Titel: | Ueber hohle Eisenbahnachsen; von Hrn. J. E. Mac Connel. |
Fundstelle: | Band 131, Jahrgang 1854, Nr. XXVI., S. 109 |
Download: | XML |
XXVI.
Ueber hohle Eisenbahnachsen; von Hrn. J. E. Mac Connel.
Aus dem Civil Engineer and Architect's Journal, Novbr.
1853, S. 387.
Mit Abbildungen auf Tab.
II.
Mac Connel, über hohle Eisenbahn-Achsen.
Um recht starke und dauerhafte Eisenbahnachsen herzustellen, welche einen der
wichtigsten Punkte für die Sicherheit der Reisenden bilden, kam der Verfasser nach
wiederholten Versuchen und mit Benutzung aller von Andern darüber gemachten
Erfahrungen, zu dem Resultate, daß die hohlen oder röhrenförmigen Achsen, an und für
sich, wenn sie gehörig angefertigt wurden, alle Eigenschaften vereinigen, welche
erforderlich sind, um die beste Form mit Leichtigkeit, Festigkeit, Gleichartigkeit
der Textur des Materials, Elasticität zur Verminderung der nachtheiligen Stöße und
Erschütterungen, und folglich mit Dauerhaftigkeit zu verbinden.
Die Wahl der Röhrenform für die Achsen wurde durch die Erfahrung veranlaßt, daß mit
einem bedeutend geringern Gewicht des Materials eine größere Festigkeit erlangt
werden kann, um der Torsion, der Biegung durch Druck oder Belastung, oder den Stößen
zu widerstehen. Da der Widerstand einer massiven Achse gegen die Biegung und Torsion
im Verhältniß der vierten Potenz des Durchmessers (oder des Quadrats vom Quadrat), das Gewicht aber
nur wie das Quadrat des Durchmessers steigt, so haben zwei massive Cylinder, deren
respective Durchmesser 4 und 5 Zoll betragen, oder im Verhältniß von 1 zu 1 1/4
stehen, ein Gewichtsverhältniß von 16 zu 25 oder von 1 zu 1 1/2, dagegen einen
Widerstand von 256 zu 625, oder von 1 zu 2 1/2. Macht man nun die stärkere Achse auf
zwei Drittel des Durchmessers hohl, so wird sich ihr Gewicht um 1/2 (2/3 ×
2/3 = 4/9 oder fast 1/2) und ihr Widerstand nur um 1/5 (2/3 × 2/3 ×
2/3 × 2/3 = 16/81 oder fast 1/5) vermindern, und das Verhältniß zu der
schwächeren massiven Achse wird dann seyn: 1 zu 1 1/4 im Durchmesser, 1 zu 7/8 im
Gewicht, und 1 zu 2 im Widerstande. Daher ist der Widerstand der doppelte, mit 1/8
weniger Gewicht.
Die Anwendung hohler Achsen wurde schon vor mehreren Jahren versucht, jedoch nicht
fortgesetzt, weil man bei der damaligen Fabricationsweise nicht im Stande war, eine
hinlängliche Gleichförmigkeit der Eisenstärke an allen Punkten der Röhre und ein
vollkommen fehlerfreies Material sicher zu erzielen. Das angenommene Verfahren
bestand darin, zwei oder drei Stäbe von halbkreisförmigem Querdurchschnitt
auszuwalzen, welche alsdann mit stumpf gegen einander stehender Fuge – jedoch
ohne inwendigen Druck und mit massiven Enden, da wo die Zapfen vorhanden waren
– zusammengeschweißt wurden. Da nun die Schweißung dieser Achsen ohne Dorn
oder innern Druck bewerkstelligt wurde, so war ihre Festigkeit sehr ungleich und es
konnte der schwächste Punkt ganz nahe an demjenigen liegen, wo die größte Festigkeit
erforderlich war.
Um diese gewichtigen Einwürfe zu heben, wurde vom Verfasser bei der Anfertigung der
Achsen ein Verfahren eingeführt, welches allen Bedingungen entspricht, indem es die
größte Festigkeit mit dem wenigsten Material, einer gleichförmigen Textur,
vollkommen gleicher Eisenstärke und mit sicherer Ausführung verbindet.
