ersehen. Der Antrieb erfolgt von der Zwischenwelle a auf die Riemenscheibe t, auf deren Achse das Getriebe v (14 Zähne) sitzt; dieses greift in das
Zahnrad u (36 Zähne), und ein
Spindelrad (9 Spindeln) an der Achse des letztern in das Kammrad
2 (36 Kämme), dessen Achse endlich mittels eines Spindelrades
(mit 6 Spindeln) die Zahnstange Z
hebt oder senkt, mit welcher die Wagenbühne R (Fig. 13)
verbunden ist. Die genaue Einstellung von R geschieht zuletzt mittels Handrad p und Ledergurte y.
Figur 23 zeigt den Hebeapparat für die Gußform; derselbe
besteht aus dem Hebel M mit Zugseil,
welcher um die Achse B horizontal
und vertical gedreht werden kann; einem Gestelle mit vier Säulen
Q, zwischen welche der Wagen W eingeschoben werden kann. Mittels des
Hebels M läßt sich das Modell auf
den Wagen oder davon herab heben, indem man die vier eisernen
Tragschienen H, welche unten in
Haken auslaufen, unter das Bodenbret des Modelles einhängt. Soll
nun die Arbeit beginnen, so wird das gereinigte Modell sammt
Wagen auf die Bühne R (Fig.
13) geschoben und mittels der Aufzugmaschine in den
Schacht S gesenkt; hierauf bringt
man gleiche Volumtheile Sand und hydraulischen Kalk mit Wasser
(in folgenden Gewichtsverhältnissen: 36k
hydraulischen Kalk, 57k gewaschenen Sand, 18k
Wasser) in den Rührapparat. Der Kalk und Sand werden zuerst
trocken gemengt und das Wasser nach Bedürfniß hinzugefügt; die
ganze Mischung dauert 8 Minuten, worauf die ganze Masse durch
die Schnauze mittels einer Krücke in die Form gezogen, letztere
aus dem Schachte S gehoben, mit dem
Wagen W (Fig. 23)
zum vorläufigen Trockenplatz gebracht und mittels einer
Hebemaschine herabgestellt wird, wobei man die Formen
paarweise an einander reiht.
Mittels eines kammförmigen Werkzeuges werden aus dem obersten
Theile der gefüllten Form die Luftblasen entfernt und hierauf
das Stoßbret (s. unten), der fortschreitenden Erhärtung
entsprechend, durch geringen Druck allmälig angetrieben. In
diesem Zustand müssen die Kolben (gußeiserne Kerne, welche die
Höhlung des Rohres ausfüllen) öfters gedreht werden, was durch
einen Zeitraum von 8 Stunden nach jeder halben Stunde erfolgt,
worauf die Kolben durch einen an der Decke des ersten
Stockwerkes eingehängten Flaschenzug ausgezogen werden.
Man läßt die Formen nun 24 Stunden stehen, nimmt sodann die zwei
Modelltheile hinweg und läßt die entblößten Röhren auf dem
Bodenbrete noch 48 bis 60 Stunden frei stehen. Nach dieser Zeit
sind dieselben transportabel, zu welchem Behufe sie aus der
verticalen in die horizontale Lage gebracht werden müssen.
Dieses geschieht mittels des in Figur 27
abgebildeten Apparates; hier sind v,
v′ zwei an die Cementröhre angelegte verticale
hölzerne Breter, welche unter der Röhre auf das Bodenbret P der Form aufgestellt werden, wobei die
Haken h, h′ unter das
Bodenbret hineinragen; von diesen Haken ist h′ fix, h beweglich und oben umgebogen, so daß eine äußere Stange
y durchgezogen werden kann; diese
Stange, sowie ein bei x befestigter
Handgriff dienen zur Hebung des Ganzen. Die Cementröhre wird nun
sammt dem Bodenbrete mit den beiden Handhaben von zwei Arbeitern
gehoben und auf den Schemel Figur 30,
an dessen Oberfläche sich entsprechende Vertiefungen befinden,
so aufgelegt, daß das Bret v nach
unten kommt. Nun wird die bewegliche Eisenschiene w herausgezogen und die Röhre sammt dem
Unterlagsbret v (von solchen Bretern
muß ein großer Vorrath vorhanden sein) vorläufig in den
Trockenraum mittels einer Hebemaschine aufgezogen; hier werden
die Röhren durch einen Zeitraum von 8 Tagen auf dem Bodenbrete
vorgetrocknet, worauf sie mit der Aufzugsmaschine wieder gesenkt
und auf den eigentlichen Trockenplatz getragen werden.
