Titel: | Ueber den Gas-Weißofenbetrieb zu Königshütte in Schlesien; von Debette. |
Fundstelle: | Band 96, Jahrgang 1845, Nr. XCV., S. 377 |
Download: | XML |
XCV.
Ueber den Gas-Weißofenbetrieb zu
Koͤnigshuͤtte in Schlesien; von Debette.
Aus den Annales de mines, Quatr. Sér. T. V, p.
507 durch das polytechn. Centralblatt, 1845, 8. Heft.
Mit Abbildungen auf Tab.
V.
Debette, über Gas-Weißofenbetrieb.
Die meisten auf schlesischen Hütten verarbeiteten Erze eignen sich wegen ihrer
pulverförmigen Gestalt, wodurch der Gang der Hohöfen sehr erschwert und ohnehin
unregelmäßig gemacht wird, so wie wegen ihres Zinkgehalts nicht zu Anwendung der Faber'schen Methoden. Der aus anderen Versuchen sich
ergebende äußerst geringe Eisenverlust beim Weißmachen mit Gasen veranlaßte daher zu
Construction eines Weißofens mit besonderm Gasgenerator, in welchem man überdem die
rohe Steinkohle unmittelbar benuzen und durch zwekmäßige Windführung eine sehr
vollständige Verbrennung erreichen zu können hoffte. Der Hüttenmeister Eck auf
Königshütte wurde mit diesen Versuchen beauftragt, deren Resultate bis zum Oktober
1843 in Folgenden bestehen.
Ende 1841 wurde ein Weißofen construirt mit besonderm Gasgenerator, der durch einen
möglichst kurzen Canal mit dem Ofen in Verbindung stand. Die heiße Luft leitete man
aus dem Lufterhizungsapparate für den Hohofen ab. Der Generator war fast prismatisch
und so hoch, daß die durchgehende Luft schon in den unteren Schichten des
Brennmaterials völlig in Kohlenoxyd verwandelt wurde, die oberen Kohlenschichten
daher nur eine allmähliche Verkohkung erfuhren. Der Wind gelangte in den Generator
anfangs durch einen Rost, dieser verbrannte aber schnell und verstopfte sich oft und
man unterdrükte ihn daher später ganz. Die heiße Luft zum Verbrennen der Gase hatte
einen etwas höhern Druk, als die in den Generator geführte; die richtige Bestimmung
des Verhältnisses beider Luftquantitäten hatte manches Schwierige. Es ergab sich,
daß für einen Ofen von später zu beschreibender Dimension per Minute in den Generator 8 Kil., in den Flammofen 12,5 Kil. Luft
eingeblasen werden mußten. Die Luft war 75–100° C. heiß; man ließ sie
erst durch mehrere Düsen einströmen, erhielt aber so nur einzelne Flammenstrahlen
und keine vollständige Verbrennung. Man machte daher später einen Eisenblechkasten
mit einer Spalte mit starken umgebogenen schmiedeisernen Andern, aus welcher der
Windstrom mit einer Neigung von 40° ausströmte. Jezt war der Effect
vollständig; man erlangte auf der Ofensohle schnell Schweißhize und konnte in zwei
Stunden 9 bis 10 Pfd.
sehr graues Kohksroheisen einschmelzen. Um in der eingeschmolzenen Masse die
erforderliche Bewegung hervorzubringen, dienten zwei seitliche Düsen mit einer
Neigung von 25°; während des Gebrauchs war die durch den Windkasten
einströmende Luftmenge etwas vermindert. Indessen zeigte sich doch, troz der
geringen Dike der Eisenschicht, die weißmachende Wirkung der Gase nur gering, und
selbst durch Vermehrung der Kohlenconsumtion und starke Erhöhung der Temperatur kam
man nicht weiter, als daß 9 Cntr. in 7 Stunden mit 11 1/2 Proc. Eisenverlust und
Consumtion von 74 Kohle auf 100 Eisen weiß gemacht werden konnten. – Man
schritt nun zum Zusaz von 4–5 Proc. gepochten Eisenerzes (Eisenoxydhydrat)
beim Weißmachen und beschleunigte dadurch den Proceß sehr, unter gleichzeitiger
Verminderung des Kohlenconsums und Verflüssigung der Schlake. 900 Kilogr. Roheisen
wurden nun in 31/2–4 Stunden mit 10 1/2 Proc. Verlust und Consumtion von 49
Kohle auf 100 Eisen bearbeitet. – Das wöchentliche Ausbringen stieg auf
30,000 Kilogramme.