Das Verfahren ist das nachstehende: Eine Anzahl Segmentalstäbe von dem besten Eisen
wird von solchem Querschnitt ausgewalzt, daß sie für das Schweißen zusammengelegt,
einen vollständigen Cylinder, Fig. 16, bilden, welcher
etwa den 1 1/2fachen Durchmesser der vollendeten Achse hat. Die Stäbe müssen genau
zusammenpassen, so daß keine Zwischenräume bleiben, und so übereinander greifen, daß
sie eine vollkommen feste Schweißung gestatten, wie Fig. 17. zeigt.
Dieser Cylinder von losen Segmentalstäben wird einstweilen durch eine Schraubenzwinge
zusammengehalten und jedes Ende wird in den Ofen gebracht und erhält eine
Schweißhitze, so daß die Stäbe theilweis mit einander verbunden werden, worauf man
die Zwingen wegnehmen kann. Darauf wird die ganze Röhre in den Ofen gebracht, erhält dort eine
Schweißhitze und gelangt alsdann zwischen eine Reihe kreisrunder Caliber der Walzen,
B, B, Fig. 17, eines
Walzengerüsts. Jedes Caliber ist mit einem Dorn A von
eyförmiger Gestalt versehen, und zwar genau in der Mitte. Diese Dorne sind an
starken Stangen befestigt, deren Enden eine feste Lage haben, so daß der Dorn in
seiner gehörigen Stellung bleibt, wenn Druck oder Zug, während der Walzarbeit,
darauf einwirkt. Die Dorne bestehen aus Gußeisen, sind schalenhart und werden
mittelst einer starken Mutter an der Verstärkung der Stange festgehalten, können
aber auf diese Weise leicht weggenommen werden.
Die Bewegung der Walzen kann mittelst eines ein- und ausrückbaren Vorgeleges
leicht gewechselt werden, so daß, wenn die Achse durch ein Caliber und über den Dorn
nach einer Richtung durchgewalzt worden ist, sie nach der entgegengesetzten gehen
kann. Dann wird die Achse in das nächste, engere Caliber des Walzgerüsts, welches
mit einem kleinern Dorn versehen ist, gebracht und auch vorwärts und rückwärts
durchgewalzt, und so durch eine Reihe von Calibern mit Dornen, von denen jedes in
einem gewissen Verhältniß enger ist, als das vorhergehende. Bei jedesmaligem Wechsel
des Calibers wird die Achse um ein Viertheil ihrer Peripherie gedreht, so daß sie
auf allen Seiten gleichen Druck erhält und das Eisen möglichst gleichförmig
zusammengepreßt wird, was sehr wesentlich ist, damit die Schweißung an jedem Punkt
der Röhre eine gleiche ist.
Die in einer Versammlung des Ingenieur-Vereins zu Birmingham vom Verfasser
vorgelegten Stücke zeigten die Vollkommenheit und Trefflichkeit der Arbeit, wovon
auch die Proben einen Beweis lieferten, denn die Achsen wurden nicht allein äußern,
starken Stößen, sondern auch dem auseinander treibenden Druck eines Dorns
unterworfen, welcher in das Innere getrieben wurde. Niemals wiesen diese Proben eine
mangelhafte Schweißung nach, obgleich sie mit Stücken angestellt wurden, welche von
den Enden abgeschnitten worden waren und an deren vollkommener Schweißung man am
ersten zweifeln konnte.
Nachdem die Achsen ausgeschweißt und durchgewalzt worden sind, so daß sie ihre
erforderliche Stärke erlangt haben, gelangen sie zu einem Hammer, dessen Bahn und
Amboß runde Gesenke haben und in denen sie über ihre ganze Oberfläche geebnet
werden. Während dieser Arbeit fällt ein dünner Wasserstrahl darauf, wodurch der
Schmied in Stand gegesetzt wird, durch die Ungleichheit der Farbe sogleich die
schlechten Schweißstellen zu erkennen. Von dem Hammer kommen die Achsen zu den
Kreissägen, welche sie zu der erforderlichen Länge abschneiden, so daß sie nun, bis auf die Bildung der
Schenkel welche in den Pfannen der Büchsen liegen, fertig sind.
