Titel: | Ueber Jones und Walsh' Verfahren zur Sulfatfabrikation; von Professor Dr. Georg Lunge in Zürich. |
Autor: | Georg Lunge [GND] |
Fundstelle: | Band 220, Jahrgang 1876, Nr. , S. 233 |
Download: | XML |
Ueber Jones und
Walsh' Verfahren zur Sulfatfabrikation; von Professor
Dr. Georg
Lunge in Zürich.
Mit Abbildungen auf Taf. IV [c/3].
Lunge, über Jones und Walsh' Verfahren zur
Sulfatfabrikation.
Erst vor Kurzem habe ich in diesem Journale (*1875 218 416) eine ausführliche Beschreibung des schon längst
bekannten Apparates von Hargreaves
zur Fabrikation von Sulfat (Glaubersalz) nach seiner neuen
Methode gegeben, und schon bin ich wiederum in der Lage über ein
Verfahren zu berichten, welches einen so enormen Fortschritt in
der Fabrikation desselben Artikels aus Kochsalz und
Schwefelsäure darstellt, daß vermuthlich das Uebergewicht der
Vortheile, welches eine Zeit lang sich auf Hargreaves' Verfahren
zu neigen schien, wieder ganz und gar der ältern Methode
zufallen wird.
Wie allbekannt, wird in allen größern Fabriken das Kochsalz mit
Schwefelsäure von 55 bis 60° B. in großen gußeisernen
Schalen erhitzt, und wenn die Masse bis zur dicken
Breiconsistenz concentrirt ist, wird sie nach dem Calcinirofen
hinübergeschafft, um dort fertig gemacht zu werden. Dies
erfordert namentlich für die erste Arbeit (in der Schale) sehr
tüchtige und zuverlässige Arbeiter; es ist ungemein schwierig,
ausgenommen nach langer Uebung und mit großer Umsicht, die
Schalen richtig zu behandeln; sie müssen selbstredend sehr dick
sein (bis 178mm am Boden), und obwohl sie nur aus den besten und
zähesten Roheisensorten gegossen werden (es ist dies eine
Specialität weniger Gießereien), so geschieht es doch häufig,
daß sie schon nach wenigen Wochen, in Folge des häufigen starken
Temperaturwechsels, springen und mit großen Kosten ausgewechselt
werden müssen. Selbst ganz abgesehen von Unfällen oder grober
Vernachlässigung hält eine Schale nur selten für mehr als 1500
bis 2000t Sulfat aus, und viele Fabrikanten rechnen nur auf
einen Durchschnitt von 1200t. Man sucht die Arbeiter durch
specielle Prämien nach Ueberstehung einer gewissen Arbeitszeit
einer Pfanne zu größerer Behutsamkeit mit denselben zu
ermuntern, aber über den obigen Erfolg kommt man doch nicht
hinaus, und man ist zudem von dem guten Willen der Arbeiter sehr
abhängig, welche recht gut wissen, daß es unmöglich ist, neue
Leute ohne enormes Risico für die Schalen Plötzlich anlernen zu
müssen.
Auch die Ofenarbeit hat ihre große Schwierigkeiten; fast überall
werden die Leute sehr durch Salzsäuregas belästigt, weil man, um
eine gute Condensation zu erreichen, nicht zu starken Zug geben
kann; um starkes Sulfat zu erhalten, muß man einen Ueberschuß
von Schwefelsäure anwenden, weil die Mischung von den Arbeitern
nie vollkommen gemacht wird, und diesen Ueberschuß muß man
wieder großentheils verdampfen. Obwohl die für Herstellung von
Natriumsulfat aus Kochsalz und Schwefelsäure erforderliche
Hitze, incl. der zur Vertreibung der Salzsäure etc.
erforderlichen, verhältnißmäßig nicht bedeutend ist, so
consumiren doch sowohl die Schale als der Ofen ganz
unverhältnißmäßig große Mengen von Brennmaterial.
