Titel: | Die Porzellanfabrik von Krister in Waldenburg. |
Fundstelle: | Band 154, Jahrgang 1859, Nr. XL., S. 176 |
Download: | XML |
XL.
Die Porzellanfabrik von Krister in
Waldenburg.
Aus den Verhandlungen des Vereins zur Beförderung des
Gewerbfleißes in Preußen, 1859 S. 122.
Mit Abbildungen auf Tab.
III.
Die Porzellanfabrik von Krister in Waldenburg.
Das Waldenburger Revier ist berühmt durch seinen
Steinkohlenreichthum, der hier eine Industrie hervorgerufen hat, so blühend, wie sie
an keinem zweiten Punkte Niederschlesiens sich findet.
Ueberall sieht man rauchende Schornsteine in die Luft emporragen, und die Flamme der
Kohks- und Porzellanöfen weit durch die Nacht dahinleuchten.
Die Porzellanfabrik von Krister in Waldenburg ist eine
sehr umfangreiche Anlage, welche 1500 Arbeiter beschäftigt; ihre Besichtigung
geschah unter Leitung der Fabrikbeamten.
Die Rohmaterialien, welche in dieser Fabrik verwendet
werden, sind:
1) Der Porzellanthon kommt theils aus
Morl bei Halle, theils aus der dem Hrn. Krister gehörigen Grube bei Zern in der Nähe
von Meißen.
2) Der Kapselthon, eine graue,
feuerfeste Thonart, stammt aus Buschkau bei Freiburg; derselbe wird vermischt
mit
3)gestampfter Kapselmasse und dient alsdann zur
Anfertigung neuer Kapseln.
4)Feldspath aus den Brüchen bei Schreiberhau.
5)Alabastergyps kommt aus Löwenberg, wird gestampft,
gebrannt und dient alsdann zur Herstellung der Gypsformen.
Der bereits in Halle einmal geschlämmte Porzellanthon wird
in der Fabrik einer zweiten, sorgfältigen Schlämmung
unterworfen. Fig.
7 stellt den Apparat dar, in welchem dieses Schlämmen geschieht. Der Thon
wird in dem Fasse A mit Hülfe des Rührers a, a in Wasser aufgerührt, wobei sich die gröbsten
Theile zu Boden setzen; das Uebrige fließt durch das Rohr a' auf das grobe Sieb b', dann durch das
feinere b in den Kasten B,
in welchem sich die noch mitgerissenen, gröberen Theile zu Boden setzen. Das
Schlämmgut läuft in die Rinne C; hier setzen sich die
letzten, noch mitgerissenen, groben Theilchen ab, während die feine aufgeschlämmte
Masse durch das Haarsieb d in das Reservoir D läuft. – Die so geschlämmte Masse wird in
größeren Mengkübeln mit 1/4 ihres Gewichtes fein geriebenem Feldspath gemengt, in große
Abdampfpfannen geleitet, und hier durch Abdampfen das überflüssige Wasser entfernt.
Die Abdampfpfannen sind von rechteckiger Form, den
Salzpfannen der Salinen an Form und Umfang ähnlich. Das Rauchgemäuer besteht aus
gewöhnlichen Backsteinen; das Pfannenfutter aus Charmotte. Die Feuerung geht in
Zügen unter dem Charmotteboden entlang, welcher 3 1/2 Zoll stark ist. Hier wird die
Masse so weil verdampft, bis der zurückbleibende Thon sich mit Spaten in ziemlich
consistenten Stücken herausheben läßt. Gewöhnlich dauert das Abdampfen 40 Stunden.
Die so erhaltene Porzellanmasse wird durch Arbeiter geschlagen, um das Ganze
gleichförmig zu machen und die Luftblasen heraus zu schaffen, und ist jetzt zur
Verarbeitung geeignet.
Der Feldspath, welcher der Porzellanmasse zugesetzt wird,
wird zunächst gewaschen, dann in Charmotteretorten geglüht, um ihn mürbe zu machen,
abgeschreckt und auf ein Pochwerk gebracht, wo er zerstampft wird.
Das Pochwerk hat 14 Stampfen, deren Köpfe, mit eisernen
Schuhen versehen, 5 Zoll im Quadrat sind. Die einzelnen Stampfen stehen in 9 Zoll
Entfernung von Mitte zu Mitte. Von diesen 14 Stampfen dienen jedoch nur 7 für
Feldspath, die anderen 7 zum Zerstampfen der Kapselmasse. Die Daumenwelle macht 15
Umdrehungen in der Minute.