Wenn die Achsen von dem Hammer kommen, so ist ihre Oberfläche vollkommen rein, sowohl
auf der äußern als innern Seite, indem der Hammerschlag gänzlich entfernt ist. Die
Enden werden dann wieder gewärmt und mittelst eines Hammers die Schenkel oder Zapfen
gebildet, so daß sie genau in die Büchsen passen; während des Schmiedens wird ein
Dorn in das Ende der Röhre gesteckt.
Es können diese Schenkel aber auch durch ein Walzwerk hervorgebracht werden, dessen
Walzen Tafeln von der ganzen Länge der Achsen haben und dieselben der Quere nach
durchwalzen; beide Tafeln sind Duplicate von einander und Matrizen der fertigen
Achse.
Die Fabrication dieser Achsen wird jetzt von der
Patent-Achsen-Compagnie (Patent Shaft
Company) ausgeführt und zwar auf eine dem hohen Ruf dieser Fabrik
entsprechende Weise.
Als Beispiel der Ersparung an todtem Gewicht, welche man durch diese Achsen erlangt,
wollen wir eine Eisenbahn als Beispiel annehmen, die im Ganzen 15000 Personenwagen
und Frachtwagen gebraucht, von denen jeder 10,000 engl. Meilen jährlich läuft. Das
Gewicht zweier massiven Achsen betrage 5 Ctr., so wird, wenn man sie durch hohle
Achsen von gleicher Festigkeit ersetzt, das Gewicht für jeden Wagen um 1 1/2 Ctr.
vermindert. Vertheilt man dieses Gewicht auf die obige Wagenzahl, so beträgt es
14,250,000 Tonnen für 1 engl. Meile per Jahr, und nimmt
man die Kosten der Locomotiv-Zugkraft zu 1/4 Pence per Tonne und Meile an, so beträgt die ersparte Summe jährlich 11,700 Pfd.
Sterl., ohne die übrigen Vortheile, die Schonung der Bahn etc. zu
berücksichtigen.
An den Achsen, welche in der Versammlung der Ingenieur-Gesellschaft vorgezeigt
wurden, waren zwei verschiedene Arten von Schenkeln vorhanden, parallele mit
abgerundeten Scheiben und die doppelt conischen, wie sie auf mehreren englischen
Bahnen, z.B. auf der Nordbahn, der West-, Bristol-Exeter-, der
Südwaliser und der Süd-Devon-Bahn, angewendet werden. Für beide Arten
von Schenkeln sind die hohlen Achsen zweckmäßig, wiewohl nicht in Abrede gestellt
werden kann, daß bei der Fabrication der doppelt conischen Schenkel sowohl an den
massiven als hohlen Achsen die Textur des Eisens leichter verändert werden kann, was
bei den parallelen nicht der Fall ist.
Um die verhältnißmäßige Widerstandsfähigkeit der massiven und der hohlen Achsen gegen
eine in senkrechter Richtung darauf einwirkende Kraft kennen zu lernen, wurden unter
Leitung des Hrn. Marshall, des Secretärs der
Ingenieur-Gesellschaft, Versuche angestellt. Jede Achse ruhte auf massiven gußeisernen
Blöcken, welche wie die Schienen auf denen die Achse steht, 4 Fuß 11 Zoll (engl.
Maaß) von einander entfernt waren. Ein 18 (englische) Ctr. schwerer, gußeiserner
Rammklotz wurde alsdann von 12 Fuß Höhe auf die Mitte der Achse fallen gelassen und
die Größe der erfolgten Biegung gemessen. Darauf wurde die Achse um die Hälfte
umgedreht und der Rammklotz wieder herabgelassen, so daß die Biegung in
entgegengesetzter Richtung erfolgte. Dieses Verfahren wurde so lange wiederholt, bis
die Achse zerbrach. Die allgemeinen Resultate dieser ersten
Reihe von Versuchen sind folgende:
Eine alte massive Achse, von 3 3/4 Zoll Durchmesser in der
Mitte, und 4 1/2 Zoll an den Enden, welche drei Jahre lang benutzt worden war, wurde
beim ersten Schlage des Rammklotzes 8 3/4 Zoll gebogen; beim zweiten Schlage in
entgegengesetzter Richtung wurde sie fast gerade gemacht, durch den dritten Schlag
um 10 Zoll gebogen und mit dem sechsten Schlag brach sie quer durch.