Der Ofen von Jones und Walsh, welcher im Folgenden beschrieben
werden soll, stellt so gut wie alle gerügten Uebelstände ab und
läßt in der That, so weit ich es jetzt beurtheilen kann, dem
Praktiker fast gar nichts zu wünschen übrig. Freilich ist die
mit demselben gewonnene Erfahrung erst einige Monate alt, aber
es ist kaum anzunehmen, daß etwaige Uebelstände in dieser Zeit
noch nicht zu Tage gekommen sein sollten. Die erste Erwähnung
dieses Ofens in der Oeffentlichkeit ist von Pattinson in seiner Eröffnungsrede vor
der Newcastle Chemical Society
gemacht worden; seitdem wurde aber der Ofen bedeutend
verbessert, und ich werde ihn und das Verfahren beschreiben, wie
ich sie Anfangs Februar d. I. in einer größern Gesellschaft von
chemischen Fabrikanten an Ort und Stelle (in Middlesborough)
gesehen und untersucht habe.
Der Ofen besteht aus einer kreisförmigen Schale, 14 engl. Fuß
(4m,27) weit, mit flachem Boden und 6 Zoll (152mm)
aufstehendem Rand, welche auf massivem Mauerwerk ruht und
ausschließlich von oben durch ein Kokesfeuer erhitzt wird. In
der Mitte der Schale ist ein Zapfenlager, in welchem eine
stehende Welle rotirt, die durch das die Schale überspannende
Gewölbe nach oben austritt und durch ein Zahnradvorgelege in
Bewegung versetzt wird; in der stehenden Welle sind
Vorrichtungen angebracht, durch welche die in der Schale
befindliche Mischung fortwährend umgerührt und schließlich
entleert wird. Die Operation wird an
derselben Schale bis ganz zu Ende geführt und existirt kein
besonderer Calcinirofen. Im Folgenden die nähere
Beschreibung des in Fig. 27
bis 29
dargestellten Ofens.
a ist der Feuerherd, wie man sieht,
verhältnißmäßig sehr klein; das Feuer streicht durch die Füchse
b über die flache Schale c und entweicht durch d in den Abzugscanal e, welcher nach den
Condensationsvorrichtungen führt. In der Mitte der Schale rotirt
eine stehende Welle f (von Gußeisen)
in einem Zapfenlager g; von ihr
gehen vier starke, horizontale, schmiedeiserne Arme h aus, an welchen die schräg
vorstehenden Stangen i mit den daran
befestigten Pflügen k durch
Vorstecker befestigt sind. Die Pflüge sind in ungleichen
Abständen von der Welle angebracht, so daß die ganze Schale von
ihnen bestrichen wird. Die Pflugschaaren K sind die einzigen Eisentheile, welche irgend größerer
Abnützung ausgesetzt sind; aber dies beträgt nur ein
unbedeutendes gegenüber der Abnützung der gewöhnlichen Gezähe,
welche hier ganz fortfallen, und sie können sehr leicht und
schnell ausgewechselt werden. Die Welle h wird durch das Zahnradvorgelege l in Umdrehung versetzt und die bewegende Kraft durch eine
Riemenscheibe von einer beliebigen Welle oder einer besondern
kleinen Dampfmaschine (etwa 125mm-Cylinder) abgeleitet. Die
Oeffnungen m, welche in der Regel
durch die Thüren n verschlossen
sind, dienen zum Eintragen und Ausziehen der Charge.
Diese Construction ist in mehrfacher Beziehung der Verbesserung
fähig, und die neuen Ofen werden jetzt nach den Plänen von
Alfred Goodman in Newcastle
ausgeführt. Der Feuerherd wird, statt an die Stirnseite, an
eines der Widerlager des Schalengewölbes gelegt, was gestattet,
das letztere viel niedriger zu halten und dadurch die Feuerung
besser auszunützen. Die Schale wird, statt 14 Fuß (4m,27)
jetzt 16 Fuß (4m,88) weit gemacht und steht auf
einem Gewölbe, und die Welle wird von unten her in Betrieb
gesetzt. Die Pflüge sind von Gußeisen, direct an die
horizontalen Arme angesetzt und derart schief gestellt, daß sie
unter gewöhnlichen Umständen den Inhalt der Schale einfach
umrühren und mischen, aber beim Umstellen der Transmission den
Schaleninhalt nach der Peripherie bewegen und durch eine dort
angebrachte Entleerungsthür ausstürzen. Auf dem Deckgewölbe
sitzt ein eiserner Rumpf, unten verschlossen durch einen mit
Kette und Gegengewicht balancirten Conus, welcher die ganze
Charge (5t Salz) faßt und durch Lüften des Conus auf einmal in
die Schalen stürzt. Diese Einrichtung wird sowohl das Beschicken
als das Entleeren der Schale auf mechanischem Wege in der
kürzesten Zeit und mit einem Minimum von Handarbeit verrichten
und noch weniger Brennmaterial als bisher beanspruchen. Es
scheint kaum fraglich zu sein, daß eine Schale von 4m,88
Durchmesser alle 6 Stunden zu 5t Salz verarbeiten wird, also 20t
täglich. Dies ist jedoch bisher noch nicht in praktischem
Betrieb, und beziehen sich die nachfolgenden Angaben auf die
etwas weniger günstigen Resultate, welche Verfasser mit dem hier
abgebildeten, noch nicht verbesserten Apparate erhalten sah.