Vom September bis Oktober 1843 hatte der Apparat die aus dem
Längen-Verticaldurchschnitt Fig. 17 (nach A, B,
Fig. 18), dem
Grundriß Fig.
18 und dem Querdurchschnitt Fig. 19 (nach C, D,
Fig. 18)
ersichtliche Einrichtung. Die im Lufterhizungsapparat des zunächst gelegenen
Hohofens auf 88° C. erwärmte Luft gelangte durch das Rad t in den Cylinder T; von da
ging ein Theil derselben durch die Röhren c, c, c in den
starken Eisenblechkasten b und von da durch zwei Düsen
d, d von vierseitigem Querschnitt in den
Gasgenerator a; der andere Theil der Luft wurde durch
f in einen zweiten Cylinder g geleitet und von da zum größern Theil durch das Rohr i in den Kasten k, aus
dessen Spalte er unter der angegebenen Neigung in den Gasstrom einströmte; ein
kleiner Theil wurde durch die Röhren l' und l' aus dem Cylinder g nach
den seitlichen Düsen abgeleitet. Hähne an den Anfängen der Röhren c, c, c und i, l, l' dienten
zur Regulirung der einzelnen Theile des Luftströmungssystems. Eine kleine
Rostfeuerung h unter dem Cylinder g konnte zu Erhöhung der Temperatur des in den Ofen getriebenen
Luftantheils benuzt werden. Die im Grunde des Gasgenerators angebrachte Thür e, während der Arbeit durch Ziegelmauerung geschlossen,
diente zur wöchentlichen Reinigung des Generators. x ist
die durch eine eiserne Platte y verschließbare
Eintragsthür des Generators; r ist der Fuchs, H die Esse, V der
Verbindungscanal zwischen Generator und Flammofen, m der
Flammofen selbst, p die Arbeitsthür (geschlossen durch
eine an einem Balancier aufgehangene Schieberthür), q
der Abstich; u eine am hintern Theil angebrachte
Beobachtungsthür;
n, n sind Blechkamine, um unter der Bodenplatte und
längs der Seitenwände des Flammofens einen steten lebhaften Luftwechsel zu
unterhalten. Die Hauptdimensionen der Theile sind in Meter angegeben folgende:
Düsen des Generators 0,13 M. breit, 0,052 hoch; Distanz der Achsen derselben 0,261;
Höhe der Achse über der Sohle 0,261. Ganze Höhe des Generators 2,038; Entfernung der
Seitenwände oben 0,993, unten 1,070; Entfernung der Vorder- und Hinterwand
oben 0,366, in der Mitte 0,522, unten 0,444. Die Spalte, durch welche die Luft in
den Weißofen tritt, ist 0,784 breit, 0,010 hoch; die Gasleitung V 0,993 breit, 0,209 hoch; die seitlichen Düsen 0,026
weit; die Sohle des Flammofens 2,09 lang, 1,254 breit; der Fuchs 0,601 breit, 0,183
hoch, 0,183 lang; die Esse 4,624 hoch, bei einem Querschnitt von 0,601 : 0,418. Die
Dike der Thonsohle 0,078; Höhe des Gewölbes über der eisernen Sohle dicht hinter der
Feuerbrüke 0,680. Arbeitsthür 0,488 breit, 0,366 hoch. Die Windpressung betrug nur
19–20 Millim. Queksilber.
Der Ofen wurde bedient von zwei Mann, welche per Cntr.