Dieser ist vollkommen horizontal und besteht aus parallelen
Gassen. Jede solche Gasse hat einen Unterbau aus zwei der Länge
der Gasse parallel laufenden Grundpfosten, auf welchen 50mm
starke Bodenbreter quer aufgenagelt sind; auf diese kommen die
Röhren zu liegen. Ist der Boden mit der ersten Reihe von Röhren
belegt, so wird darüber eine zweite, dritte und vierte Reihe
geschichtet und zwischen den Röhren feiner Sand (Abfälle des
Sandwaschapparates) gestreut. Die Einwirkung der Luft
(Kohlensäure) und der Regen ist für die Röhren vortheilhaft und
macht sie allmälig fester. Erst zu Anfang des Winters müssen
diese Röhrenlagen mit beweglichen Dächern versehen werden.
Was die Röhrenform betrifft, so ist
dieselbe durch die Figuren
24 und 25 im
Auf- und Grundriß näher dargestellt. Sie besteht aus einem
Bodenbret und eisernen Seitenwänden; das Bodenbret, welches die
Figuren 21 und 22 in
vergrößertem Maßstab zeigen, ist von Holz und rings um die
mittlere Oeffnung b c mit Eisenblech
beschlagen, um für den gußeisernen Kern eine feste Unterlage zu
bilden. Auf dem Bodenbret befindet sich ein hölzerner Aufsatz
von der Gestalt des später beschriebenen Stoßbretes. Nachdem der
Kolben gereinigt ist, werden die innern Flächen der Wände mit
Maschinenöl geschmiert, bei x y
(Fig. 21)
eine Lettenwulst umgelegt und die Seitenwände der Form in diese
Wulst hineingesenkt. Diese Wände (Fig. 24
und 25)
bilden ein achteckiges Prisma von Eisenblech, dessen beide
Hälften sich an der Berührungsstelle übergreifen und durch je
zwei oder drei Haken α, β zusammen gehalten
werden; nachdem dieselben zusammen gefügt sind, werden sie durch
die Haken α, β verbunden und oben der eiserne Ring
r angezogen.
Der Kern (Fig. 28
und 29) ist
aus Gußeisen gefertigt und besteht aus einer Röhre von 6mm,5
Fleischstärke; er ist genau abgedreht und schwach conisch
geformt. Oben ist in zwei gegenüber stehenden Oeffnungen
desselben ein rundes Holzstück eingesetzt, mit einer Bohrung
versehen, in welche eine zum Anfassen dienende Eisenstange p eingezogen werden kann. Der Kolben
wird ebenfalls geölt und in das Modell (Fig. 24)
eingeschoben, wobei seine verticale Stellung durch die eiserne
Führung r′ erhalten ist,
welche auf den obern Rand der Form aufgestellt wird. In dieser
Stellung wird nun der Mörtel eingeführt.
Das Stoßbret (Fig. 19
und 20)
besteht aus Holz und ist mit einem eisernen Ring versehen.
Nachdem die gefüllte Form mittels einer Hebemaschine auf den
Trockenplatz gestellt wurde, schiebt man das gereinigte und
geölte Stoßbret in umgekehrter Stellung über den Kolben und
treibt dasselbe durch öfteres leises Beklopfen gegen den obern
Theil des Cementrohres.
Brüche von Röhren kommen selten vor;
man kann sie auf 1 bis 2 Proc. veranschlagen; während dieselben
nach der frühern Methode mit Holzformen stets in der
Längenrichtung der Form erfolgten, kommen sie bei verticalem
Guße ausschließlich nur nach der Quere der Röhre vor, und dies
macht die Wiederherstellung jeder gebrochenen Röhre leicht
möglich. Es werden zu diesem Zwecke die beiden gebrochenen Theile
auf einen Schemel gebracht, so daß der Zusammenstoß derselben
über eine Aushöhlung in dem Schemel zu liegen kommt, sodann
durch die Röhrenstücke ein Kolben eingeführt und von außen eine
kurze aus zwei Theilen bestehende Form angelegt, welche oben
eine Oeffnung zum Eingießen des Cementes besitzt. Man verwendet
dazu ⅔ Th. Portlandcement auf ⅓ Th. hydraulischen
Kalk zu gleichen Theilen mit feinem Sand; die Trocknung erfolgt
dabei etwas schneller, und die Röhren sind vollkommen fest.