Die in den jetzigen (4m,27 messenden) Pfannen
verarbeiteten Chargen sind je 3t,5 Kochsalz resp. Chlorkalium (in
Jones' Fabrik wird der Apparat
meistens zur Fabrikation von schwefelsaurem Kali gebraucht). Das
Salz wird vorläufig noch mit der Hand eingeschaufelt, wie es bei
dem Betriebe der Welle von oben nicht gut anders möglich ist,
und dieses dauert bei der großen Charge beinahe 1 Stunde, ein
Verlust an Zeit und natürlich an Kohlen, welcher bei der neuen
Construction, mit Beschickung von oben, vollkommen vermieden
werden wird; dasselbe kann von dem Entleeren gesagt werden. Man
läßt dann etwa vier Fünftel der nöthigen Säure zulaufen, was
durch zwei gerade über dem Rande der Schale einmündende
Bleiröhren geschieht, und findet, daß die Säure sich mit dem
Salze ganz regelmäßig und ohne die mindeste Neigung zum
Ueberkochen mischt. Bei den gewöhnlichen, von unten geheizten
Pfannen findet bekanntlich ein solches Ueberkochen sehr leicht
statt, und die Arbeiter müssen ganz regelmäßig ein Stück Talg o.
dgl. in die Pfanne werfen, um es zu dämpfen, nicht immer mit
Erfolg; das Salzsäuregas entwickelt sich ganz stürmisch und
nimmt die Condensationsvorrichtungen in der ersten Viertelstunde
viel mehr als später in Anspruch. Bei Jones und Walsh' Apparat
dagegen ist die Gasentwicklung viel gleichmäßiger und die
Condensation darum leicht und vollständig, trotz der Verdünnung
mit Luft. Nachdem die Masse eine Viertelstunde lang umgerührt
worden ist, wird eine Probe herausgenommen und je nach Befund
derselben im Laboratorium der Rest der Schwefelsäure zugesetzt.
Sollte man zufällig zu weit darin gegangen sein, so kann man ein
weniges Salz zufügen u. s. f. Gerade diese Möglichkeit, eine
Charge während der Arbeit verbessern zu können, macht einen der
Vorzüge des Verfahrens aus. In Folge der innigen Mischung
braucht man auch nicht so viel Schwefelsäure (ca. 5 Proc.
weniger) als bei dem gewöhnlichen Verfahren. Die Hitze in dem
Ofen ist nur etwa 425° gegenüber 650° oder mehr in
dem gewöhnlichen Flammofen.
Nach 5½ oder 6 Stunden ist die Operation beendigt und das
Sulfat wird ausgezogen. Es erscheint als eine ganz feinpulverige
Masse, völlig frei von Klumpen und von großer Reinheit. Von zwei
Mustern, welche ich an Ort und Stelle entnahm und zu Hause
probirte, zeigte das eine (schwefelsaures Kali) 0,6 Proc. freie
Säure und 0,58 Proc. K Cl, das
andere (schwefelsaures Natron) 0,2 Proc. freie Säure und 0,12
Proc. Na Cl. Ein Sodafabrikant,
welcher 200t des bei Jones
fabricirten Sulfates zu Soda verarbeitet hatte, versichert mich,
daß es sich ganz ausgezeichnet gut verarbeitet und ungewöhnlich
starke Soda geliefert habe.