Eine neue massive Achse von denselben Dimensionen, wurde
durch den ersten Schlag 9 3/4 Zoll gebogen, beim zweiten fast gerade gemacht, beim
dritten um 9 1/2 Zoll, beim vierten um 2 1/2 Zoll gebogen und beim fünften zerbrach
sie 3/4 Zoll von dem Mittelpunkte. Das Bruchansehen war auf 3/4 des Querschnitts
krystallinisch, der übrige Theil fadig.
Eine neue hohle Achse von 4 5/8 Zoll Durchmesser der
ganzen Länge nach, wurde durch den ersten Schlag 5 Zoll gebogen, durch den zweiten
fast gerade gemacht und durch den dritten wieder um 5 Zoll gebogen. Der neunte
Schlag veranlaßte eine Biegung von 4 1/2 Zoll und der zehnte eine solche von 1 3/8
Zoll. Bis zum fünfzehnten Schlage wurde sie abwechselnd gebogen und es betrugen die
Biegungen 2 bis 3 1/2 Zoll. Es zeigte sich keine Spur von Schwäche oder Bruch, beim
fünfzehnten Schlag aber eine leichte Hebung der Oberfläche. Die Schläge wurden noch
bis zum siebenundzwanzigsten fortgesetzt, wobei die Biegungen von 2 bis 3 5/8 Zoll
wechselten, worauf in der Mitte der Achse ein 1 1/2 Zoll langer Querbruch erfolgte.
Der achtundzwanzigste Schlag bog sie 3/8 Zoll und da er auf die entgegengesetzte
Seite von dem Bruch geführt wurde, so schloß er denselben. Beim neunundzwanzigsten
Schlag wurde die Achse zwei Drittel durchgebrochen und um 9 1/2 Zoll gebogen; die
Bruchfläche war sehr fadig.
Eine zweite Reihe von Versuchen wurde in der Absicht
gemacht, die verhältnißmäßige Festigkeit der Schenkel an hohlen und an massiven
Achsen in Beziehung auf Brüche kennen zu lernen.
Die Achsen lagen auf einem Amboß und zwar so, daß die innere Scheibe des Schenkels 1
1/2 Zoll über die Kante des Amboßes wegstand, wodurch also die Unterstützung der
Achse in der Nabe des Rades dargestellt wurde. Es wurden 100 Schläge mit einem 24
Pfund schweren Vorschlaghammer oder Schlägel auf die obere Seite des vordern Endes
des Schenkels geführt und dabei nach 12 oder 13 Schlägen der Schmied gewechselt. Die
Biegung des Schenkels wurde alsdann gemessen und die Achse um die Hälfte gedreht,
worauf diese Seite wiederum 100 Schläge erhielt. Dasselbe Verfahren wurde dann
ferner wiederholt. Die allgemeinen Resultate dieser Versuche waren die folgenden:
–
Bei einer alten massiven Achse mit Schenkeln von 3 auf 5
Zoll, welche drei Jahre im Gebrauch gewesen war, erfolgte der Bruch des einen
Schenkels nach 205 und der des andern nach 53 Schlägen; beide Brüche gingen quer
durch den Schenkel an der Scheibe.
Bei einer neuen massiven Achse, mit Schenkeln von 3 auf 6
Zoll, brach der Schenkel nach 570 Schlägen ab; der Bruch war unregelmäßig von
Gestalt und fadig.
Eine neue hohle Achse, mit Schenkeln von 3 auf 5 Zoll,
erhielt 400 Schläge auf den Schenkel, welche das Ende 5/8 Zoll niederbogen und eine
Längenspalte an die untern Seite von 3 3/4 Zoll Länge verursachten, jedoch keinen
Querbruch.
Eine neue hohle Achse mit gleich großen Schenkeln erhielt
800 Schläge auf das Schenkelende, wodurch es um 1/8 Zoll gebogen wurde und eine
Längenspalte auf beiden Seiten entstand, die aber nur einen 3/4 Zoll langen
schwachen Querbruch in der Nähe der Scheibe veranlaßte.