Schadhafte Stellen, welche an dem Ende der Röhre vorkommen
können, werden auf gleiche Weise ausgebessert. Zu diesem Ende
erhalten die Außentheile des Stoßbretes (Fig. 19
und 20)
160mm lange Blechwände, welche an ihren Kanten nicht
zusammen hängen, um sie dem Cementrohre besser anpassen zu
können. Das Stoßbret wird nun mit diesen Wänden mittels einer
Schraubenzwinge an das Rohrende befestigt und hierauf das
Vergußmaterial oben eingeführt.
Was das Legen der Röhren betrifft, so
wurde früher bereits eine Methode der Verbindung angegeben,
welche im Allgemeinen befriedigende Resultate gibt; es können
jedoch auf ausgedehnte Strecken, wo stellenweise nicht
vollkommen standhafter Grund vorhanden ist, in einer starren
Röhrentour Zerklüftungen entstehen. Eine seit vielen Jahren am
Salzberg in Ischl gelegte eiserne Röhrentour war nun mit einem
Kitt von ungelöschtem Kalk und Steinkohlentheer an einander
gefügt worden; dieser Kitt, welcher außen erstarrt, bleibt nach
Jahren in der Mitte zähflüssig und gestattet dem schiebenden
Boden (Haselgebirge) eine nicht unbedeutende Bewegung der
Röhren. Diese Beobachtung führte auf folgende Verbindungsart der
Cementröhren.
Die zu verbindenden Röhren werden zuerst horizontal in dem 712mm
tiefen Graben an einander gereiht und festgelegt, hierauf eine
mit der obigen zähflüssigen Masse geschmierte Schnur in den
keilförmigen Zwischenraum ε (Fig. 17
und 18) der
Röhren gewickelt und der Reihe nach mit immer dickern alten
Stricktheilen, endlich mit Hanfsträngen umwunden und dabei
fortwährend Kitt eingetragen. Ueber den am Umfang entstehenden
Wulst wird endlich ein eiserner Ring γ mit der Schraube
δ angezogen und ein Blechstreifen p zur bessern Vertheilung des Druckes eingelegt.
Ueber die Festigkeit der Röhren läßt
sich Folgendes angeben. Ein Jahr alte Röhren haben einen Druck
von 3at ausgehalten; nachdem ein höherer Druck aus Mangel
einer entsprechenden Einrichtung nicht erzielt werden konnte und
neue Röhren durch längeres Liegen an Festigkeit zunahmen, so
kann diese Zahl nicht als Maximum angesehen werden.
Die Kosten der Herstellung eines 1m,16
langen Rohres, von 65mm,5 Fleischstärke und 131mm
lichtem Durchmesser stellen sich, wie folgt:
0,6
Metzen
=
36k
hydraulischer Kalk
39,31
kr.
ö.
W.
0,6
Metzen
=
57k
Sand
10,70
kr.
ö.
W.
18k
Wasser
—
kr.
ö.
W.
Oel zum Modellschmieren
2,30
kr.
ö.
W.
Arbeit
26,00
kr.
ö.
W.
––––––––––––––––––––
78,31
kr.
ö.
W.,
also pro laufenden Meter loco Fabrik nahe
68 kr. ö. W.
Tafeln
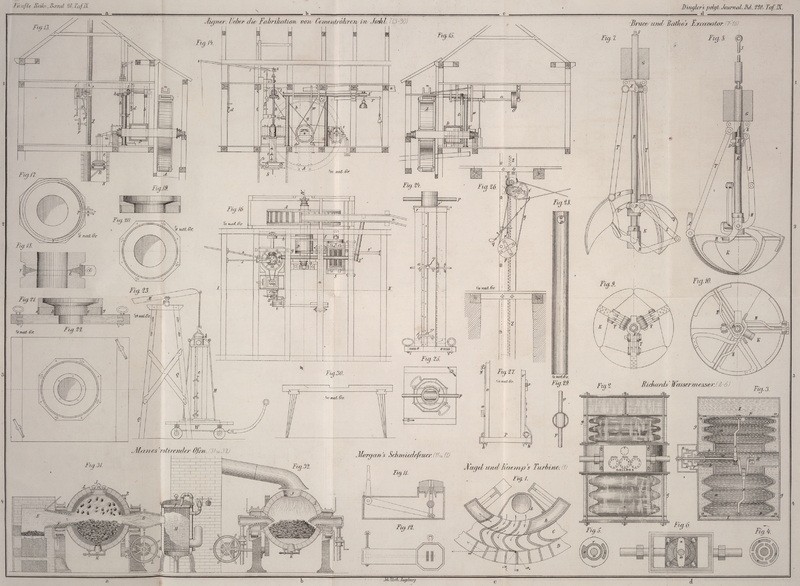