Hier sey gleichzeitig bemerkt, daß sich in der Fabrik noch zwei Stampfwerke zum Zerkleinern von Charmotte vorfinden, mit 14 Stampfen und 3
Hebedaumen für jede Stampfe, in ähnlichen Dimensionen, wie die Feldspathstampfen.
Die Daumenwelle macht hier 16 Umdrehungen in der Minute, und ist die Theilung der
Betriebsräder 2 Zoll.
Die gepochte Feldspathmasse geht durch Siebe und wird dann
nochmals gewaschen, wobei der entstehende Schaum, welcher sehr nachtheilig auf das
Porzellan einwirkt, abgenommen wird. Die gewaschene Masse kommt jetzt auf die
Mühlen. Es sind 60 Massenmühlen vorhanden, welche sich
mit 40 Mühlen zum Mahlen der Glasurmasse, die ganz analog eingerichtet sind, in
einem großen Saale befinden. Diese 100 Mühlen sind in 5 Doppelreihen à 20 Stück gruppirt und werden von einer
durchgehenden Betriebswelle a, in Fig. 8, mit Abzweigungen
durch conische Räder getrieben. Jedes der beiden conischen. Räder b, b sitzt mit einem Stirnrade c auf einer kurzen Welle; von jedem dieser Räder c,
c aus werden je zwei zur Seite eingreifende Stirnräder und dadurch zwei
parallel nebeneinanderlegende Wellen d umgetrieben, von
welchen aus durch conische Räder direct der Betrieb der Mühleisen e, e, e... bewirkt wird. Die Anordnung der Mühlen in der Doppelreihe
erhellt noch deutlicher aus Fig. 9. Durch das erwähnte
Stirnrad c werden die nebenliegenden, auf den Wellen d, d befestigten Stirnräder c',
c', und somit auch die conischen Räder f, f
umgetrieben. Diese haben 15 Zoll Durchmesser und 1 Zoll Theilung. Die 2 Zoll im
Durchmesser haltenden Mühleisen e, e sind bei g, g mit dreizölligen Hülsen umgeben. Ueber den
horizontalliegenden conischen Rädern befindet sich eine Kuppelung, deren Handhebel
mit h, h bezeichnet sind; durch dieselbe ist es
ermöglicht, den Betrieb der Mühleisen auszurücken; diese machen pro Minute 10 bis 11 Umdrehungen. Die in den 30 Zoll im
Durchmesser haltenden Kübeln i, i liegenden Mahlsteine
sind ein grobkörniges Sandsteinconglomerat; der Bodenstein ist kreisrund mit 26 Zoll
Durchmesser und 6 1/2 Zoll Höhe, und die Form des Läufers in Fig. 10 und Fig. 11
wiedergegeben. Jeder Feldspathmahlgang geht 18 Stunden; alsdann ist der Feldspath
fein genug, um der Porzellanthonmasse zugesetzt und mit ihr auf schon beschriebene
Weise weiter verarbeitet zu werden.
Der rohe Kapselthon wird in Mühlen, von denen je vier zusammenstehen und einen Satz bilden, geknetet;
diese Anordnung ist in Fig. 12 skizzirt. Die in
der Mitte der 4 Mühlen stehende Welle a wird von der
Hauptbetriebswelle b umgetrieben und betreibt durch
Stirnräder die stehenden Messerwellen c, c der 4
Thonschneidemaschienen; die Messer sind 4 Zoll breit und unter 15 bis 20 Grad gegen
die Horizontale geneigt; die Wellen machen pro Minute 12
Umdrehungen.
Der aus einer Mühle kommende Thon wird mit gepochter und gesiebter Kapselmasse
beschüttet und auf die folgende Mühle gegeben. Der durch die vier Mühlen gegangene
Thon wird schließlich wieder mit Kapselmasse bestreut, auf die Drehbänke gebracht
und dort verarbeitet. Das Pochen der Kapselmasse geschieht auf dem schon oben angeführten
Pochwerke mit 7 Stampfen. Die gepochte Masse fällt aus der schrägen Pochrinne auf
ein Sieb mit Schüttelkasten, und wird die gesiebte Masse durch einen Elevator
fortgeschafft. Die gedrehten Kapseln werden in der Nähe der oberen Etage des
Porzellanofens nur lufttrocken gemacht und alsdann sogleich, ohne verglüht zu seyn,
im Porzellanofen verwendet.