Die Versuche über den Widerstand gegen ein in der Querrichtung auf die Mitte der
Achse wirkendes schweres Gewicht, wobei man dasselbe abwechselnd auf die eine oder
die andere Seite wirken läßt, zeigen, daß die hohlen Achsen fast doppelt so fest in
dieser Beziehung sind, als die massiven. Die Biegung betrug bei jenen nur 5, bei
diesen aber 9 3/4 Zoll, die Auzahl der Schläge durch welche die ersteren zerbrochen
wurden 29, die Anzahl, durch welche der Bruch der zweiten erfolgte, nur 5. Dieß ist
ein ganz unwiderlegbarer Beweis von der größern Festigkeit der hohlen Achsen.
Die hohle Achse wurde nur 1/8 Zoll oval in ihrer Mitte nach dem siebenten Schlag, und
erst beim 28sten Schlag, kurz vor dem Bruch, wurde sie 1/4 Zoll oval.
Die Versuche über die Festigkeit der Schenkel zeigen, daß während bei den massiven
Achsen ein Querbruch dicht an der Scheibe erfolgt, die Schenkel der hohlen Achsen mehr
Hammerschläge aushalten können und dann nur der Länge nach aufreißen, was ebenfalls
ein Beweis ihrer weit größeren Festigkeit ist.
––––––––––
Bei den Discussionen welche nach dem Vorlesen obigen Aufsatzes in der
Ingenieur-Gesellschaft entstanden, wurde bemerkt, daß auf dem Bruch der
hohlen Achse alles Eisen fadig erscheine, während der Bruch der massiven
meistentheils krystallinisch sey; ferner, daß man bei den hohlen Achsen von gleicher
Festigkeit etwa zwei Fünftel an Gewicht erspart, daß man der größeren Sicherheit
wegen ihnen in der Praxis aber ein Drittel vom Gewicht der massiven gebe. Es wurde
ferner bemerkt, daß die hohlen Achsen bereits auf der Nordwest-,
Midland- und großen Nord-Bahn angewendet werden, und schon über 500
angefertigt worden sind, wovon einige schon seit neun Monaten mit bestem Erfolg in
Gebrauch sind.
Hr. MacConnell bemerkte, daß von welcher Beschaffenheit
auch die einwirkende Kraft, oder die von den Stößen veranlaßte Veränderung der
Textur seyn mag, die Wirkung der ununterbrochenen Stöße und Erschütterungen bei
einer hohlen Achse sehr vermindert werden muß, indem die Stöße von der Höhlung
aufgefangen und unterbrochen werden, wogegen eine massive Eisenmasse sie
fortpflanzt. Er zeigte eine hohle und eine massive Achse vor, welche zwei Stunden
ohne Oel in einer Drehbank heiß gelaufen waren und zwar mit einer Geschwindigkeit
von 20 englischen Meilen in der Stunde; die Schenkel dieser massiven Achse
zerbrachen mit 179 Schlägen und der Bruch war ganz kurz und krystallinisch, wogegen
die Schenkel der hohlen Achse nach 400 Schlägen bloß an mehreren Stellen der Länge
nach aufsprangen.
Tafeln
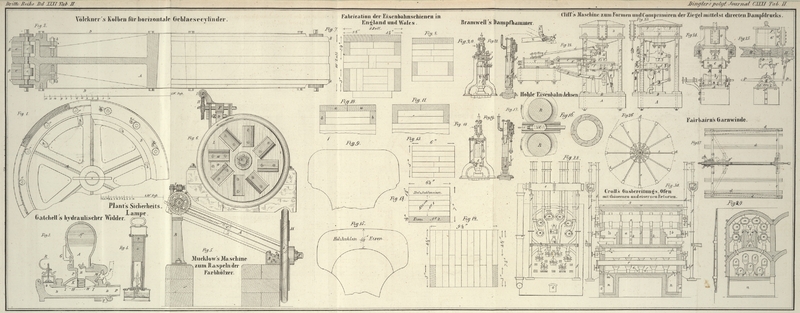