Zur Feuerung dienten Kokes, wovon 1¼ Ctr. pro Stunde
gebraucht werden. Dies beträgt 30 Ctr. für den Tag, was schon
bei der jetzigen Production nur ⅓ bis ¼ des bei
dem gewöhnlichen Verfahren in der Pfanne und im Ofen
verbrauchten Brennmaterials ausmacht. Neuerdings, auch während
meiner Anwesenheit, wird halb Kokes und halb Steinkohlen
gefeuert, ohne anscheinend der Salzsäure zu schaden, was wohl
von der bald zu erwähnenden „Douche“
herrühren mag.
Ein Arbeiter kann mit größter Leichtigkeit drei Oefen bedienen
und in der langen Zwischenzeit, während die Maschinerie
arbeitet, das Salz von Magazin herkarren, um es durch ein
Becherwerk in den Füllrumpf heben zu lassen; vorläufig geht das
eben nicht an, und er muß müßig gehen. Bei dem gewöhnlichen
Verfahren würden zwei Mann an der Pfanne, zwei oder selbst vier
am Ofen, ein Mann zum Wiegen und einer zum Wegkarren
erforderlich sein, um 15 bis 20t pro Tag zu verarbeiten.
Ein sehr wichtiger Gegenstand bleibt noch zur Betrachtung übrig,
nämlich die Condensation der Salzsäure. Es scheint allen
gewöhnlichen Regeln und Erfahrungen zu widersprechen, daß man
bei der Fabrikation des Sulfates mit ausschließlichem Oberfeuer starke Säure, und zwar ohne
irgend wie complicirte Condensationseinrichtung gewinnen könne,
und doch ist dieses der Fall, wie ich mich genau überzeugt habe.
Die
Möglichkeit davon wird augenscheinlich durch zwei Umstände
gegeben — einmal, daß die Entwicklung des Salzsäuregases
lange nicht so stürmisch im ersten und so langsam im letzten
Stadium geschieht, wie dies bei dem gewöhnlichen Verfahren mit
Pfanne und Ofen der Fall ist, und zweitens, daß die Hitze in
Jones' Apparat, wie oben bemerkt, weit geringer als im
gewöhnlichen Calcinirofen ist. Die Salzsäure streicht in Jones'
Fabrik zugleich mit der Feuerluft zunächst durch einen aus
Chamottesteinen gemauerten Canal von 50 Fuß (15m,25)
Länge, 3½ Fuß (1m,07) Höhe und 2½ Fuß (76cm)
Weite; derselbe befindet sich auf der Hüttensohle und wirkt also
nicht sehr abkühlend; ein viel besserer Effect würde unbedingt
durch die in vielen andern Fabriken gebräuchlichen Gußeisenrohre
erzeugt werden. Darauf passirt das Gas eine
„Douche“ (shower-bath), nämlich einen Steintrog, auf dessen Deckel
etwa 80 Oeffnungen mit Wasserverschluß sich befinden; ein 25mm
weites Wasserrohr mit einer Anzahl feiner Oeffnungen läuft
darüber hin und producirt im Innern des Troges einen
fortwährenden feinen Regen, welcher das Gas abkühlt und den
Rauch aus demselben niederschlägt, wenn man mit Kohlen feuert,
ohne doch viel Säure dabei zu condensiren, weil die Wirkung eine
zu kurze ist. Das continuirlich in halber Höhe des Troges
(dessen Dimensionen 2m,15 × 1m,55
bei 2m,15 Höhe sind) ablaufende Wasser schmeckt nur wenig
sauer und zeigt höchstens ½° B. Von da tritt das
Gas unmittelbar in einen ganz gewöhnlichen steinernen
Condensationsthurm von 7 Fuß (2m,14) im Quadrat und 50 Fuß (15m,25)
Höhe ein, welcher für die sämmtliche Production genügt; von
seiner Spitze führt ein 15 zölliges (381mm-)Thonrohr wieder hinunter und in einem
Schornstein. Die abfließende Säure zeigte sich 28° Tw.