Die nach oben beschriebener Methode hergerichtete Porzellanmasse wird behufs der weiteren Verarbeitung in Lappen
ausgemangelt. Sollen Tassen und Teller daraus gefertigt werden, so wird die Masse auf der Drehbank mit
Hülfe von Gypsformen aus dem Rohen gearbeitet, und alsdann von einem zweiten
Arbeiter die Form der Gegenstände mit Schablone und Messer auf der Drehbank
vollendet. Andere Gegenstände werden nicht aus gemangelten Lappen, sondern direct
aus einer Partie Masse, die auf die Drehbank gebracht wird, mit der Hand aus dem Rohen geformt, und die
Vollendung der Form auf einer zweiten Drehbank vorgenommen. Schnauzen, Henkel und
ähnliche, nicht drehbare Gegenstände werden in Gypsformen gepreßt und, nachdem sie
lufttrocken geworden sind, mit Hülfe von Schlicker, d.h. mit Wasser aufgerührter
Porzellanmasse, an die zugehörigen Geräthe gekittet. Die Pfeifenköpfe, welche hier in großen Massen fabricirt werden, werden
einfach mit der Hand gedreht.
Die so geformten Gegenstände werden lufttrocken gemacht, in der oberen Etage des
Porzellanofens in Cassetten verglüht und alsdann glasirt.
Die Glasur besteht aus einem Gemenge von vielem Feldspath
und wenig Porzellanthon, welcher in den schon beschriebenen Mühlen hergestellt wird.
Die quantitative Zusammensetzung der Glasur ist ein Geheimniß der Fabrik. In diese
mit Wasser aufgerührte Glasurmasse werden die verglühten Gegenstände, das Biscuit,
getaucht, und die Stellen, an welchen sie beim Eintauchen angefaßt wurden, mit einem
Pinsel mit der Glasurmasse bestrichen. Die Glasurmasse zieht schnell in das poröse
Biscuit ein, so daß dieses binnen kurzer Zeit trocken erscheint. Die so
hergerichteten und wieder trocken gewordenen Biscuitgegenstände werden in Kapseln
verpackt und in die untere Etage des Porzellanofens eingetragen.
Die Porzellanöfen dieser Fabrik haben nur zwei Etagen; die
dritte, welche hier vorhanden zu seyn scheint, dient nur als Fuchs, die zweite Etage
zum Verglühen und die untere zum Brennen der gearbeiteten Gegenstände. Jeder Ofen
hat sieben Feuerungen in seinem Umkreise. Eine Skizze solcher Feuerung findet sich
in Fig. 13 u.
Fig. 14.
Bei jeder Feuerung ist oberhalb des Feuerraumes C eine
horizontale, von den schiefen, nach der Oeffnung b
laufenden Seitenwänden a', a' begränzte Fläche a, auf welcher die Steinkohlen aufgeschichtet und
vorgewärmt werden. Die vorgewärmten Kohlen werden alle fünf Minuten in die Oeffnung
b geschoben und fallen in den Feuerraum C, dessen vordere Seite sie vollständig ausfüllen, so
daß der Zug nur unterhalb des nach hinten geneigten Rostes d,
d eintreten kann. Neben jeder Feuerung ist eine Probezugöffnung angebracht
zur Beobachtung der Gluth im Ofen und zur Herausnahme einzelner Stücke
Probegeschirr. Der Brand dauert 18 bis 21 Stunden; es wird so lange gefeuert, bis
eine herausgenommene Probe weißen Geschirres, gewöhnlich eine Tasse, nicht mehr
bläulich, sondern rein weiß erscheint. Dann verschließt man die Feuerungen, setzt
den Ofen zu und läßt ihn erkalten; dieses dauert etwa drei Tage. Alsdann werden die
vermauerten Ofenöffnungen aufgebrochen, der Ofen ausgeräumt, die Kapseln geleert,
und das erhaltene Geschirr sortirt; die vorstehenden Kanten werden abgeschliffen,
kleine Fehler durch Ausschleifen mit Porzellanscheiben entfernt, und die dadurch
entstandenen Flecke
durch Poliren mit einer kleinen Holzscheibe und Polirsand geglättet; solche Stellen
haben gegen die übrige Glasur nur einen matten Glanz. Das Abschleifen der Tellerfüße
geschieht auf gußeisernen Scheiben.