Weißeisen 12 Centimes (1 Silbergroschen) erhielten. Wegen Mangels an Arbeitern
konnte des Nachts nicht gearbeitet werden, wodurch sich die Kohlenconsumtion erhöhen
muß. – Alle halbe Stunden wurde im Generator Kohle nachgegeben. Einer der
Arbeiter nahm die Platte y weg, goß ein wenig Wasser in
den Generator, um die entstehende Flamme zu erstiken, gab dann mit der Schaufel die
Kohlen in den Generator, sezte die Platte y wieder vor
und begoß sie abermals mit Wasser, was sich überhaupt wiederholte, so bald zwischen
y und der Wand sich kleine Flämmchen zeigten. Alle
acht Tage, Sonntags, nachdem die Kohlen der lezten Gicht vom Sonnabend
niedergebrannt waren, wurde die Oeffnung e geöffnet, der
Gasgenerator ganz entleert und seine Wände von Schlaken gereinigt. Nuß die Reinigung
im Laufe der Woche eintreten, so schiebt man nach Oeffnung von e oberhalb Eisenstangen ein, welche eine Art von Rost
bilden, der die Kohlen trägt und unterhalb dessen man den Herd reinigen kann.
Außerdem sind dicht an der Sohle des Generators drei kleine Oeffnungen angebracht,
durch welche man eiserne Stäbe einschiebt, die gewöhnlich liegen bleiben und nur von
Zeit zu Zeit einige Minuten herausgezogen werden, wobei der Wind alle nicht
verschlakte Asche herausbläst.
Beim Weißmachen selbst wird zuerst nach Beendigung des vorigen Abstichs die Sohle des
Weißofens wieder abgeglichen, dann 900 bis 1000 Kil. sehr graues, grobkörniges, in
kleine Schirbel zerschlagenes Roheisen mittelst einer am Ende schaufelartig
abgeplatteten Eisenstange eingetragen und gleichförmig vertheilt, darauf alle Oeffnungen geschlossen und der
Ofen sich selbst überlassen, indem man von Zeit zu Zeit durch u und einen kleinen Schieber in der Arbeitsthür p beobachtet. Diese Zeit benuzen die Arbeiter zum Herzutragen des
Roheisens und der Steinkohlen, des Erzzuschlags, des nöthigen Wassers, um es auf das
abgestochene Eisen zu gießen, zu Beseitigung der Schlaken, zum Zerbrechen des vorher
abgestochenen Eisens und Entfernung desselben aus der Schalenform u.s.f. Uebrigens
muß nach einiger Zeit die Rinde, welche sich auf dem einschmelzenden Eisen bildet,
aufgebrochen und die halbgeschmolzenen Massen in das Eisenbad zurükgebracht werden.
Nach 2–3 Stunden ist das Einschmelzen beendigt. Jezt paßt man die Röhren l und l' mit ihren Düsen an
die Ansäze des Cylinders g, öffnet die Hähne und dreht
dafür den Hahn an i etwas zu, bis der Anblik der Flamme
zeigt, daß man das richtige Verhältniß hergestellt hat. Nun wird das zuzusezende
Eisenerz mit etwas Wasser befeuchtet, gehörig umgestochen und mittelst eines
schaufelartigen Werkzeugs ein Korb voll (25 Kil.) in den Ofen gebracht und sogleich
mit einer am Ende hakenförmig umgebogenen Brechstange mit der Eisenmasse
zusammengearbeitet. Nach 1/2 bis 3/4 Stunden zeigt der Glanz des schmelzenden Eisens
die Bewegung darin und eine mit einem eisernen Löffel genommene Probe, ob man den
Zusaz von Eisenoxyd wiederholen muß, was dann auf gleiche Weise geschieht. Selten
nur ist es nöthig, wenn nicht ein zu gahres Eisen einen außergewöhnlichen Erzzusaz
nöthig macht, die Schlaken abfließen zu lassen. Die bei der Arbeit im Ofen etwas
unbequeme Stichflamme könnte man durch eine kleine Düse mit kalter Luft, wie in
Wasseralfingen, beseitigen. – Sobald das Weißmachen beendigt ist, sticht man
das Eisen in eine flache, von Eisenplatten gebildete, mit Kalkwasser ausgestrichene
Form ab und trennt dann durch Uebergießen mit Wasser die Schlafen. Das Stichloch
wird dann wieder verschlossen, die Herdsohle gereinigt, geebnet und zu einer neuen
Operation geschritten. Nach dem lezten Abstich des Abends werden alle Hähne der
Windleitungen über Nacht geschlossen.