heiß gemessen, also mindestens 30° Tw. kalt, und es kann
gar keinem Zweifel unterliegen, daß man durch etwas bessere
Condensationseinrichtungen auch noch stärkere Säure wird
erhalten können. Ueber die Quantität
der erhaltenen Salzsäure konnte ich leider keine Auskunft
erhalten, weil dieselbe nicht gut gemessen werden konnte; dies
wäre jedenfalls sehr wünschenswerth, um eine bessere Vorstellung
davon zu erlangen, ob das in der Douche condensirte Gas wirklich
nur einen unerheblichen Bruchtheil des ganzen ausmacht. Die
Condensation ist gut; denn eine in meinem Beisein aus dem
Schornstein gewonnene Probe des Gases zeigte nur 0,2 Grains H Cl auf den Cubikfuß (2g,3 H Cl
pro 1cbm), was noch innerhalb der von der Alkali-Act
gesetzten Grenze ist. Eine Belästigung durch Salzsäuredämpfe in
der Fabrik selbst findet überhaupt gar nicht statt; es war
selbst während der ersten, immerhin stärksten Einwirkung der
Schwefelsäure kein Gas um den Ofen herum zu spüren; die Thüren
können natürlich ganz lutirt werden, wenn der Zug nicht
hinreichend sein sollte, da man nur ein Schauloch in den Ofen
hinein braucht, und somit ist selbst bei schlechterm Zuge keine
Gefahr eines Entweichens von Gas vorhanden. Da kein Register
zwischen Pfanne und Ofen existirt, so ist auch diese Quelle von
Gasverlust verstopft, und da das Sulfat ganz ausgezeichnet und
fast ohne Säureüberschuß abgeröstet wird, so ist auch die beim
Ausziehen der Chargen stattfindende Belästigung durch das von
derselben ausgehende Gas nur ganz unbedeutend; wenigstens war
dies bei meinem Besuche der Fall, und wurde mir bestimmt
versichert, daß es immer so sei.
Es wird schließlich den technischen Leser interessiren zu hören,
daß die Anlagekosten des neuen, verbesserten Ofens (nach der
Construction von Goodman) sich auf
300 Pfd. Sterling für sämmtliche Maschinerie und Eisentheile
belaufen, wozu noch etwa 60 Pfd. St. für die Einmauerung und 40
Pfd. St. für eine kleine Dampfmaschine kommen, im Ganzen also
400 Pfd. St., zuzüglich einer mäßigen Patentgebühr. Dies ersetzt
zwei gewöhnliche Pfannen und zwei Calciniröfen, welche wohl
ebensoviel kosten; der Einwand, welcher gegen Hargreaves'
Verfahren mit Recht erhoben wird, nämlich die enormen
Anlagekosten, existirt also in diesem Falle nicht. Jones und
Walsh' Apparat nimmt schließlich nur ein Viertel des Raumes ein,
wie die zu einer gleichen Production nach dem alten Verfahren
erforderlichen Pfannen und Oefen. Alles dies wird wohl mein im
Eingänge dieser Mittheilung ausgesprochenes, günstiges Urtheil
bestätigen, zu welchem ich durch eigene, unabhängige
Untersuchung der Sache gekommen bin.
Tafeln
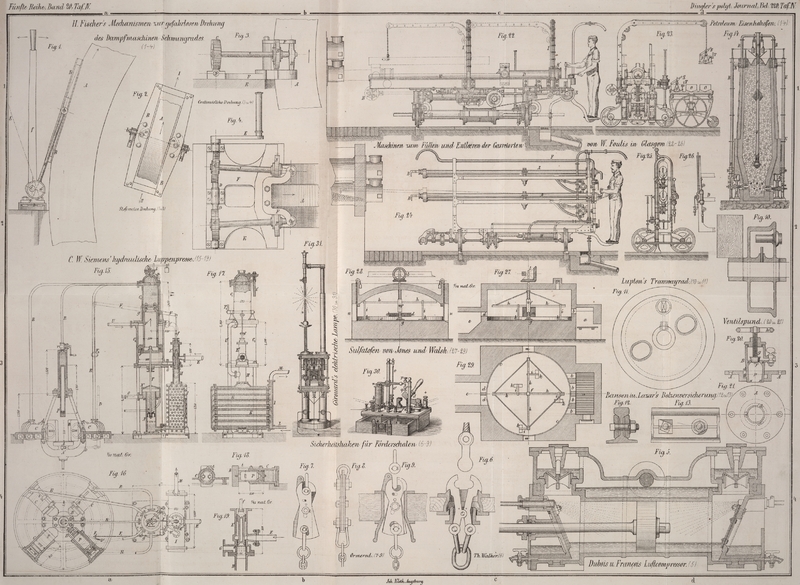