Ein Theil des Geschirrs wird weiß verkauft, das übrige bemalt und vergoldet. Die Farben werden, mit
Terpenthinöl angerührt, aufgetragen; die Zusammensetzung derselben ist größtentheils
Fabrikgeheimniß. Zur Vergoldung wird auf chemischem Wege fein zertheiltes Gold mit
Terpenthinöl angerührt.46) Die so bemalten und vergoldeten Gegenstände werden in der Muffel in
besondern Muffelöfen gebrannt, wobei mit Farben bemalte
Probescherben als Richtschnur dienen, und später die Vergoldung durch Poliren mit
Achat, Ueberwischen mit Schlämmkreide und Poliren mit Blutstein glänzend gemacht;
der Blutstein selbst wird auf Thonsteinen mit Zinnasche angeschliffen.
Das Bemalen der ordinairen Porzellanwaren geschieht durch
Knaben, welche unter Leitung eines Lehrers darin große Fertigkeit erlangen.
Eine in der Ruffer'schen Maschinenfabrik zu Breslau
erbaute Dampfmaschine treibt sämmtliche Maschinen der
Fabrik und zwar: 100 Massenmühlen, 8 Thonschneidekübel, 1 Feldspathstampfwerk, 2
Charmottestampfwerke, 1 Schachtpumpe und 1 Mahlgang für Getreide. Die Maschine hat
33 Pferdekräfte, arbeitet mit 4 Atmosphären Dampfspannung und macht 48 Umdrehungen
in einer Minute. Der Cylinderdurchmesser beträgt 11 Zoll, der Kolbenhub 23 Zoll. Zur
Dampferzeugung dienen zwei 32 Fuß lange Kessel.
Mit der Porzellanfabrik ist eine Schneidmühle verbunden,
welche die Breter zu den zur Verpackung der Porzellangegenstände nöthigen Kisten
herstellt. In derselben befinden sich folgende Maschinen: 3 Sägegatter, 2 Kreissägen
und 1 Charmottepochwerk. Zum Betriebe dieser Maschinen dient eine auf der Carlshütte
zu Altwasser erbaute Dampfmaschine mit liegendem Cylinder
von 12 Pferdekräften. Der Cylinderdurchmesser beträgt 11 Zoll, der Kolbenhub 28
Zoll. Die Maschine macht 46 bis 48 Umdrehungen in einer Minute und arbeitet mit
einer Dampfspannung von 3 Atmosphären Ueberdruck. Zur Dampferzeugung für diese
Maschine gehören ebenfalls 2 Kessel.
Tafeln
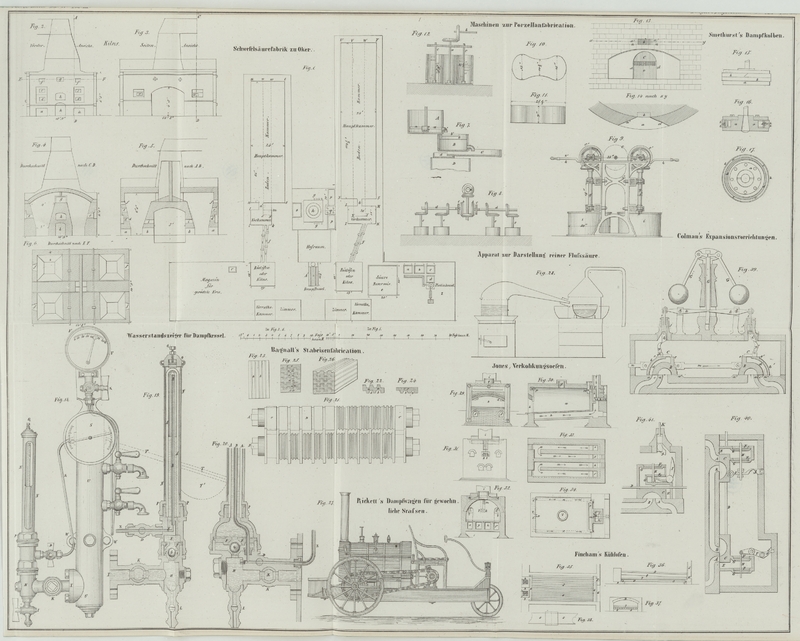