In sieben Operationen, am 27., 28. und 29. Sept. 1843, wurden im Ganzen 6600 Kilogr.
Roheisen verarbeitet, dabei in 34 1/2 Arbeitsstunden 296,8 Kil. Erzzuschlag und 3780
Kil. Steinkohlen consumirt und 6013,8 Kil. Weißeisen ausgebracht. Vergleicht man
jedoch die einzelnen Operationen, so ergibt sich, daß
zuerst der Erzzuschlag nach der Natur des Roheisens sehr veränderlich ist und unter
sonst gleichen Umständen, so wie auch die Dauer des eigentlichen Weißmachens, in
stärkerem Verhältnisse wächst, als die Größe des Eiseneinsazes. Die Kohlenconsumtion ist natürlich bei
der ersten Operation an jedem Tag am stärksten und würde sich bei continuirlichem
Betrieb, so wie durch Verminderung der Höhe des Ofengewölbes und des Fuchses noch
sehr vermindern lassen; auch könnte man die durch den Fuchs strömenden Flammen zum
Vorwärmen des Eisens und zu Erhöhung der Windtemperatur zwekmäßig benuzen.
Das geweißte Eisen ist theils ganz weiß, körnig-blätterig, theils graulich und
sehr feinkörnig; lezteres verpuddelt sich besser, obwohl etwas langsamer. Man
verpuddelt 200 Kil. in 1 3/4 bis 2 Stunden mit 11–13 Proc. Verlust. Die unter
einem Stirnhammer gezängten Luppen werden ohne nochmalige Erhizung zu flachen
Stangen ausgewalzt, dann zerschnitten und, in Paketen erhizt, zu Schienen gewalzt.
Dieses Stabeisen ist außerordentlich zäh und von vorzüglicher Qualität.
Im Oktober 1843 beabsichtigte man noch zwei andere Gas-Weißöfen auf
Königshütte zu errichten; das Gleiche auf Laurahütte. Auf der damals noch im Bau
begriffenen Alvensleberhütte sollte der Gaspuddelproceß versucht werden.
Tafeln
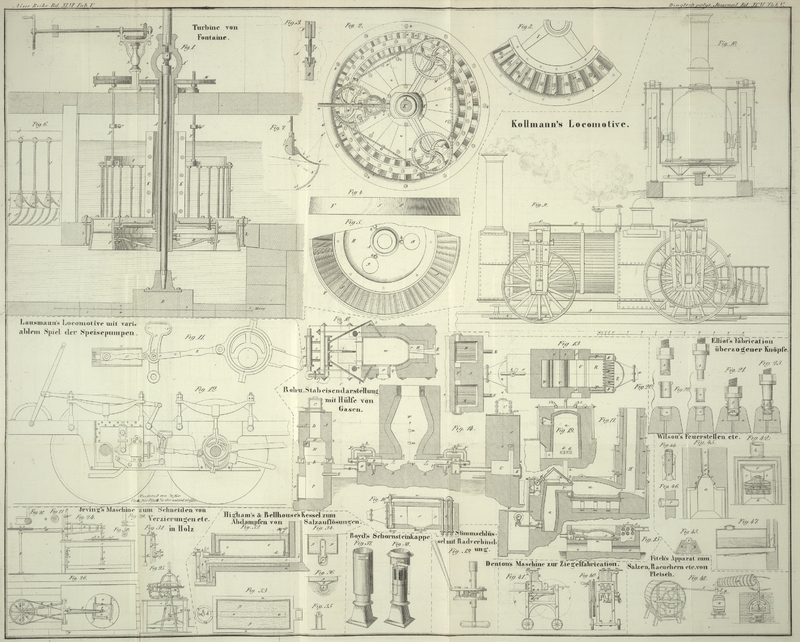